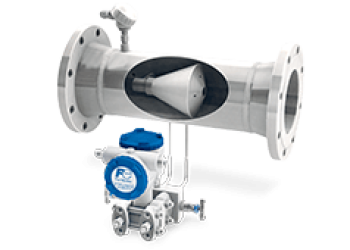
As a district heating operator, your energy performance is a key issue for your company.
Your steam output fluctuates according to demand and seasonality. You may need to supplement your steam with steam from another production site. Optimising the consumption of this steam is a challenge.
Choose the most effective solution to measure your steam production, maximize your energy efficiency and increase your profitability.
For several years now, the irremediable depletion of fossil fuels and the urgent need to slow down global warming have led us to rethink the energy mix.
District heating, also known as heating and cooling networks, is part of this ecological transition, saving over 6 million tonnes ofCO2 in France every year.
By 2035 in France, the aim is to triple the number of households connected to heating networks.
To meet this demand, district heating operators are expanding their networks to optimize the energy performance of their sites, while offering their customers attractive prices.
A heat networks operator provides heating to customers in Paris, France, through a system of steam boilers.The flow of steam fluctuates according to customer demand and seasonality.
Heating demand is high in winter and low in summer.
The metering application is measuring steam flow at 202°C produced by gas and biomass boilers.
During boiler shutdowns or power shortages, steam is supplied from another production site.
This requires bi-directional measurement to measure steam in both directions over wide flow ranges.
In order to save energy, the heating operator wants to minimise the pressure losses of the future meters.
Difficult flow applications require close collaboration between the meter manufacturer and the end-user to fully understand the process operating conditions, noise, and vibration of the surrounding machinery.
The V-Cone® differential pressure flowmeter was chosen for this project because the lack of straight lengths required. Optimised for confined spaces, the V-Cone® flow meter was easily integrated into the existing configuration, eliminating the need for re-piping. Orifice plates and vortex flow meters could have measured steam flow in this situation. However, the straight length requirements of orifice plates would have required modifications and additional pipe lengths.
The wide flow range of the application would have required two vortex flow meters. Both solutions would have resulted in significant additional pressure losses and costs that would have been unacceptable to the heating district operator.
The V-Cone® technology claims a rangeability of 10:1. In this application, 4 pressure transmitters differentials were used to accurately measure the desired flow range (20:1) in both directions.
The Fuji Electric solution also included pressure measurement, temperature measurement, box-mounted energy flow computers cabinets, and accessories: condensate pots and isolation valves.
Overall, the V-Cone® flow meter proved to be an ideal choice for accurate measurement over a wide range of bi-directional flow.
Since 2016, the V-Cone® flow meter has been certified in the ISO5167-5 standard, which allows it to be used for custody transfer metering.
The versatility of the V-Cone® flow meter for a wide range of flow and fluid conditions, as well as the ability to customise, make it a viable and sustainable solution for many new and retrofit flow measurement applications.
Another advantage of this measurement is that it can be calibrated on-site without the need for removing the flow meter and without stopping steam production.
After the success of this challenging measurement, the heating operator decided to install similar measurement devices for hot condensate returns.
Download your application sheet and optimize your energy performance today!