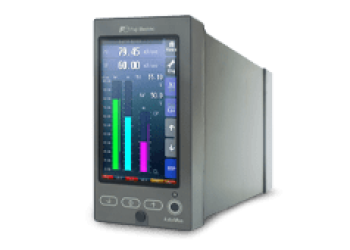
Multifunction controller - PSC100 series - 2 loops
ref : PSC100From
2928,00 € Request a quoteIndustrial steam boilers are essential for process heating and electrical power generation. To reduce energy costs, the efficiency of these systems must be optimised.
Manufacturers and heating operators need to ensure continuous operation to keep plants running and meet customer requirements without interruption.
To improve the performance and extend the life of an industrial boiler, proper operation is essential.
Let's take a look at how to improve the performance of your industrial boiler and extend its life.
Industrial boiler drums are used to generate steam at high pressure.
They are usually installed in factories to produce the thermal energy for industrial heating processes, cleaning or hydration processes, or to generate electricity in power plants.
A drum is a large, cylindrical container that holds either boiling water or steam. It’s often placed on its side and located near the top of a boiler.
Its primary purpose is to either feed an industrial process or to provide power for a steam turbine so it can generate electricity.
Keeping the water level precise in the drum is vital for both safe boiler operation and efficiency.
If the water level is too high, it causes flooding and gets in the way of separating moisture from steam in the drum. However, if it’s too low, then conversion efficiency suffers and even exposed or damaged boiler tubes are possible. Usually, this requires maintaining a narrow range for optimal results.
Steam flow and feed water flow are two elements that affect the level of the storage tank. By adding these to the element of drum level, we are able to maintain a much steadier and controlled water level in the boiler. This particular control strategy is known as ‘three-element control’.
The control of the drum level is also called «feedwater control», as its purpose in a drum boiler is to maintain a constant water level in the drum.
Multi-function process controllers: a reliable and cost-effective solution for controlling the level of industrial steam boilers and achieving stable and accurate drum level control.
The primary goal of drum level control is to change the feedwater flow in reaction to water level feedback so that the height remains consistent. Water flow is usually adjusted by speeding up or slowing down a feedwater pump, or by opening/closing a valve.
The feedback control explained above is acceptable if the boiler load (steam demand) is stable. However, a sudden change in load causes a transient disturbance called "inverse tank level response", which disrupts its stability. To ensure close control under stable, transient conditions, the steam outlet flow rate, the cause of the disturbance, is measured before any level change, and used to directly manipulate the feedwater. This is known as "two-element control".
Additionally, the feedwater flow control loop added in cascade from the drum level control loop improves controllability and eliminates the effects of feedwater pressure variation.
The addition of these three elements - (1) drum level, (2) steam flow and (3) feedwater flow - enables the controller to foresee how much water needs to be added to the drum, despite any disturbances, thus maintaining an even drum level.
Figure 1 shows an example of the PSC210 function block combinations for the three-element boiler drum control.
The PID control block output (MV) of the drum level control loop (LIC) is provided as the setpoint (SP) of the second PID control block for the feedwater flow control loop (FIC) in cascade. The LIC output (MV) is added to the steam flow to compensate for its variations (feedforward control).
The PSC210 controller model is particularly suitable for use in a critical control loop, such as for boilers, due to its backup and manual control functions.
It also has Modbus/TCP communication capability for remote monitoring and control of boilers from a SCADA system.
The PSC100/200 series controllers can provide extended software function blocks of addition/subtraction and offset/shift calculation in addition to PID control, to realise sophisticated control such as three-element drum level control.
With the three-element boiler drum level control available on the SC100/200 Series multifunction PID controllers, manufacturers and operators have an effective way to optimise their steam boiler efficiency and increase the lifespan of their equipment.
Operating costs are reduced and your investment is protected.
A sudden increase in load (steam output flow) causes a decrease in pressure in the drum.
This, in turn, makes the bubbles in the generating tubes expand and move the water towards the drum- giving a false indication of trends regarding true water level changes happening within the said drum. The effect reverses as soon as the load decreases again. Similarly, adding feedwater causes the water level to temporarily decrease due to the contraction of cooled bubbles. This is known as the «reverse response of the drum level. ». To compensate for this effect, controllers will increase the amount of feedwater when load increases.
The Fuji Electric regulator temporarily increases the feed water to compensate for this effect when the load increases.
Download your application form and find out how to save energy right now!