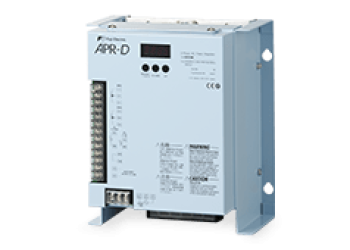
SCR power controllers, or silicon-controlled rectifiers, are crucial for precise temperature control in a wide range of industrial applications, including heating, melting, drying, and shaping.
These versatile devices boats impressive efficiency for up to 99.8%, outperforming alternatives such as IGBT-based controllers. The main advantages of SCR power controllers include their wear-free switching capabilities, adaptability and compact design.
They excel at managing electrical flow to heaters in industrial furnaces, ovens and thermal processing equipment, resulting in enhanced reliability, cost-effectiveness and energy efficiency.
By understanding these key aspects, capabilities, and performance characteristics, businesses can unlock the full potential of SCR Power Controllers and optimize their industrial processes.
In the world of manufacturing,temperature control is essential for various processes such as heating materials, melting, drying, and shaping. Silicon-controlled rectifiers (SCRs), commonly known as SCR power controllers, serve a crucial function in maintaining precise temperatures by managing the electrical flow from the grid to heaters within industrial furnaces, ovens, and other thermal processing equipment.
When compared to alternatives like IGBT-based controllers, SCR power controllers demonstrate superior efficiency, reaching up to 99.8%. Additionally, thyristor devices' wear-free switching capabilities make SCR power controllers an ideal replacement for contactors or relays, significantly enhancing reliability and product lifespan.
Closed-loop system where the SCR power controller skillfully manages the power flow from the mains to a furnace, oven, or heater. This system exemplifies the adaptability and precision of SCR power controllers in industrial heating applications.
A temperature sensor or transmitter positioned within the furnace provides direct feedback to either a Fuji Electric Micrex programmable controller or an external temperature controller. Consequently, the Fuji Electric Micrex programmable controller or Fuji Electric PXF temperature controller sends an analogue or digital set point to the SCR power controller. This set point is determined based on chamber temperature, control, and PID settings..
The SCR power controller then uses this set point to regulate the electricity flow to the heater, ensuring a precise and stable temperature inside the furnace. A high-quality SCR power controller can modulate current, voltage, or power output based on process requirements and conditions, showcasing its versatile functionality in various industrial heating applications.
SCR power controllers are integral to a wide range of industrial manufacturing processes utilizing electrical heating. Industries that commonly rely on these controllers include:
SCR power controllers contribute to superior quality and cost-effectiveness through their precision, adaptability, compact design, and energy efficiency.
Temperature control accuracy is often compromised by fluctuations in mains voltage and heating-element resistance. Mains voltage can vary up to ±10% or more, leading to temperature inconsistencies. SCR power controllers tackle this issue by using RMS voltage regulation to compensate for mains voltage fluctuations. In voltage regulation mode, the SCR's firing angle (phase angle) or duty cycle (zero cross) is adjusted to maintain a stable voltage output relative to the set point.
Heating-element resistance variations stem from ageing, temperature coefficients, and other material properties. SCR power controllers address these variations by regulating the RMS output current. When both true RMS current and true RMS voltage regulation are applied, the power regulation mode is achieved. Power regulation allows the SCR power controller to regulate true power independently of mains voltage or heater resistance variations, ensuring the highest temperature regulation accuracy and process repeatability.
SCR power controllers offering a broad range of operation modes and communication options ensure optimal performance and seamless integration into any process.
For systems with Fuji Electric controllers communicating digital set points to the SCR power controller, typical field bus protocols include:
Connected SCR power controllers facilitate system streamlining with fewer components and enhanced data collection. Reduced cable and communication card counts lower costs and minimize potential failure points, while shorter cable lengths boost efficiency and decrease power consumption.
In the confined spaces of industrial manufacturing systems, SCR power controllers must be compact without sacrificing functionality. Cutting-edge SCR power controllers offer a small footprint that meets these requirements.
Advanced SCR power controllers allow users to easily monitor and configure their SCR power controller through compatible Android and Apple apps. This user-friendly app offers a range of features to improve the efficiency and convenience of managing your power control unit.
Rising energy costs in both public and industrial sectors have increased the demand for highly efficient production technologies to minimize capital and operational expenses, especially in energy-intensive applications. With an impressive 99.8% efficiency, SCR power controllers hold a distinct advantage over alternative devices like IGBT-based power supplies and converters.
Additionally, contemporary SCR power controllers provide multiple firing modes, allowing users to choose the most suitable control method for their application. Firing modes can be selected based on technical necessities such as minimizing THD or maximizing power resolution. Advanced control techniques like mains load optimization can reduce peak load demand for multiple SCR units, resulting in lower energy rates.
SCR power controllers offer various firing methods to optimize performance in industrial applications. These methods help regulate power demand and minimize electrical interference while ensuring efficient operation.
Phase-angle (VAR) mode is a popular choice for heating applications due to its precise power resolution.
Phase Angle (PA) firing is a method that enables precise control of power to the load by allowing the thyristor to conduct only for a portion of the AC supply cycle. The required power determines the conduction angle, which advances progressively until virtually the entire cycle is conducted for 100% power.
