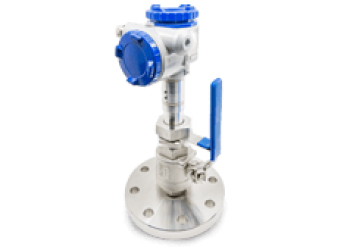
L’ingénierie de l’instrumentation et du contrôle-commande se concentre sur la conception, la configuration et la maintenance des systèmes d’automatisme industriel qui contrôlent et surveillent les machines et les processus au sein des industries. Cette branche de l’ingénierie garantit que les processus fonctionnent efficacement, en toute sécurité et de manière rentable en utilisant une variété d’instruments de mesure et de systèmes de contrôle-commande.
L’objectif principal dans ce domaine est de maintenir la stabilité et d’améliorer les performances de l’ensemble du système grâce à des mesures et un contrôle précis.
Les instruments utilisés par les ingénieurs de contrôle-commande comprennent des instruments de mesure tels que des capteurs, des détecteurs et des transmetteurs. Ceux-ci sont essentiels pour collecter des données concernant la température, la pression, le débit, le niveau et d’autres variables critiques du processus. Ces données sont ensuite analysées et manipulées pour gérer et optimiser les opérations industrielles.
Des systèmes de contrôle-commande, englobant à la fois le matériel et le logiciel, sont mis en œuvre pour traiter les données collectées et exécuter des actions basées sur des paramètres prédéfinis. Ces systèmes peuvent aller de simples contrôleurs locaux à des systèmes de contrôle en réseau complexes qui automatisent des lignes de production ou des processus entiers.
Le rôle d’un ingénieur en instrumentation et contrôle-commande est vital pour un large éventail d’industries, notamment la fabrication des produits pharmaceutiques ou chimiques et la production d’énergie. Dans ces environnements, ils travaillent au développement et à la maintenance de systèmes qui visent la précision, l’efficacité énergétique et la sécurité.
Grâce à l’application de technologies modernes et de stratégies innovantes, l’ingénierie industrielle de l’instrumentation et du contrôle-commande contribue de manière significative à la fiabilité et à la qualité des opérations industrielles, ce qui est essentiel dans le paysage concurrentiel du marché actuel.
L’ingénierie de l’instrumentation et du contrôle-commande fait partie intégrante du fonctionnement efficace des processus dans diverses industries. Il comprend des systèmes et des instruments conçus pour mesurer et contrôler des grandeurs physiques afin d’assurer des performances et une sécurité optimales.
Une formation en génie électrique est courante chez les ingénieurs en instrumentation, soulignant la nature interdisciplinaire du domaine.
Les systèmes de contrôle-commande sont fondamentaux sur le terrain, avec pour objectif principal de maintenir les variables de processus dans les limites souhaitées. Ces systèmes s’appuient sur des boucles de rétroaction pour comparer les conditions réelles avec les points de consigne et ajuster les variables si nécessaire.
Dans le contexte de l’ingénierie de l’instrumentation, les systèmes de contrôle « font référence » à l’utilisation d’instruments de contrôle de processus et d’outils logiciels pour l’analyse, la mesure et le contrôle des variables de processus industriels.
Cela comprend le dépannage des systèmes de contrôle et la sélection et la documentation de divers instruments tels que les instruments de débit, de niveau, de température et de pression. Une régulation appropriée est essentiel pour la stabilité, les performances et la sécurité du système.
Dans le domaine du contrôle des procédés, l’instrumentation comprend des dispositifs tels que des transmetteurs, des régulateurs PID, des automates et des actionneurs, ainsi que des instruments de contrôle des procédés. Ces composants fonctionnent ensemble pour mesurer et modifier les variables du processus telles que le niveau, la pression et le débit, garantissant ainsi la fiabilité et la conformité aux normes de sécurité.
Les régulateurs et automates interprètent les données des capteurs et signalent les actionneurs pour effectuer les ajustements nécessaires, maintenant ainsi le processus dans les paramètres spécifiés. Des outils logiciels sont utilisés parallèlement à ces instruments pour améliorer l’analyse et le contrôle des variables des processus industriels.
L’instrumentation et la régulation des process sont essentielles dans les industries dans lesquelles un contrôle précis de variables telles que la température, la pression et le débit est essentiel. Ils garantissent l’efficacité, la qualité des produits et la conformité réglementaire tout en réduisant les déchets et de potentielles situations dangereuses.
Les ingénieurs en instrumentation et contrôle commande sont essentiels à la conception et à la maintenance des systèmes dans les installations de fabrication, assurant la bonne production des marchandises et le développement de mécanismes complexes.
Les capteurs sont les yeux et les oreilles des systèmes de contrôle, convertissant des quantités physiques en signaux électriques. Ils sont essentiels pour la surveillance et le contrôle des variables des processus industriels telles que la température, la pression, le débit et le niveau, qui sont essentielles pour assurer l’efficacité et la sécurité des opérations.
