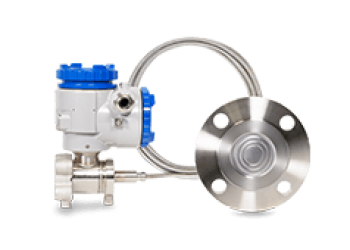
Diaphragm seal gauge pressure transmitter - FKB
ref : FKBFrom
2725,00 € Request a quoteThe high temperatures and pressures, corrosion and crystallisation inherent in the urea manufacturing process can put a strain on even the most reliable pressure measurement equipment and quickly render it inoperative.
In this article, learn about a diaphragm seal that is strong enough to protect relative, absolute and differential pressure transmitters from the the harsh environments encountered in urea fertilizer production.
Organic farming dreamed of chemical-free crops that would preserve our health and our environment. Today, the dream of the 1980s is coming up against the reality of the soil: without help, the land is depleted.
The Food and Agriculture Organisation of the United Nations (FAO) estimates that food production will have to increase by 70% to feed the additional 2.3 billion people on our planet by 2050.
At the same time, the area of cultivated land is constantly decreasing.
Cultivated agricultural land accounted for 5 billion hectares worldwide. But every year, more than 3 million hectares are severely degraded.
Today, nearly 5 million hectars of our arable land are lost yearly.
The number of people is expected to reach 9.7 billion by 2030 and more than 11 billion by 2100.
This demographic pressure has led the agricultural world in recent years to increase the yield of arable land. This is a more environmentally friendly method.
Compared to the old agricultural practices, which are responsible for more than 80% of the world's deforestation. Every year, 51,600 square kilometres of forest were lost: the equivalent of the size of Costa Rica!
Add to this a demand for biofuels (albeit declining) and the global market for mineral fertilisers is expected to reach USD 143.34 billion by 2028.
Today, the need for mineral fertilisers is exploding on every continent!
Urea production is becoming a critical issue, even as global urea production approaches 200 million tonnes per year, with demand surging since the beginning of the year.
With the rise in agricultural commodity prices, countries such as Australia and Korea find themselves on the brink of collapse.
And it is unlikely that the global tension will subside before 2023.
Optimising output and increasing the efficiency and profitability of production units becomes a major challenge for the plant manager when faced with the inevitable trade-off of meeting increased urea demand: Synthesise more products in an attempt to increase production at the risk of compromising plant efficiency and product quality, or maximise urea quality at the expense of volume and yield.
This is a real challenge for the maintenance manager, who has to anticipate problematic, long and costly plant shutdowns, which are nevertheless essential to ensure the sustainability and safety of the installations, to keep all the equipment running at optimum efficiency and to limit maintenance periods.
It's also a constantly renewed challenge for the instrumentation manager who must adapt to the extreme conditions and dangers inherent in urea production.
The challenge is complicated by the constantly changing technologies and materials that must be chosen to avoid the risk of breakdowns and forced plant shutdowns.
Improving the reliability of manufacturing processes, avoiding production stoppages and guaranteeing the safety of installations is particularly difficult in these conditions.
And those responsible for increasing overall efficiency and keeping plants running are under great pressure due to the complexity of the urea manufacturing process, which is very aggressive on equipment.
Although the approaches to urea processing differ from plant to plant, the production process is common to all.
It starts with the high-pressure synthesis of ammonia and carbon dioxide. There are two main reactions:
The residual ammonium carbamate is first separated from the urea-water mixture in a high-pressure extractor and then in a recirculation stage.
The water is then expelled in the evaporation stage to form urea melt. Finally, the molten urea undergoes a granulation process to obtain a final solid urea product of the desired quality.
Each urea production process presents unique safety, reliability and efficiency challenges that compel plant managers to improve the performance of their facilities for a safer, more reliable and more environmentally friendly fertiliser industry.
This can only be achieved with innovative, high-performance equipment and measuring instruments, specially designed and manufactured with materials that can withstand corrosive environments and ensure long service life.
Material selection is therefore vital at the design stage of equipment and measuring instruments. Poor material selection can lead to catastrophic failures, plant shutdowns, and even loss of life.
The materials used for pressure transmitters, as well as the choice of sensor technology, play a very important role in the fertiliser industry, particularly in the urea industry.
Just like strippers, scrubbers and the reactor of your plant, urea measuring instruments are subject to chemical attack by ammonium carbamate, which causes accelerated degradation of the components in contact with this highly corrosive agent.
Conventional materials for the thin diaphragm of a pressure transmitter's measuring cell do not protect against erosion, corrosion and the mechanical stresses inherent in the urea manufacturing process.
By using urea grade 1.4466 stainless steel, existing urea processes can then achieve a higher level of performance, resulting in energy savings and an increased level of safety due to (for example) a reduced need for passivation.
However, the measuring cell and electronic components used to manufacture pressure transmitters cannot withstand the high temperatures of the process fluid.
That's why it's so important to use diaphragm seals membranes.
The pressure transmitters urea grade 1.4466 austenitic stainless steel diaphragm seals offered by Fuji Electric are, in the majority of cases, the best choice for use under normal urea production process conditions for pressures up to 26 bar (377 psi) and temperatures up to 180°C (356° F).
Above these conditions, the use of zirconium or tantalum diaphragm separators may be required for more critical measurement points.
The use of a 1.4466 austenitic urea grade steel increases the corrosion resistance of the fertilizer plant pressure transmitter , resulting in:
50 YEAR GUARANTEE
MAXIMUM SAFETY
RELIABLE, ROBUST DESIGN
The 1.4466 - 25.22.2 - 310MoLN - S31050 - 2RE69 urea grade steel used to manufacture the separators and diaphragms of Fuji Electric's urea pressure transmitters is a fully austenitic stainless steel with very low carbon and impurities.
Practical experience has confirmed its excellent resistance to urea (ammonium carbamate) corrosion at high pressures and temperatures.
It is also highly resistant to inorganic acids.
This steel grade is characterised by:
Download your application sheet and choose the right measuring instruments for your urea plants!