Load power can be adjusted from 0 to 100% based on the analog input signal, typically determined by a temperature controller or potentiometer. PA is commonly employed with inductive loads, offering improved efficiency and adaptability in various industrial applications.
However, this mode can generate excessive harmonics and low power factor, potentially interfering with other equipment's operation.
Digital SCR power controllers with advanced features offer several alternative firing modes to overcome these limitations:
This full-wave switching operation mode generates minimal harmonics and is widely used in various heating applications.
For multi-zone applications where the overall power is high, Fire Synchronization is necessary to avoid power surges and improve the power factor when operating in zero-cross mode.
This is a super Fast Firing used with short infrared elements to avoid flickering and harmonic generated by Phase Angle Firing
SC is the fastest zero-crossing switching method. With an analog input, the unit adjusts the number of ON and OFF cycles based on the input signal. The microprocessor calculates and memorizes the ratio to deliver precise power control to the load.
Delayed Triggering (DT) is a method specifically designed for switching the primary coil of transformers when connected to standard resistive loads (not cold resistance) on the secondary side. DT effectively prevents the inrush current that can occur when zero voltage (ON-OFF) is used to switch the primary.
The thyristor unit switches OFF when the load voltage is negative and switches ON only when positive, with a preset delay for the initial half cycle. This approach ensures enhanced performance, efficiency, and reliability in various industrial applications involving transformers.
BF is a digital firing method performed within the thyristor unit at zero volts, resulting in no EMC interference. With an analog input, the number of complete cycles required for 50% of power demand must be specified. This value ranges from 1 to 255 complete cycles, determining the speed of firing. When set to 1, the firing mode becomes Single Cycle (SC).
S+BF is an additional feature that combines Soft Start with Burst Firing. Starting in Phase Angle mode, the unit ramps from zero to full voltage at a preset time before transitioning to full conduction. This method is ideal for switching small inductive loads, as it prevents current surges and minimizes electrical interference.
To counter the effects of supply voltage fluctuations, the voltage supplied to the load is measured and compared with the controller's power demand. The error signal is used to maintain the requested power level automatically. There are three control modes available:
Optionally, it is possible to switch control modes from voltage to power through a simple digital command.
For heating resistors like MoSi2 Element (Kanthal Super Elements TM) whose resistance when cold is very low and which increases sharply with temperature, it is essential to limit the current to the load by reducing the voltage using phase angle ignition and current limit to prevent the oversizing of the SCR power controller in terms of current.
As the resistance value reaches a predetermined threshold, there are two selectable working methods available :
By exploring these advanced firing modes, users can optimize their heating processes while minimizing the drawbacks associated with traditional phase-angle mode. The right choice of firing mode will not only enhance energy efficiency and process control but also reduce interference with other equipment, ensuring smooth and efficient industrial operations.
SCR power controllers offer considerable cost reductions through their energy efficiency and extensive connectivity options.
SCR power controllers unlock the potential for substantial cost savings by offering a comprehensive range of connectivity options. One notable example is Ethernet/IP connectivity, which minimizes the need for numerous cables and communication cards, resulting in considerable savings:
By leveraging the energy efficiency and versatile connectivity options of SCR power controllers, businesses can optimize their industrial heating processes while minimizing costs. This approach not only enhances immediate performance but also ensures future scalability and adaptability in an ever-evolving technological landscape.
Eliminate redundant analog equipment
Reduce space and save time
Enhanced digital control
Scalable performance and functionality
Incorporating communication bus modules in your industrial setup can significantly streamline operations and reduce costs. By minimizing the need for multiple bus cards, these modules offer the following advantages:
By integrating communication bus modules into your industrial processes, you can improve efficiency, reduce costs and ensure seamless scalability.
SCR power controller technology delivers significant cost benefits through its inherent energy efficiency. Boasting an impressive 99.8% efficiency, SCR power controllers conserve energy by minimizing power losses (heat load) compared to switch-mode power supplies. This efficiency offers several advantages:
In conclusion, digital SCR power controllers offer a multitude of opportunities for intelligently managing electrical energy in industrial furnaces, ovens and other thermal processes. Compared to their analog counterparts, digital SCRs deliver superior power regulation, diagnostics, adaptability and bus connectivity. These capabilities have demonstrated substantial improvements in thermal processes, including enhanced quality, increased throughput and reduced energy expenses. The compact design and user-friendly nature of digital SCRs are additional advantages.
By making well-informed decisions about this critical component of your thermal process, you can gain a competitive edge in addressing rising energy costs, meeting demands for higher throughput and ensuring improved quality. Embrace the future of industrial heating processes by harnessing the power of digital SCR power controllers with cutting-edge technology that drives efficiency, sustainability and growth.
Discover the game-changing benefits of SCR power controllers, designed to optimize energy efficiency, reduce costs and improve industrial operations. These advanced devices offer precise power control, improved power factor performance and reliable protection for your sensitive equipment.
Don't let outdated technology hold you back! With Fuji Electric's SCR power controllers, you can overcome the challenges of energy management and boost your business growth. Experience unparalleled control, robust performance and long-term savings, tailored to your specific needs.