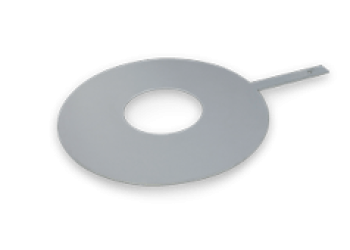
Choosing the right industrial pressure transmitter is not an easy task.
When choosing an industrial for your application, you need to ask yourself specific questions. pressure transmitter for your application, you need to ask yourself some specific questions.
This article will guide you through the selection process, helping you to understand the 9 key points to consider when choosing the right industrial pressure transmitter .
The type of measurement is the first question yourself to ask when selecting a pressure transmitter.
The most common application is pressure transmitter to measure pressure and vacuum. The sensor is subjected to pressure, from a pump or compressor for example.
The pressure transmitter hydrostatic level sensor measures the difference in height between two points.
The sensor can be used to measure the height of a liquid column.
Differential pressure flow measurement is based on the pressure difference in a flowing fluid. This is achieved through the use of specific primary elements.
Examples of depressurizers include orifice plates, venturi tubes or nozzles. Other options include V-ConeTM flowmeters, averaged Pitot tubes, integrated orifices, and microventuris.
Differential pressure flow meters are used to measure the flow of liquids and gases in a pipe.
Density measurement by differential pressure transmitter is an effective method for measuring the density of liquids.
The nature of the fluid, such as gas, liquid or vapour, is an important factor to take into account when measuring processes.
Knowing the critical properties of the fluid to be measured is the key to choosing the right sensor for your industrial process.
The type of pressure to be measured: Differential / Gauge / Absolute / Vacuum is an important consideration when choosing the right pressure transmitter.
Fluid temperature is another important factor to consider when selecting a pressure transmitter.
pressure transmitters are generally designed to operate with liquids, gases or steam within a given temperature range.
The minimum and maximum operating temperature limits of pressure transmitters are an important consideration when selecting a sensor for long-term use.
For high temperatures, you will need to use pressure transmitters at diaphragm seals to keep the sensor electronics away from the process measurement.
The pressure range is the final other element to consider when choosing a pressure transmitter.
The zero and span must be chosen to cover the applicable range without going beyond the upper or lower limit over which you need accurate measurements.
The corrosiveness of the fluid: contaminated, chemically aggressive.
It is important to take into account the corrosiveness of the liquids and gases for which you select a pressure transmitter.
Sensitive materials can be corroded by certain fluids under certain conditions.
This corrosiveness determines the choice of material for parts in contact with the fluid.
This choice has a significant effect on the life of the sensor.
Check the compatibility of the fluid with the materials of construction of your pressure transmitter.
The type of process connection: flanged, threaded, screwed or hygienic is another factor to consider when choosing the right pressure transmitter.
Process connections are available in different types depending on the type of connection required for the application:
The application's environmental conditions: temperature and humidity, explosive atmosphere, dust, EMC, vibrations, safety integrity level ( SIL) are other important factors to consider when choosing a pressure transmitter.
You need to understand how the pressure transmitters will be used, and ensure that they can withstand all potential conditions in their application environment.
You need to know whether your application requires specific types of safety certification and choose a pressure transmitter SIL2 or ATEX, IECEx, etc.
Application-specific requirements :
Choosing the right pressure transmitter for your application can be difficult.
There are many factors to consider when selecting a pressure transmitter. In particular, if you need an industrial or food-grade option.
The other crucial point is to define the type of process connection required.
Finally, it is important to take into account the environmental conditions to which the transmitter will be subjected during its lifetime.
These nine questions should help you make certain decisions as you make this important investment in your business.
Let us know if you have any other specific needs that are not covered here, so that our experts can recommend solutions tailored to your unique situation!