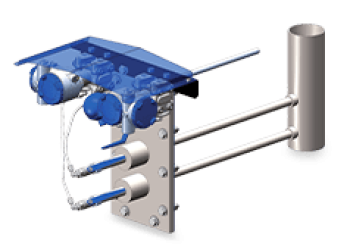
Die Zementherstellung ist ein komplexer Prozess, der Strenge und Genauigkeit erfordert, um Produkte von hervorragender Qualität zu erhalten, die den Umweltstandards entsprechen. Die Überwachung des Zementprozesses mit zuverlässigen Druckmessgeräten, Durchflussmessgeräten und Temperaturmessgeräten trägt dazu bei, die Effizienz zu steigern und gleichzeitig die Lebensdauer der Anlagen zu verlängern. Gasanalysatoren ermöglichen außerdem eine bessere Prozesssteuerung und überwachen gleichzeitig die Emissionen in die Atmosphäre.
Die Messgeräte von Fuji Electric begleiten die Zementhersteller während jeder Phase des Herstellungsprozesses, um :
Kontrolle der Zementqualität
Umweltfreundliche Produktion
Verwaltung von CO2-Emissionen
Energieeffizienz
Zement ist ein wichtiges hydraulisches Bindemittel im Bauwesen, das aus gemahlenem Klinker hergestellt wird. Dieser Klinker wird durch das Brennen einer Mischung aus Kalkstein und Ton bei sehr hohen Temperaturen gewonnen. Die Herstellung von Zement ist ein komplexer Prozess, der mit der Zerkleinerung der Rohstoffe beginnt, gefolgt von deren Brennen in einem Drehofen bei Temperaturen von bis zu 1450 °C. Durch diesen chemischen Prozess wird die Mischung in Klinker umgewandelt, der dann zur Herstellung von Zement fein gemahlen wird. Zement wird zum Verbinden von Beton- und Mörtelpartikeln verwendet und ist beim Bau von Gebäuden, Brücken, Straßen und anderen Infrastrukturen unverzichtbar.
Die Rohmühle dient dazu, die Rohstoffe für Zement zu zerkleinern: Kalkstein, Ton, Silikatstein, Eisenoxid, Gips und Sand. Diese Materialien werden zuvor dosiert und dann in der Mühle gemischt. In der Mahlphase wird auch Hochofenschlacke aus Stahlwerken hinzugefügt. Außerdem wird Asche aus Müllverbrennungsanlagen als alternatives Zementmaterial verwendet. Die Rohstoffe werden anschließend mit heißen Gasen getrocknet. Nur ausreichend feines Material kann den Separator passieren und wird zum nächsten Prozess mitgenommen. Das dann gewonnene feine Pulver wird als Rohmehl bezeichnet.
Der elektrostatische Filter wird verwendet , um schädliche Partikel aus dem Gas zu entfernen. Er entfernt feine Partikel wie Staub und Rauch aus dem strömenden Gas, indem er die Kraft einer induzierten elektrostatischen Ladung nutzt, ohne den Gasstrom durch die Einheit zu behindern. Da elektrostatische Filter einen geringen Druckverlust verursachen und dehnbar sind, werden sie häufig in großen Kesseln und Zementwerken eingesetzt. Sie können Gase über 350 °C und sehr feuchte Gase verarbeiten. Er dient als Endfilter, mit dem Partikel bis zu einer Größe von etwa 0,05 µm entfernt werden können.
Die Höhe und Größe des Industrieschornsteins hängt von den emittierten Stoffen, den örtlichen meteorologischen und geografischen Bedingungen sowie den benachbarten Gebäuden ab. Die Emissionen von Verbrennungsgasen und die damit verbundenen Schadstoffe müssen gemäß den geltenden Vorschriften überwacht und gemessen werden.
Das Mehl muss vorgewärmt werden, bevor es in den Drehofen eingefüllt wird. Es wird in die vertikal ausgerichteten Wärmetauscher des Vorwärmers eingeleitet. Das rohe Mehl sinkt in Wirbeln durch die aufeinanderfolgenden Zyklone im Gegenstrom zu den heißen Gasen nach unten. Während die Rohmischung in die Tanks des Vorwärmers hinabsinkt, wird sie mithilfe der dem Drehofen entzogenen Wärme auf 800 °C bis 900 °C erhitzt. Bei diesem Prozess findet eine chemische Reaktion im Rohmehl statt, die die Wirksamkeit der Kalzinierung verbessert. Dieses Vorheizen ist notwendig, um den Leistungskern des Zements zu erreichen.
Die vom Vorwärmer abgegebene Wärme wird in den Heizkessel umgeleitet, der zur Energieversorgung der restlichen Anlagen dient. Wasserrohrkessel: Oben und unten sind zwei Fässer angeordnet, die durch eine Reihe von Wasserrohren miteinander verbunden sind, durch die das Wasser zirkuliert. Die Rohre werden durch die Verbrennungsgase erhitzt, um Dampf zu erzeugen.
Der Drehofen ist ein mit feuerfesten Ziegeln ausgekleidetes Rohr (3-5 m breit und 30-60 m lang), das sich etwa 3-5 Mal pro Minute dreht, wobei das Rohmaterial durch allmählich heißer werdende Bereiche des Ofens in die Flamme fließt. Das Rohmehl wird in der Rotation auf bis zu 1450 °C erhitzt. Anschließend wird es mit kalter Luft abgekühlt, um Zementklinker zu bilden. Die heiße Luft aus dem Kühler wird zum Vorwärmer zurückgeführt, um Brennstoff und Energie zu sparen. Zement oder Kalk hängt vom Herstellungsprozess und den beteiligten Temperaturen ab.
Der Klinker wird wiederum in einer Kugelmühle mit anderen Zusätzen (Asche aus Wärmekraftwerken, Hochofenschlacke oder Gips) sehr fein gemahlen, um eine andere Zementqualität zu erhalten. Der Zement wird dann vor der Auslieferung gelagert.
Die Gasanalyse gewährleistet die Luftqualität in Zementfabriken. Wärmekraftwerke und Drehrohröfen, die bei der Zementherstellung eingesetzt werden, emittieren Treibhausgase, insbesondere CO2, die zum Klimawandel beitragen. Mithilfe von Gasanalysen ist es möglich, diese Emissionen zu messen und Strategien zu entwickeln, um sie zu reduzieren. Beispielsweise werden kohlenstoffarme Zemente unter Verwendung alternativer Materialien und effizienterer Herstellungsverfahren produziert, wodurch die CO2-Emissionen gesenkt werden. Dies ist entscheidend, um Umweltstandards zu erfüllen und eine nachhaltigere Zementproduktion zu fördern.
Erfahren Sie, wie Gasanalysatoren bei der Reduzierung von Schadstoffen helfen und die Entwicklung sauberer Energien für eine nachhaltige Umwelt fördern.
09. Juni 2024