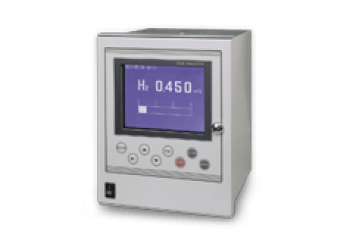
Les procédés de traitement thermique nécessitent une atmosphère contrôlée avec précision pour que le processus soit réussi.
Ces procédés du métal sont souvent utilisés pour fabriquer des pièces critiques en alliages spéciaux pour des industries telles que l’aérospatiale, l’automobile, la pétrochimie ou l’énergie nucléaire. Un mauvais contrôle de l’atmosphère du four peut altérer la qualité des alliages et engendrer des conséquences financières et sécuritaires.
Comment assurer un traitement thermique efficace dans une atmosphère contrôlée ?
Si l’atmosphère du four de traitement thermique n’est pas contrôlée, l’alliage peut être contaminé. Cela peut entraîner une perte de résistance et de ductilité, ainsi qu’une augmentation de la fragilité. La microstructure de l’alliage peut également être affectée, ce qui entraîne une mauvaise stabilité dimensionnelle et une réduction de la durée de vie. En outre, les atmosphères non contrôlées peuvent provoquer de la corrosion et d’autres formes de dommages à l’alliage.
Dans certains cas, la contamination peut même provoquer la fissuration ou la rupture de l’alliage.
Une atmosphère contrôlée est essentielle pour un traitement thermique efficace. En empêchant la contamination, elle garantit que l’alliage traité conserve ses propriétés.
C’est particulièrement important dans les industries de l‘automobile, de la chimie et de l’énergie nucléaire, où les conditions suivantes sont réunies :
L’absence d’atmosphère contrôlée peut entraîner des réactions chimiques à la surface de l’ensemble métallique à traiter thermiquement, compromettant sa qualité et ses performances et conduisant à des pièces rejetées.
De telles conditions entraînent des pertes financières, des pertes de temps et des répercussions potentiellement dangereuses pour le client qui utilise la pièce sans détecter la faiblesse. En outre, une atmosphère mal contrôlée peut conduire à un four endommagé ou, pire encore, à des employés blessés.
Un four de traitement thermique à atmosphère contrôlée fournit un environnement optimal pour les composants métalliques pendant le processus de traitement thermique.
En contrôlant soigneusement la composition et le débit du gaz à l’intérieur du four, on obtient un contrôle précis de la température et une oxydation ou une décarburation minimale.
Il en résulte une amélioration de la qualité et de la cohérence du produit, ainsi qu’une augmentation de l’efficacité de la production.
Afin d’assurer un traitement thermique efficace en atmosphère contrôlée, il est important de surveiller et de contrôler soigneusement les paramètres suivants :
En contrôlant soigneusement ces paramètres, il est possible d’obtenir un traitement thermique précis dans une atmosphère contrôlée, ce qui se traduit par l’amélioration de la qualité et de la cohérence des produits.
Les gaz inertes les plus couramment utilisés dans les procédés de traitement thermique sont l’argon (Ar), l’hélium (He) et l’azote (N₂).
La mesure dans laquelle une atmosphère peut être qualifiée d’inerte, dépend de facteurs tels que le type de gaz, son niveau de pureté, les températures concernées et le matériau traité. En fonction du gaz ou du mélange de gaz utilisé, le procédé sera dédié à différents types de traitement thermique : recuit, trempe neutre, revenu, nitruration, frittage ou brasage.
Les analyseurs de gaz Fuji Electric sont utilisés pour contrôler l’atmosphère dans tous ces procédés, avec des capacités de mesure rapide et précise de ratios tels que Ar/He, Ar/N₂, He/N₂, H₂/Ar ou H₂/N₂.
Ce dernier est nécessaire pour contrôler une atmosphère riche en hydrogène. Celle-ci est mise en œuvre pour réduire l’oxyde de fer en fer et décarburer l’acier. Il contribue aussi efficacement au transfert de chaleur et peut réagir avec une présence d’oxygène.
La solution Fuji Electric pour contrôler le H₂/N₂ est une armoire industrielle compacte intégrant :
Prenons l’exemple suivant :
La conductivité thermique étant variable d’un composant à un autre, tout changement de la concentration du composant mesuré entraîne une variation de la conductivité thermique du gaz échantillonné, laquelle affecte la température du fil de platine.
L’analyseur se base sur ces variations de température pour déterminer la teneur en gaz.
Le gaz du four est extrait en continu par une sonde de prélèvement chauffée et filtrée. Il est ensuite acheminé par une ligne d’échantillonnage chauffée jusqu’à l’armoire compacte murale.
Celle-ci intègre l’analyseur de conductivité thermique TCD et l’ensemble du système d’échantillonnage spécialement conçu pour assurer la sécurité de l’analyseur et garantir une mesure précise, représentative et fiable de la concentration en H₂.
Télécharger votre fiche d’application et contrôlez avec précision l’atmosphère du fours lors d’un traitement thermique !