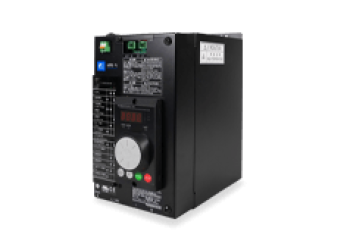
The food industry faces major challenges in terms of hygiene, product quality and the reduction of greenhouse gas emissions. The transition to electrification of cooking and sterilization processes, in particular with the use of professional electric ovens, represents an effective solution for meeting these requirements while saving energy.
Fuji Electric offers advanced scr (silicon controlled rectifiers) power controllers that optimize these processes, ensuring cleaner, safer and more sustainable production for food companies.
The agri-food industry occupies a central position in the global economy, but it is also one of the most energy-intensive sectors, with significant impacts on the environment. According to the International Energy Agency, this sector consumes around 25% of the total energy used worldwide, making it one of the main contributors to greenhouse gas emissions, a key factor in climate change.
In Europe, where science and research on environmental impact are highly developed, the stakes are even more pressing, as companies have to comply with ambitious carbon neutrality targets set for 2050. This energy transition calls for an in-depth overhaul of industrial processes to meet the challenges posed by climate change.
The food industry is faced with a double constraint: not only do they have to reduce their energy consumption to reduce their carbon footprint, but they also have to comply with strict health standards that guarantee the quality and safety of food products. In an environment where economic conditions are marked by steadily rising energy costs, these challenges are becoming increasingly complex to manage. This situation is forcing companies to rethink their production methods, taking into account not only economic aspects but also environmental imperatives.
The electrification of industrial heating applications is an essential solution to these challenges. By replacing gas-fired heating systems with electrical technologies, food industries can not only drastically reduce their CO2 emissions, but also improve the energy efficiency of their operations. These technological advances, supported by environmental science, also make it possible to meet regulatory requirements while maintaining the sector's economic competitiveness, and contributing to a more sustainable future.
Today's agri-food companies face a complex, multi-dimensional challenge: how can they reduce the environmental impact of their production sites while guaranteeing the impeccable quality of their food products? Traditional methods, in particular the use of gas-fired heating systems, pose several major problems that affect the efficiency of industrial activities and the preservation of jobs in this sector.
Not only are these systems responsible for significant CO2 emissions, but they also generate radiant heat that raises the ambient temperature of production facilities. This has a direct impact on food quality, as it can alter texture, flavor and even safety. Production sites are therefore faced with the complex challenge of maintaining optimal conditions while minimizing environmental impact.
In addition, rising ambient temperatures require intensive use of air conditioning to maintain acceptable working conditions, resulting in higher energy costs. This situation creates a vicious circle where inefficient heating systems amplify the need for air conditioning, thus increasing operational costs and the company's overall carbon footprint. For agri-food businesses, this means increased challenges in maintaining competitiveness while meeting environmental expectations.
Another major drawback of gas-fired systems is their lack of precision in temperature control. Temperature variations can lead to quality discrepancies in finished products, which not only compromise customer satisfaction, but also contribute to food waste.
To meet these challenges, companies need to adopt solutions that offer precise temperature control, increased energy efficiency, and strict compliance with plant hygiene standards.
As part of this transition to more sustainable processes, the electrification of autoclaves, used for sterilizing food products, is a major innovation. By replacing steam sterilization systems with electric autoclaves equipped with power controllers, the food industry can achieve much more precise temperature and power control. These power controllers ensure effective sterilization by eliminating pathogenic micro-organisms, while guaranteeing food safety. What's more, the use of electric autoclaves not only reduces CO2 emissions, but also facilitates equipment maintenance and cleaning, reducing the risk of cross-contamination and improving hygiene conditions within production sites.
By integrating these solutions, food companies can not only reduce their carbon footprint and energy costs, but also improve product quality while complying with the most stringent sanitary standards. This innovative approach contributes to the sustainability of industrial activities, while ensuring the sector's competitiveness.
Faced with these challenges, Fuji Electric offers an innovative solution to optimize the use of professional electric ovens in the food industry. Fuji Electric's SCR power controllers, designed for single-phase and resistive loads, enable efficient and precise management of electric heating systems by incorporating advanced techniques such as phase angle switching and burst firing. These methods allow for fine-tuned control of load power and load voltage, ensuring perfect temperature control throughout the cooking and sterilization processes.
The electrification of industrial processes offers several decisive advantages for food companies. Firstly, it eliminates the CO2 emissions associated with the use of gas, thus reducing the company's carbon footprint. By replacing gas-fired systems with electric heaters, precisely controlled by Fuji Electric power controllers using zero cross and zero voltage switching techniques, companies can achieve significant energy savings while reducing air-conditioning costs, thanks to lower heat radiation in the workspace.
The temperature control offered by SCR power controllers ensures perfect uniformity in food cooking, avoiding temperature fluctuations that could compromise product quality. These controllers manage half cycle bursts to adjust power delivery precisely based on the input signal, maintaining consistent load power and ensuring the integrity of the process. This precision is essential to guarantee high-quality products that meet consumer requirements. In addition, electrification facilitates compliance with the most stringent hygiene standards by making equipment easier to clean and maintain, reducing the risk of cross-contamination and improving food safety.
By adopting the power control and temperature control solutions offered by Fuji Electric, food companies can not only achieve their environmental sustainability objectives but also improve their operational efficiency and product quality while reducing their energy costs. This transition to electrified industrial processes, including the use of phase angle switching and burst firing techniques, represents a strategic investment for companies seeking to remain competitive in an increasingly demanding market in terms of sustainability and quality.
CO2 reduction
Reducing consumption
Improving conditions
Product quality
Download your application sheet and improve hygiene and food quality with power control!