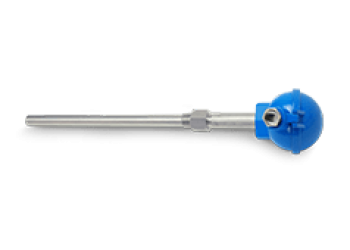
Industrial metrology is of paramount importance in the world of manufacturing and production. It focuses on the application of precise measurements to ensure product quality, efficiency and conformity. Measurements carried out by specialized instruments help establish the reliability of production processes and ensure compliance with international standards.
For companies seeking to improve quality and performance, metrology services are essential. They underline the importance of accurate measurements. The application of industrial metrology is essential to meet demanding customer requirements and quality standards.
The fundamental principles of industrial metrology involve understanding the units of measurement, knowing the permitted margins of error, and mastering calibration methods. These principles are applied by means of industrial measuring instruments and equipment, which must be regularly calibrated. This rigorous approach guarantees the precision of our equipment and the traceability of our measurements.
The applications of metrology in industry are diverse, ranging from product quality inspection to supply chain management. Quality assurance relies on metrology to verify that finished products meet specified criteria.
Industrial metrology refers to the science of measurement and its application in the industrial field. It is based on three fundamental pillars: measurement accuracy, precision and repeatability.
Precision
Accuracy
Repeatability
Measuring instruments must be calibrated regularly to maintain their validity and reliability. Calibration ensures that measuring instruments comply with reference standards.
Term | Definition |
---|---|
Calibration | Comparison between value and reference standard. |
Tolerance | Margin of error accepted for a measurement. |
The units of measurement used must be uniform and standardized at international level. The International System of Units (SI) is the reference for this.
Quality standards such as ISO 9001 are also used to guarantee traceability, quality management and continuous improvement of industrial measurement processes.
By mastering these fundamental principles, industrial metrology is of major importance to quality assurance and competitiveness in the global marketplace. The importance of 'meaning' in industrial metrology lies in the need to ensure that measurements make sense and can be compared consistently across different contexts, maintaining an international and national standard reference.
Industrial metrology relies heavily on a wide range of accurate and reliable instruments to ensure the quality and conformity of manufacturing processes. These tools are essential for obtaining accurate, repeatable measurements.
This approach guarantees traceability to national and international standards, which is a requirement of certification, quality and accreditation standards.
The use of a suitable tool is fundamental to maintaining better control over the results of metrological traceability, underlining the importance of an unbroken chain of comparisons as a necessary component of effective traceability.
Sensors are fundamental to data collection, converting physical parameters into measurable signals. Transmitters are devices that convert one form of energy into another for measurement.
Temperature measuring instruments:
Pressure measurement instruments:
These instruments measure the physical dimensions of an object. They range from simple calipers, gauges and micrometers to more complex systems such as coordinate measuring machines (CMMs).
Advances in metrology technology, in particular instantaneous measurement systems, play a key role in ensuring the accuracy of measurements and the reliability of production processes. These systems enable fast, accurate measurements to be taken automatically. They also facilitate profiling, geometric dimensioning and tolerance. They also support CAD file import and offer automated programming.
analysers quality control systems, including spectrometers, hardness testers, defect detectors and machine vision systems, are used to inspect and guarantee product conformity to standards. Spectrometers analyze the chemical composition of materials, while durometers measure their hardness. Defect detectors spot anomalies in materials or assemblies, and machine vision systems offer automated visual inspections for quality verification. All these materials testing equipment are vital in assessing compliance with datasheet requirements through a variety of tests.
Calibration is essential in industrial metrology. It comprises a complete set of operations designed to ensure the accuracy of measuring instruments. Quality assurance, meanwhile, is vital to guaranteeing this accuracy and standardizing processes.
Calibration procedures ensure that measuring instruments operate correctly and deliver reliable results. A plan is drawn up detailing the frequency of calibration and the methods to be used.
Intervention | Frequency |
Preventive | According to operational needs |
Corrective | Once a significant discrepancy has been identified |
Calibration methods : Choice of standards and technical means.
For quality management in metrology, it is imperative to follow a strict quality management system in line with international standards.
Metrology, with its extensive application across a wide range of fields and disciplines, is proving decisive in guaranteeing precision, quality and uniformity in various industrial sectors. It is of major importance in validating the characteristics of products and manufacturing processes, underlining its interdisciplinary nature and its application across diverse scientific and industrial fields.
In mechanical engineering, metrology is used to accurately measure the dimensions of mechanical components.
Instruments such as micrometers, verniers and coordinate measuring machines (CMMs ) are used to check that manufactured parts comply with the required tolerances.
Metrology is essential in the electronics industry to ensure that electronic components and printed circuit boards meet strict datasheet standards.
Tools such as oscilloscopes, multimeters and analysers spectrum analy zers are used to rigorously characterize electronic performance.
Industrial process control involves the use of metrology to monitor and regulate manufacturing operations in real time.
Sensors, actuators and machine vision systems are deployed to maintain constant production quality.
Industrial metrology is essential for guaranteeing measurement accuracy in production and compliance with standards. This section seeks to deepen their knowledge and answer frequently asked questions to shed light on its role and importance specifically in an industrial context.
Industrial metrology focuses on the application and assurance of accurate measurements in manufacturing and production processes. Legal metrology deals with measurements required by regulations and laws for commercial transactions and consumer protection. Scientific metrology refers to high-precision measurements and measurement standards used in science and research.
In the industrial sector, metrology is used to calibrate and maintain the accuracy of measuring equipment, to ensure the quality of parts produced and to validate the conformity of end products to datasheet. It is also critical for optimizing production processes and ensuring effective quality control.
This approach detects manufacturing deviations and adjusts processes to ensure product consistency and quality. This discipline helps to reduce waste and scrap, improve manufacturing tolerances and support an effective quality management system.
The choice of measuring equipment is based on its accuracy, reliability, resistance to working conditions and ability to be calibrated. Cost, ease of use and suitability for specific applications are also important considerations.
Jobs in industrial metrology include metrology technicians, quality engineers and calibration specialists. Skills required include an understanding of measurement principles, the ability to work with precision instruments and knowledge of industrial quality standards and measurement units, and contacts in the scientific community.
Accurate and efficient industrial metrology enables companies to improve production quality and reduce costs, thereby strengthening their market position, evolution and growth. It guarantees innovation, product development and access to international markets.