Les technologies de mesure vont du simple thermocouple pour la température, en passant par les capteurs de pression pour la pression, les sondes de niveaux pour la mesure de niveau niveau, jusqu’aux débitmètres ultrasoniques plus complexes pour la mesure du débit.
Le choix de la technologie des capteurs a un impact sur la précision, la fiabilité et la portée des mesures, ce qui rend essentiel la sélection des capteurs appropriés pour surveiller ces variables de processus industriels.
Les instruments de mesure de niveau maintiennent l’équilibre des matières premières dans des processus tels que dosage chimique. Les technologies varient de simples interrupteurs à flotteur, capteurs de niveau hydrostatiques, aux sondes de niveau radar, qui peuvent mesurer les niveaux de solides et de liquides dans des conditions extrêmes sans contact.
La mesure du débit est indispensable pour réguler le taux de transfert de matière ou d’énergie. Les instruments comprennent des débitmètres à pression différentielle, des débitmètres électromagnétiques, des débitmètres à ultrasons, des débitmètres Coriolis, chacun adapté à des types particuliers de fluides allant des liquides aux gaz et aux boues.
Les instruments de mesure de pression sont essentiels pour la sécurité et le contrôle des processus.
Ils comprennent des manomètres, des transmetteurs de pression et des pressostats. Ces appareils peuvent aller de capteurs analogiques à des capteurs numériques très sophistiqués pour mesurer des niveaux de pression (relative, différentielle ou absolue) statiques ou dynamiques.
La température est un paramètre couramment surveillé. Les instruments comprennent des sondes thermocouples, des sondes de température à résistance (RTD) et des sondes de température infrarouges.
Le choix dépend de facteurs tels que la plage de température, la précision requise et les conditions environnementales.
Les instruments d’analyse des gaz comme les chromatographes, les analyseurs de gaz laser et les analyseurs de gaz infrarouges, détectent et quantifient la composition des gaz.
Ils sont essentiels dans la surveillance des émissions atmosphériques, le contrôle des process et pour assurer la sécurité dans les environnements de travail où des gaz dangereux peuvent être présents.
Dans le domaine de l’ingénierie de l’instrumentation et du contrôle, la conception des systèmes numériques de contrôle-commande et leur intégration sont essentielles pour assurer la fiabilité et la sécurité de la fabrication et de la régulation des process.
Les machines de contrôle jouent un rôle central dans l’automatisation des processus au sein de divers systèmes d’ingénierie, améliorant la surveillance et le contrôle des machines dans les installations, en particulier dans des industries comme l’hydroélectricité.
De plus, les équipements de contrôle des process sont essentiels à l’efficacité et à la productivité des équipements de production, fournissant des systèmes d’instrumentation et de contrôle industriels qui prennent en charge le fonctionnement transparent des process de fabrication.
La conception de systèmes numériques de contrôle-commande (SNCC, ou DCS pour distributed control system en anglais) est une entreprise complexe qui implique l’élaboration de spécifications pour les boucles de contrôle et de régulation, garantissant que l’équipement répond aux exigences précises de l’automatisation.
Dans cette phase, les principes d’ingénierie des systèmes sont appliqués pour générer des architectures électriques et électroniques à la fois robustes et évolutives.
Les ingénieurs doivent évaluer des facteurs tels que le temps de réponse, la fiabilité et la stabilité du système.
Temps de réponse
Fiabilité
Stabilité du système
L’ingénierie de l’instrumentation se concentre sur l’intégration transparente de la technologie pour mesurer et contrôler l’environnement de fabrication. Cette intégration doit être exécutée avec un haut degré de précision pour faciliter un contrôle précis du processus.
Les éléments clés sont les suivants :
Les normes ISA (International Society of Automation), les normes IEC (International electrotechnical commission), et les normes ISO sont souvent citées en référence pour guider l’intégration de ces éléments.
L’infrastructure dans l’automatisation industrielle transmet les cadres physiques et logiques qui soutiennent la technologie opérationnelle. La conception de cette infrastructure doit tenir compte des besoins actuels tout en étant adaptable aux progrès technologiques futurs.
Les principales considérations sont les suivantes :
Évolutivité
Interopérabilité
Sécurité des réseaux et des données
L’ingénierie de l’instrumentation et du contrôle-commande a évolué avec l’intégration de technologies avancées, améliorant la productivité, l’optimisation et la stabilité du système. Ces technologies tirent parti des communications numériques, des microprocesseurs, de l’IA et de l’apprentissage automatique pour créer des systèmes de contrôle plus efficaces et plus réactifs.
Les systèmes de communication industriels sont essentiels pour permettre un échange efficace de données entre les différents dispositifs de contrôle.
