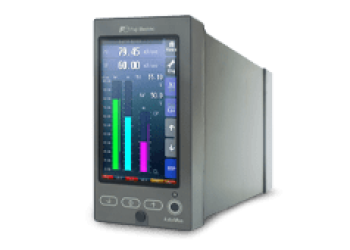
Multifunction controller - PSC100 series - 2 loops
ref : PSC100From
2928,00 € Request a quoteIndustrial boilers are necessary to provide citizens and businesses with heat, electricity and hot water, but they can have a significant impact on operational costs as well as on the environment.
In order to increase energy efficiency, minimise fuel consumption, improve profits while ensuring safety and environmental preservation; operators need to optimise the combustion process in their industrial boiler rooms.
Discover the solution in this article.
A boiler is a closed vessel in which water or other fluid is heated. The heated or vaporised fluid exits the boiler for use in various heating processes or applications, including power generation in which pressurised steam is used to revolve a turbine, and heating for use as a reactant or diluent in a production vessel, or heating for building air conditioning.
The boiler’s burner burns the fuel fed together with air to generate steam. It is necessary to regulate the air/fuel mass in order to maintain a constant ratio of the mixture.
In actual applications, however, steam loads can vary significantly and unpredictably over time. Either air or fuel flow may be delayed in tracking such changes, resulting in a temporary imbalance of the air/flow ratio.
Too much fuel or air can cause environmental and safety problems and reduce the energy efficiency of the boiler.
Insufficient air leads to unburned fuels (fuel, soot, smoke and carbon monoxide), while too much air leads to heat loss due to increased flue gas flow, which reduces the overall efficiency of the boiler in terms of fuel-to-steam ratio.
Multi-function process controllers for boilers: reliable and cost-effective solution to regulate the combustion of your industrial boiler and maintain the expected operational efficiency.
Combustion control with «cross-limit ratio» logic is used to prevent the ratio feeding the burner from becoming too rich (too much fuel) or too lean (too much air) when operating conditions change.
An example of a control loop configuration with the cross-limit architecture is shown in Figure 1.
When the firing demand is stable, the air/fuel ratio is balanced by the ratio setting (× μ). The high select override (high selector) and the low select override (low selector) block the current air/fuel flow signals added with the positive and negative biases (+β, −β) to prevent them from affecting each of the flow controllers.
When the firing demand increases (steam pressure decreases), the main steam pressure controller increases its output C to compensate. At this point, the setpoint signal to the fuel flow controller is limited to the maximum value A (air flow + β1) by the low selector. It only increases by the value of the bias β1, unless the airflow increase is greater. On the other hand, the high selector transmits the same signal C directly to the ratio setting (× μ), so that the airflow mass is always increased before the fuel, to avoid the emission of carbon monoxide and unburned fuel, which is harmful to the environment. At the same time, it is limited to a maximum value of D (fuel flow + β3) to avoid too much energy loss due to the additional heating of the exhaust air through the stack. In this way, the fuel flow and the air flow limit each other and increase stepwise.
If the firing demand decreases, the low selector transmits the signal C so that the fuel flow rate decreases proportionally, but the air flow rate cannot go below the value B (fuel flow rate -β2) by the high selector override, so the mass of the air flow rate always decreases behind the fuel flow rate to avoid black smoke.
The PSC210 multi-function process controllers are suitable for use in a critical control loop, such as for boilers, due to their backup and manual control functions.
Its extensive software function blocks of signal selection, addition/subtraction and leag/lag computation in addition to PID control allow for sophisticated control such as ratio with cross-limit override. It also has Modbus/TCP communication capability to realize remote monitoring and control of boilers from a SCADA system.
Combustion ratio control with cross-limit override available on PSC100/200 series multifunctional PID controllers provides plant managers with an effective means of optimizing steam boiler operation. Fuel consumption is reduced and the environment protected.
The PID controller is used to regulate the main steam pressure (P). The MV (output value) of the controller is called the Boiler Master signal.
The Boiler Master signal is provided as the SP (setpoint) of the PID to control the fuel flow mass. The cross-limit strategy does not affect the control action when reducing the SP, but limits it within a certain range when increasing the SP.
The boiler master signal multiplied by the preset air/fuel ratio is provided as the SP (setpoint) of the PID to control the airflow mass. The cross-limit strategy limits the deviation of the SP within a certain range in both directions to ensure that a sudden operational change does not result in incomplete combustion, by temporarily supplying additional air to the burner until equilibrium is restored. The air flow increases ahead of the fuel flow with higher ignition demand, while it decreases behind the fuel with lower demand.
Download your application sheet and improve the combustion and safety of your industrial boiler!