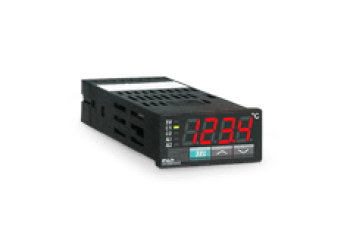
On/Off thermostat controller - PXR3
ref : PXR3V61From
229,00 € Request a quoteA Heat Treatment Controller is an essential tool in the control of temperature and time for the heat treatment process, crucial for achieving specific mechanical properties in materials. These devices, often programmable, allow for precise temperature control across multiple heating zones, increasing the process's efficiency and effectiveness in modifying material characteristics.
Looking to improve your heat treatment processes? Heat treatment controllers are the key to controlling and maintaining the temperatures required for high quality metal treatments. These advanced systems not only ensure material properties but also reduce energy consumption. In this article we look at how choosing the right heat temperature controller can transform your operations, with consistent quality, less downtime and longer equipment life.
During heat treatment, metals and metal alloys are heated and cooled in a controlled environment to modify their crystalline structure. Heat treatment involves heating the material to improve its mechanical properties and overall performance. The desired results of these heat treatments are hardness, temperature resistance, ductility and overall material reinforcement. Heat treatment of metals, particularly aluminum, is very important in many industries such as aeronautics and aerospace, automotive, semiconductor manufacturing, the arms industry, and the oil and gas industry.
Heat treatment temperature controllers maintain precise temperatures, ensuring consistent results throughout the heat treatment process.
Heat treatment controllers are at the heart of heat treatment systems, enabling :
These instruments from temperature control allow you to monitor and adjust parameters for optimum energy use and efficiency.
Choosing the right temperature controller for heat treatment depends on a number of factors: from the process to the result to the industry's requirements.
The choice of controller is determined by factors such as reliability, temperature range, type of control action required and power supply.
Every controller type is designed for a specific application so choosing the right one is key to getting the desired results.
There are different types of heat treatment controllers for different industrial processes.
These include the following types:
Each has its own capabilities and uses, making it suitable for different industries.
Choosing the right one means efficiency and safety, energy savings, reliable processes and consistent materials.
Just like a race car needs to be matched to the track it will run on, a heat treatment controller needs to be matched to the specific heat treating process. These processes require different furnace temperatures, so aligning the controller’s temperature range with the process is key to achieving and maintaining the required temperatures without sacrificing quality or safety.
Control accuracy also matters because it:
Additionally, the process’s complexity influences the kind of controller required.
precise temperature control
reduces dead time
improves process efficiency
product quality maintained
Advanced heat treatment controllers are more than just temperature controllers. They have many features that make them a vital part of the process. They offer precision temperature control, user friendly interfaces and compliance to safety and standards.
Austenitic stainless steel is an essential component of heat treatment processes, equipped with everything needed to guarantee efficiency, safety and rationalization of the process, in order to obtain the desired internal structure thanks to rapid metal cooling techniques.
One of the best features of advanced heat treatment controllers is precise temperature control. Precise temperature control is essential in heat treatment processes, as it ensures uniform heat treatment and consistent material properties.
This is done through advanced control systems and thermal loop systems that keeps the temperature within a certain range, so every part of the material goes through the same thermal cycle, including rapid cooling.
In today’s world, simple is key and heat treatment controllers are no exception. They have simple interfaces that make them easy to use and more functional. Automation in advanced heat treatment controllers enhances the heat treating process through real-time monitoring, data acquisition, and precise control over temperature, time, and atmosphere.
This decreases the dependence on manual intervention, thereby enhancing the entire process’s efficiency.
Safety is key in any process and heat treatment is no exception. Advanced heat treatment controllers must comply with safety standards that require regular maintenance of the furnace and control systems and use of personal protective equipment by operators when handling hot metal. Following these standards ensures operator safety and extends the life of the equipment.
Heat treatment controllers are used in many industries and here are a few:
These controllers ensure that the materials used in these industries meet the required specifications for strength and durability including reaching the critical temperatures like upper critical temperature during the heat treatment process.
