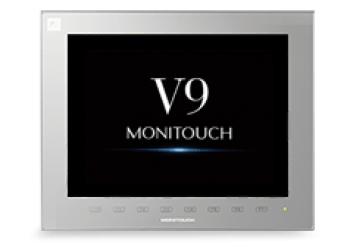
HMI - Monitouch V9150 - 15 inches
ref : V9150From
4335,00 € Request a quoteIncineration plants and energy recovery units (UVE) are combustion facilities whose gas emissions are limited by strict regulations. To optimize energy performance, protect the environment, measure pollutants in flue gases and guarantee the safety of the technical process, the installation ofmeasuring instruments (pressure transmittertemperature probes, flow meters, level probes, energy meters) andgas analysis equipment is essential.
Fuji Electric measuring instruments support professionals in the waste-to-energy industry during each phase of their manufacturing process in order to:
Compliance with current standards
Air emission controls
Plant safety
Production waste management
Energy recovery from non-hazardous waste is a crucial process for waste management and the production of renewable energy. Waste incineration plants (UIOM) play an essential role in this process, recovering the energy produced when waste is burned.
These incineration plants not only reduce the volume of waste, they also transform it into a valuable energy resource. By burning waste, MWIPs generate heat and electricity, thus contributing to waste-to-energy conversion. In this section, we explore the operating principles of MWIPs and the various stages involved in waste-to-energy conversion.
The waste treated in MWIPs is mainly household waste, but also industrial and domestic waste . This waste is characterized by its Lower Calorific Value (LCV), which defines the energy produced during combustion. Waste with a high ICP is more suitable for energy recovery, as it produces more heat when burned. By treating these different types of waste, industrial incinerators help to reduce waste volumes while recovering valuable energy.
The function of the central control room is to control and monitor the waste incineration plants. One of its key tasks is to optimize combustion based on the output values of each unit.
The combustion control system adjusts the amount of fuel and air required. This ensures complete combustion and avoids the production of toxic gases such as dioxin. In addition, it regulates the speed of the moving grates so that waste moves forward and burns slowly.
The heat produced byincineration can be recovered and integrated into a heating network to supply district heating systems, transforming waste into a renewable energy source and improving the energy efficiency of facilities.
On the other hand, the automatic combustion control system, also known as DCS (Distributed Control System), controls all utilities. These include wastewater treatment plants, water supply facilities, substation equipment and waste loading facilities.
An industrial incinerator is a furnace in which waste is burned.
Waste transported to a hearth incinerator is burned until it is transformed into ash.
A fixed hearth incinerator comprises a drying hearth, a combustion hearth and an afterburner.
A cooling tower is the equipment that lowers the temperature of the flue gases to 150 °C by spraying water into the flue gases. The temperature of the flue gases during the waste incineration process is above 800 °C. It is then cooled below 250 °C as the gas passes through boilers and pipes.
The reason for lowering the temperature of the flue gases is to prevent the resynthesis of dioxin in this temperature zone. Dioxins are generated from frying ash and Cl.
A baghouse filter, also called a baghouse dust collector, contains many fabric filters. The number of filters varies from 10 to several hundred depending on the scale of the installations. A bag filter is capable of filtering particles of about 0.2 µm. When the filtered gas contains dust, slaked lime is added at the same time. Then the slaked lime absorbs chlorine and harmful ash. Passing through all the filters, the gas is cleaned before being emitted through the chimney. As the surface of the filters becomes dusty, it is necessary to remove the dust regularly.
The denitrification system is essential for reducing NOx emissions into the atmosphere. It converts nitrogen oxides into nitrogen and water, thereby helping to protect the environment.
Nitrogen oxides (NOx) contained in combustion gases produce a harmful substance called photochemical oxidant when they come into contact with ultraviolet rays. If the photochemical oxidant remains in the atmosphere, it is transformed into smog, known as photochemical smog.
The NOx released into the air binds with H2O or O2 to form HN03. This causes acid rain, which pollutes rivers and soil.
In a denitrification unit, NH3 is added to the flue gas so that NOx is reduced to N and H2O. The catalytic unit features a honeycomb catalyst that helps NOx and NH3 bind together.
To save energy and reduce costs, it's important to measure NH3 concentration and control the amount of NH3 used.
Waste-to-energy consists of recovering and valorizing the energy produced when waste is burned. This energy can be used in the form of heat or electricity. MWIPs and other waste-to-energy plants are equipped with industrial boilers to recover heat and turbines to produce electricity. The heat can also be transmitted to a district heating network (CAD) to supply buildings in the region. This process maximizes the use of available resources and reduces dependence on fossil fuels, while helping to protect the environment.
Find out how gas analysers help reduce pollutants and promote the development of clean energies for a sustainable environment.
June 09, 2024
Reduce your TGAP by recovering energy from waste treatment plants. Find out how to quantify this energy and benefit from government rebates.
January 02, 2023