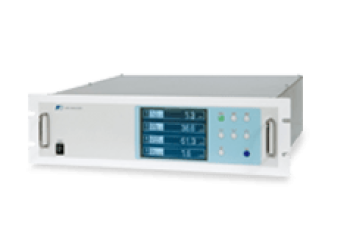
From biogas to biomethane highlights the process of converting biogas into biomethane. This ecological and sustainable process transforms organic waste into renewable green energy. It helps reduce greenhouse gas emissions and provides an additional clean energy resource.
Biogas and biomethane, derived from organic waste, are renewable alternatives to natural gas. Biogas is the first by-product of an anaerobic digestion unit. Consisting mainly of methane, it can be used to produce heat or electricity.
Once processed and purified of other compounds such as nitrogen dioxide (CO2), oxygen dioxide (O2), hydrogen sulfide (H2S)or water vapor (H2O), this same biogas becomes biomethane. This newly-formed fuel has the same properties as natural gas, with the added advantage of promoting the use of green energy while reducing greenhouse gas emission levels, thus protecting the environment through energy transition efforts worldwide.
Methanization is an astonishing process that uses the natural power of bacteria to break down and transform fermentable matter into biogas. This phenomenon can be found in wetlands, for example. The gas generated is rich in methane, a component also found in fossil fuels.
This ecological process also converts organic materials such as paper and cardboard, food scraps, plant by-products, animal waste, slurry, manure and sewage sludge into biogas.
An anaerobic waste digestion plant produces biogas from organic matter. This process takes place in tanks called reactors, fermenters or digesters, which operate at a temperature of 35°C. The latest versions can transform waste into renewable energy in a matter of days, with an estimated output of between 1 and 10 cubic meters per day for every cubic meter of waste treated.
From rural farms to huge industrial complexes, biogas production units come in all shapes and sizes. For example, the output of a small agricultural digester can be as little as 100 cubic meters, while the largest plants produce tens of megawatts.
Landfill sites, or ISDND (Installations de Stockage de Déchets Non Dangereux), are also a source of biogas. As organic matter decomposes, methane is produced.
The waste is compacted and deposited in pits known as bins. To ensure optimum results, the area can also be sealed. These spaces are filled with several meters of earth and crossed by a network of horizontal drains that collect the biogas produced, while the vertical ones allow it to reach the surface, so that regular fermentation can take place for around twenty-five years.
Preventing methane (CH4), a powerful greenhouse gas, from entering the atmosphere is essential in the fight against climate change. When it can't be recovered, flaring methane is a better alternative than releasing it. This releases carbon dioxide (CO2), a greenhouse gas which, according to the IPCC, has 28 times less impact than methane on our environment.
There are other, less widespread biogas production processes, based on more recent technologies, some of which are not yet fully mature.
One example is the generation of biomethane by methanation of carbon dioxide (CO2) in reaction with hydrogen (H2). Carbon dioxide and hydrogen are produced either by gasification of biomass from lignocellulosic resources, or by electrolysis of water (power-to-gas).
Finally, microalgae can be used as a primary or complementary input for the anaerobic digestion reaction. Cultivated in bioreactors, microalgae have the advantage of not consuming agricultural land, thus not competing with animal or human food production.
To produce biogas via a methanization process, fermentable source materials need to be harvested. These raw materials, also known as organic matter, are mainly our agricultural, municipal and food waste, but also our sewage sludge and plant matter in general.
The main outlets for biogas generated by the decomposition of organic matter are cogeneration, producing both heat and electricity, and biomethane, which, when injected into natural gas networks, completes the energy mix, supporting the ecological transition.
Biogas can be used to produce heat and electricity.
Biogas can be recovered in the form of heat only, by using it as fuel in a boiler. More often, however, biogas is used to produce both heat and electricity. Hence the term cogeneration.
The electricity generated by the cogeneration turbine is used for the biogas plant's own consumption, and the surplus - the majority of the power generated - is sold on.
The heat produced by biogas combustion is often used to heat the digester of the biogas plant, and to improve the plant's energy balance in general. But this heat is also used for :
The biogas is treated and purified for injection as biomethane into natural gas networks.
Several purification stages are required before biomethane can be injected into the network.
The main processes are :
Once cleaned and delivered to the injection station, the biomethane still has to be :
Biogas is made up of different gases, the proportions of which vary according to the raw materials and methods used.
The gases are essentially :
Methane is the main component of biogas. It is the fuel that will be used to create energy.
Biogas contains 50% to 75% CH4.
Carbon dioxide is a by-product of biogas, present in very large quantities but with no energy value. CO2 must be removed from biogas by various methods to generate usable biomethane. However, it can be retained if the biogas is valorized in the form of heat (boiler) and/or electricity (cogeneration).
Biogas contains 20% to 50%CO2.
Oxygen is present in biogas in relatively small but significant quantities. Biogas contains oxygen, which precipitates some of the hydrogen sulfide (H2S)in the digester.
In addition, because it is difficult to eliminate, a certain amount of oxygen is tolerated in the purified biogas (biomethane) before it is injected into the natural gas network.
Biogas contains less than 1% O2.
Raw biogas is a highly humid gas. Biogas needs to be dried, usually by cooling, before upgrading to protect equipment from corrosion.
Raw biogas is saturated with moisture.
Hydrogen sulfide is a very dangerous and harmful gas. On the one hand, it is a corrosive gas, which generates sulfuric acid in the presence of humidity and when burned in boilers or cogeneration plants.
On the other hand,H2Shas a strong, characteristic rotten-egg odor at low levels. This makes it easy to detect. But at higher concentrations, it affects the sense of smell in a more or less reversible way. It then becomes odorless, and all the more dangerous as it is no longer naturally detected by humans.
H2S present in biogas at 1500 ppm becomes lethal if inhaled for more than a minute.
H2S can be present in biogas in very large quantities. It is therefore essential to significantly reduce its content, whatever the biogas recovery method.
Biogas generally contains more than 100 ppmH2S, and this level can exceed 10,000 ppm when certain types of food industry waste are fermented.
Siloxanes in biogas are molecules derived from silicon. Biogas contains siloxanes when extracted from landfills (ISDND). These compounds are liable to damage installations, as they are vitrified (transformed into sand) once injected into cogeneration engines or biogas boilers, causing significant mechanical damage.
Biogas can contain up to 50 mg/m3 of siloxanes.
Biogas composition can be measured using a analyser multi-gas biogas analy zer to continuously and accurately quantify the exact content of the various gases present in the biogas or biomethane.
It is important to measure the composition of biogas with a analyser to ensure optimal and efficient biogas utilization. By quantifying the various biogas components, biogas chemical composition analysis enables biogas production to be controlled and optimized. Biogas analysis also ensures the safety of people and processes by checking whether potentially harmful gases are present in the mixture.