Aerospace
Automotive
Metal industry
Manufacture
In the aerospace and automotive industries, heat treatment temperature controllers ensure precise temperature control during the various heat treatment processes to improve mechanical properties and overall part quality. They manage :
This improves the strength and durability of the metals used in body and engine parts.
In the metalworking and fabrication, heat treatment controllers control the heating and cooling of the material to obtain the desired properties:
By preventing deformation and irregularities, these temperature controllers are the key to the quality and reliability of the end product.
Optimisation is key in any process and heat treatment is no different.
Advanced controllers can help optimise heat treatment cycles for:
Heat treatment is fine-tuned for best results.
A well-managed heat treatment process consumes less energy. Advanced temperature controllers contribute to this by optimizing the heating cycle to consume less energy. They do this by precisely controlling the temperature to avoid overheating or prolonged heating cycles, thus reducing costs.
By controlling power in and not wasting energy through over heating these controllers save on energy and make the heat treatment process more sustainable and cost effective.
To get optimal energy savings in heat treatment processes you need to associate temperature controllers with SCR power controllers. This combination ensures the power supply to the heating system is precisely controlled and not wasted. By modulating the power input according to the real time requirements of the heat treatment process the power controllers work in tandem with temperature controllers to maintain the desired temperatures efficiently.
This synergy not only improves temperature control but also saves energy, so cost and sustainable. Implementing such a system will help industries to achieve their energy efficiency targets while maintaining high quality in their heat treating operations.
In the heat treatment industry, it is necessary to maintain precise, uniform temperatures throughout the process in order to correctly manage the material's melting point.
Advanced PID controllers ensure the specific temperature is maintained within a certain range so all parts of the material experience the same thermal cycle. This uniformity gives consistent material properties and high quality end products.
Reducing plant downtime and maintenance costs is a major goal in any industry. Advanced temperature controllers contribute to this by offering high reliability, redundancy, and lifecycle support. They are designed to ensure increased equipment availability and smooth operations.
An advanced heat treatment controller protects your furnace and its components. It helps to :
In the fast-paced world of manufacturing, automation is the name of the game. Automation in heat treating ensures repeatability and consistency, reduces reliance on manual intervention, and improves overall process efficiency.
Advanced heat treatment controllers are equipped with automation features that ensure the process runs smoothly and effectively, reducing the likelihood of human error and increasing overall process efficiency.
Multiloop temperature controllers with human-machine interface (HMI) are super user friendly in heat treatment processes. These controllers can control multiple temperature zones at the same time, more precise and efficient. The HMI gives you a visual of the process so you can monitor and adjust in real time. This simplifies complex operation, reduces errors and allows for adjustments on the fly so you have total control of the heat treatment process. With intuitive navigation and clear feedback the multiloop controllers and HMI will improve your user experience and operation.
In the world of manufacturing, heat treatment controllers help save energy, maintain quality and guarantee safety. These versatile devices are used in a wide range of industries, from aerospace and automotive to metalworking and manufacturing. They offer precise temperature control, user-friendly interfaces, process automation and meet safety and compliance standards. By choosing the right temperature controller, optimizing heat treatment cycles and following best practices for calibration and maintenance, you can get the most out of these advanced controllers and keep your heat treatment processes running smoothly.
Heat treatment is used to obtain a material's properties, strength, durability and wear resistance by applying heat and manipulating its microstructure.
Heat treatment involves heating the metal to a specific temperature without melting it, then cooling it in a controlled manner to obtain the desired mechanical properties. It can include annealing, tempering and quenching to achieve different results.
Heat treatment controllers enable the material to be heated or cooled consistently and uniformly to control the furnace temperature.
Get the most out of your heat treatment processes with Fuji Electric’s Heat Treatment Controller. With latest technology, our controllers offer highest temperature accuracy, easy programming and flexibility to manage complex heat treatment profiles.
Our Heat Treatment Controller is the key to big energy savings and top quality in your materials. By controlling your heat treatment processes precisely, you can reduce energy consumption and minimize material waste, for more efficient and cost effective operation. Whether you want to harden metals or achieve specific material properties, our solution is designed to meet your needs with precision and reliability.
Don't settle for quality or efficiency. Contact Fuji Electric today to see how our heat treatment controller can change your heat treatment processes. With our technology, save energy while improving the quality of the materials you produce.