Les réseaux numériques utilisent des protocoles de communication industriels comme Ethernet/IP, EtherCat, FOUNDATION™ Fieldbus, Profibus, Profinet, CANopen, DeviceNet, CC-Link et Modbus TCP/IP qui sont courants et succèdent au signal 4-20mA avec HART™. Ils offrent des communications à haut débit et une interopérabilité entre différents équipements, tels que des capteurs et des transmetteurs.
Les protocoles de communication sans fil tels que le WirelessHART™ ou LoRA sont déployés dans l’industrie notamment pour les instruments de mesure de l’énergie.
Cette connectivité est essentielle pour que les systèmes de gestion optimisent les opérations et effectuent des analyses de données en temps réel.
Les régulateurs de température d’aujourd’hui intègrent des microprocesseurs pour une régulation précise et rapide de la température.
Ces régulateurs PID utilisent des signaux analogiques et numériques pour surveiller et ajuster la température afin de maintenir les points de consigne souhaités.
Cette précision assure la stabilité des processus dépendants de la température, ce qui a un impact direct sur la productivité.
Les IHM (Interface Homme Machine) modernes ont transformé l’interaction entre les humains et les machines. Avec l’intégration de la technologie des écrans tactiles et des interfaces personnalisables, les IHM sont devenues plus conviviales.
De plus, les IHM avancées intègrent des éléments d’IA et d’apprentissage automatique, fournissant des informations prédictives et améliorant les capacités de prise de décision.
Les automate programmable industriel (API ou PLC en anglais) et les systèmes de supervision SCADA (système de contrôle et d’acquisition de données) sont l’épine dorsale de l’ingénierie I&C moderne. Ces systèmes ont évolué avec des microprocesseurs permettant un contrôle et une surveillance plus sophistiqués.
Les automates mettent en œuvre des algorithmes de contrôle et traitent les entrées des transmetteurs, tandis que les systèmes SCADA offrent une vue de haut niveau pour une meilleure optimisation et gestion.
Les stratégies de contrôle avancées utilisent la robotique, l’IA et l’apprentissage automatique pour créer des systèmes de contrôle plus adaptatifs et intelligents. Ces stratégies permettent une optimisation en temps réel et améliorent considérablement l’efficacité des opérations.
La maintenance prédictive et les algorithmes de contrôle adaptatif illustrent la façon dont ces technologies repoussent les limites de l’ingénierie I&C traditionnelle.
L’ingénierie de l’instrumentation et du contrôle (I&C) est un domaine aux multiples facettes qui progresse continuellement grâce à l’innovation, à l’amélioration des processus industriels et de la production.
Cette section se penche sur les éléments essentiels du développement professionnel au sein de cette discipline et examine les tendances prédictives qui façonnent son avenir.
Les ingénieurs contrôle-commande et instrumentation jouent un rôle fondamental dans la maintenance et le développement de systèmes de machines complexes. Leur rôle dépasse souvent les frontières du génie électrique et électronique, ce qui nécessite une compréhension approfondie des deux.
Le parcours pour devenir un ingénieur en instrumentation estimé implique un engagement à rester informé dans ce domaine dynamique. Cela inclut le respect des normes de l’industrie établies par des entités faisant autorité telles que l’International Society of Automation (ISA) et le maintien d’un ensemble de compétences à jour grâce à l’apprentissage continu. Le respect de la loi et des règles de sécurité reste une partie intégrante de leur pratique professionnelle.
En termes de progression de carrière, les ingénieurs dans ce domaine peuvent commencer en tant que spécialistes techniques, chargé d’affaires, évoluer vers des rôles de gestion de projet et potentiellement accéder à des postes de direction. Les opportunités de carrière abondent dans des secteurs tels que le nucléaire ou les énergies renouvelables (hydrogène, solaire, biogaz,..) où la demande d’ingénieurs I&C qualifiés pour gérer et optimiser la production est élevée.
L’avenir de l’ingénierie I&C est façonné par un certain nombre de tendances émergentes.
Les innovations technologiques continuent de faire avancer l’industrie. Ils influencent les stratégies de maintenance et optimisent les processus de production.
L’essor de l’instrumentation intelligente et l’intégration accrue avec les technologies de l’information soulignent la nécessité pour les ingénieurs d’avoir une bonne maîtrise des aspects logiciels et matériels du métier.
Dans les environnements industriels tels que le pétrole et le gaz, le nucléaire ou les énergies renouvelables les modèles de maintenance prédictive devraient devenir la norme. Ils réduiront la fréquence des temps d’arrêt imprévus des machines.
Les ingénieurs versés dans la technologie de pointe sont prêts à diriger des projets qui s’inscrivent dans les normes internationales de la pratique de l’ingénierie.
Le rôle de l’ingénieur I&C n’est pas statique. Il évolue en accord avec les progrès technologiques. Cela garantit que les machines et les systèmes de diverses industries continuent de fonctionner avec une efficacité et une sécurité optimales.
Énergie verte
Cybersécurité
Systèmes intelligents