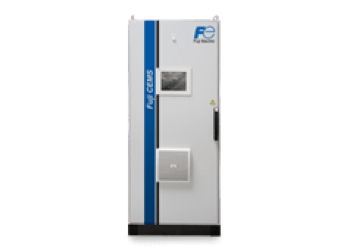
You have decided to purchase or develop an industrial analysis system for your process. This is a very important decision that will impact the efficiency and performance of your facilities..
When designing a gas analysis system for an industrial environment, there are 6 key points to consider.
In this blog post, we will detail them and explain how they can impact the overall success of your gas analysis system.
The choice of the detection technology(ies) to be used is essential when integrating a gas analyser into an industrial process. A wide variety of technologies are available, such as infrared (IR), thermal conductivity (TCD ),zirconium oxide (zirconia ) or paramagnetic detection for oxygen measurements. Each technology has its own benefits and drawbacks, so it's important to choose the appropriate one for your specific application.
The following elements need to be considered in the first selection phase:
THE COMPONENTS TO BE MEASURED
THE MEASUREMENT RANGES
THE INTERFERING COMPONENTS
This last factor is as crucial as the others, as cross-interference can disturb and compromise the measurements.
The second key point to consider is the choice between in situ or extractive gas analysis solutions.
In-situ gas analysers are installed directly in the process stream. They measure the gas concentration where they are, at a given time, without moving or altering them. Therefore, they are more efficient in terms of response time and, usually, more compact and less energy consuming, as they do not require gas preparation before analysis.
Extractive gas analysers take a sample of the process gas and analyse it outside the process, at a certain distance. The response time is longer, and a sample collection and processing system are required. As you can see, both methods have their benefits and drawbacks and the best choice depends a lot on the application.
The third key point to consider when building gas analysis solutions is the design of the sampling systems, also known as sampling systems, or sample processing or conditioning systems.
The sample gas must be representative of the process gas and must not contain any solid, liquid or gaseous contaminants that could damage the sensor. The sample gas must also be supplied to the analyser at a defined and constant flow rate and pressure. Different types of sampling systems may be required, depending on the application and the detection technology.
For instance, most IR analysers work at room temperature. The gases must therefore be dried beforehand to prevent them from condensing in the analyser's cell. However, an analyser equipped with a heated cell and measuring soluble compounds will receive a hot gas, filtered upstream.
The industrial analyser must be designed to operate and withstand the stresses of environmental conditions, including high temperatures, pressures and vibrations.
The main questions to be answered at this stage are:
INSIDE OR UNDER COVER
BOX OR CABINET
IP AND/OR ATEX
AVAILABLE UTILITIES
The industrial analyser's function is to determine the concentration of gas components in an industrial process. But its purpose is to inform the user, or even to control the process.
In the case of a Continuous Emission Measurement System (CEMS), the analysis system will be equipped with an automated Data Acquisition and Handling System (DAHS) software. This is a specific and complex interface, meeting standards that include EN14181 for CEMS and EN17255 for DAHS.
In the case of analysis systems used to control industrial processes, such as combustion control or heat treatment furnaces, the measurement data and some status information (ranges, alarms, etc.) are transmitted to the control system via analog signals (4-20mA, relay contacts, etc.) or by digital transmission (Modbus, Profibus, etc.).
Various devices such as a PC, industrial HMI touch screen, a smartphone or a tablet can be used as an interface, depending on the user's needs.
The sixth and final key point to consider is the durability and performance of a gas analysis solution. The gas analysis system must be able to withstand the harsh industrial use and maintain its accuracy over time.
To maintain the accuracy of a gas analyser over time, there are three basic design considerations:
A calibration device needs to be integrated into the sampling system for gas analyser. It is essential that gas analysis system is easy to calibrate, whether it is equipped with a manual device or an automatic calibration system. Furthermore, it must be adapted to the calibration frequencies required by both the detection technology and the operator's need to ensure the measurement accuracy of the gas analyser.
Materials such as seals, filters and other pump valves should be easily accessible to help them to carry out regular maintenance. Operators can be trained in these maintenance operations, or maintenance can be outsourced.
The materials used for all gas analysis systems, whether inside the gas analysers themselves or within the sampling systems, must be suitable for the sample gas conditions. They need to be resistant and inert, so that they can withstand moisture and corrosion. This not only prevents analytical equipment from being damaged, but also prevents the gases to be denatured before they are analysed.
Whether you are a project manager, or a maintenance or operations manager, these are the six key points to consider when designing a gas analysis system for an industrial environment. By considering all of these factors, you can select or develop an industrial analysis system that will meet your application needs and provide years of reliable service.
80% of problems encountered when usinganalysers gases are not due to theanalyser itself, but to the system in which it is integrated. Fuji Electric has been a manufacturer ofanalysers since... 1954 (!), as well as a designer, integrator and manufacturer of the complete analysis system adapted to the user's industrial process. Thanks to this dual expertise, Fuji Electric's gas analysis solutions are world-renowned as among the most reliable and efficient on the market.