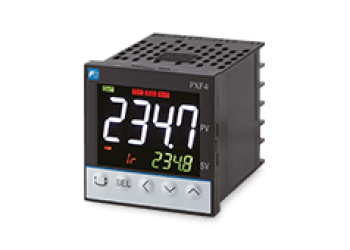
PID temperature controller - PXF4 series
ref : PXF4From
241,00 € Request a quotePID Control for Dummies is designed for those looking for a better understanding of PID control without getting bogged down in complex technical concepts.
Whether you're a technician or a student in the field of instrumentation, this article is intended as a resource to guide you towards knowledge of the pid controller.
You'll learn about the origins of PID control, how it works, the importance of PID control in different industries, and tips for optimizing your process.
It's difficult to discuss PID control without touching on its history. At the beginning of the 20th century, Nicolas Minorsky observed that ships were unable to maintain a constant course despite the continuous efforts of the piloting staff.
Mr. Minorsky then developed a solution to the need: the use of an automatic controller, which, by exploiting deviations between the desired direction and the actual course, could adjust the rudder to ensure smoother navigation.
This was the basis for the birth of PID control, and its effect on industrial process control has been major.
To easily understand how a PID controller works, let's consider a simple and common example of a pottery kiln loop temperature control with a temperature controller PID PXF.
The temperature inside the oven must be maintained at a constant setpoint , say 800°C.
Instead of a simple all-or-nothing control system (the oven is either on or off), the temperature controller PID will maintain this temperature constant to avoid any deviation that could deteriorate the quality of the product inside the oven.
Here's how it works.
The start of the control process involves a thermocouple temperature sensor which monitors the temperature inside the furnace.
This measure of temperature is compared with the temperature setpoint (800°C in this example).
Thedifference between these two values, called the error, is sent to the PID controller, which formulates a correction action on the output to mitigate this error. The output of the temperature controller PID then controls the SCR power controller, providing the optimum power to the furnace heating element to correct the deviation.
This correction is the product of three functions or quantities: Proportional (P), Integral (I ) and Derivative (D ) together form the acronym PID (Proportional Integral Derivative).
The proportional band action is equivalent to multiplying the error by a proportional coefficient (Kp). This action adjusts the controller output to be proportional to the error. So, if the error or disturbance is large, the correction will be equally large, and vice versa.
Integral action aims to eliminate persistent error by accumulating past errors and integrating them over time. This action brings the system progressively closer to the setpoint by adjusting the output according to the integrated error. The integral coefficient (Ki) determines the influence of this component.
The derived action concerns the rate of change of the error. This predictive action enables the system to react to future events based on observed trends. The derived coefficient (Kd) adjusts the influence of this action for better control.
Setting up a Proportional Integral Derivative controller may seem daunting, but it's essential to ensure that your process runs smoothly. Each of the tuning parameters, P, I and D, impacts the way the controller reacts to process value variations.
The right settings can significantly improve the stability and performance of your system.
On the other hand, incorrect settings can lead to oscillations, over-excitations and under-reactions, impairing the quality of process control.
The Ziegler-Nichols method is a well-known approach to setting the parameters of a PID controller.
This method consists of making the system or process oscillate by adjusting the proportional gain (Kp) until it reaches the stability limit.
The oscillation period and critical gain are then used to determine the optimum proportional (Kp), integral (Ki) and derivative (Kd) coefficients.
While this method is convenient for initial setting of PID parameters, it is important to note that optimization of the control system may require further adjustments. These adjustments will depend on the desired response and specific process constraints.
If your system has inherent instability, or other prevailing problems such as delays, disturbances, external pressures, etc., then a P, I, D controller can only temper them, not eliminate them completely. It is sometimes useful to redesign the process, or to opt for Fuzzy Logic technology from temperature control .
In a closed loop, information on the current state of the process is constantly fed back to the PID controller.
It uses this information to correct its output, thus keeping the process as close as possible to the setpoint.
This mechanism considerably improves the precision of process variable management, enabling tighter control and greater stability.
In addition, closed-loop systems effectively counteract external disturbances, minimizing unwanted fluctuations.
All-or-nothing refers to a control mode in which the system is either 100% on or completely off. There are no intermediate operating levels.
All in all, on/off control can be adapted for simple, less demanding applications.
However, for precise, efficient temperature control, particularly in industrial environments or for critical processes, PID controllers: the solution for improving your industrial processes offer significant advantages in terms of stability, energy efficiency and equipment protection.
The proportional band is the range of values within which the controller switches from its off state to its full power state (and vice versa) in a proportional control. It is the part of PID control that reacts according to the deviation between the desired value and the actual value. The greater the deviation, the greater the correction.
The integral band is the part of the PID control that accumulates over time. If the deviation persists, however small, this correction will continue to increase until the deviation is corrected.
Thederivative action in PID control is the part that reacts to the speed of change of the deviation. It tries to predict the future of this deviation and to make a preventive correction to minimize too rapid variations.
The advantages of PID controllers in industry are numerous. In the pharmaceutical industry, regulating temperature is of prime importance, as well as in the food industry (e.g.: guaranteeing production quality in bakery ovens, or regulating the temperature of pizza ovens), in the automotive industry (e.g.: reducing energy consumption in paint booths) in laboratories (e.g.: guaranteeing material quality when testing automotive materials), in special machines such as packaging machines or improving quality in the plastics industry with temperature controllers, in particular for:
And many other applications with temperature control systems.