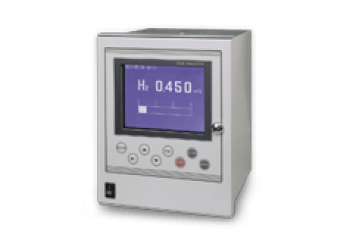
Hydrogen plays an important role in the production of renewable energy. Gas measurement and analysis instruments (analyser hydrogen gas, pressure transmitter hydrogen, hydrogen flowmeter, temperature probe) help to improve the manufacturing process, reduce costs and extend the life of hydrogen production processes, hydrogen storage and transport, stations and fuel cells.
Fuji Electric's measuring instruments are designed to respond effectively to the crucial challenges of the hydrogen industry, at every stage of its production.
Here's how we address these challenges:
At Fuji Electric, we equip you to meet today's challenges and prepare for a greener, more sustainable future.
Sustainable production
Compliance with current standards
Process safety
Lower production costs
Hydrogen, often dubbed the energy of the future, promises to revolutionize our approach to the production and use of clean energy. It stands out for its cleanliness, energy efficiency and storage capacity. It is also appreciated for its versatility and the technical challenges it presents.
Hydrogen, often described as the energy carrier of the future, comes in a range of colors depending on its production method and environmental impact. Each type is classified by a color that provides information on the advantages and disadvantages associated with its production process.
Black and brown hydrogen are derived from the gasification of coal and lignite respectively. These methods emit high levels of CO2 and other greenhouse gases, posing a major challenge for the ecological transition.
Green hydrogen is produced by electrolysis of water using electricity from renewable sources such as solar and wind power. It represents the most sustainable and cleanest option. The process of producing green hydrogen remains expensive due to the cost of renewable energies and electrolysis technology.
Pink hydrogen (sometimes called red or purple), similar to green hydrogen, is generated by electrolysis, but specifically fromnuclear energy. Although it has a low carbon footprint, it raises concerns about nuclear safety and the treatment of radioactive waste.
Blue hydrogen is produced from hydrocarbons, such as natural gas, with a carbon capture and storage (CCS) process to minimize emissions. It is cleaner than black or brown hydrogen, but still relies on fossil fuels and requires an efficient CCS infrastructure.
White hydrogen refers to geothermal hydrogen, extracted directly from natural sources, but its availability is limited to geothermally active regions.
Turquoise hydrogen is obtained by pyrolysis of methane, a cleaner method since it produces solid carbon instead of CO2. Nevertheless, this technology is still at an early stage of development.
Yellow hydrogen is sometimes used to refer to hydrogen produced by electrolysis using electricity from a mix of renewable and fossil sources, which places it somewhere between green and grey in terms of carbon footprint.
Grey hydrogen is manufactured from natural gas by steam reforming without capturing the CO2 emitted, making it a significant source of greenhouse gas emissions.
Since February 17, 2021, thanks to an ordinance anchored in the Energy-Climate Law, the hydrogen sector in France has enjoyed affirmed legal recognition within the Energy Code. This innovative legal framework proposes a renewed approach to classifying hydrogen, abandoning the old colored categories in favor of a classification based on hydrogen's ecological attributes.
As a result, the evaluation of hydrogen now focuses on its environmental impact, highlighting the nature of its original energy source and the volume of CO2 emissions generated by its production.
Renewable hydrogen generally includes green hydrogen, and sometimes pink, provided that nuclear energy is considered renewable.
Low-carbon or decarbonated hydrogen encompasses types of hydrogen whose production generates less CO2 than traditional methods, notably blue hydrogen and sometimes turquoise hydrogen. The Gas and Hydrogen Market Directive sets a threshold of 3.38 kgCO2eq/kgH2 for the definition of low-carbon hydrogen.
Carbonated hydrogen is a term used to describe forms of hydrogen produced with a large carbon footprint, such as black or brown hydrogen.
Each type of hydrogen offers a compromise between cost, accessibility and environmental impact, reflecting the complexity of the transition to a hydrogen economy and the need for continuous innovation to achieve sustainable, economically viable production.
Specifications :
To produce hydrogen by steam reforming, the hydrocarbon and steam are heated in the presence of a catalyst. H2 or a mixture of CO and H2 is obtained. Light hydrocarbons such as methane, natural gas, LPG and naphtha are used as raw materials. These materials must be desulfurized before use.
This method of steam reforming methane involves a series of chemical reactions in which a hydrocarbon reacts with steam to produce hydrogen and carbon dioxide.
In this context, each measuring instrument plays a specific role in ensuring efficient and safe production.
Pressure measurement is essential to control the pressure inside reactors, ensuring optimum conditions for chemical reactions and overall process safety. Temperature measurement is essential to monitor and regulate the temperature inside the reactor, as reforming requires high temperatures to be efficient, directly influencing the performance and longevity of the equipment.
Flow measurement plays an indispensable role in regulating the supply of steam and hydrocarbons to the reactor, ensuring that the necessary chemical reactions are maintained and that hydrogen is continuously produced.Gas analysis is also used to examine the composition of the gases produced, verifying the effective conversion of hydrocarbons into hydrogen and detecting impurities or by-products, such as carbon monoxide, which could compromise gas quality.
Although less frequent, level measurement is used to control the volumes of liquids, such as water and hydrocarbons, before they are processed, ensuring precise management of the raw materials required for the process.
Specifications :
The hydrogen electrolyzer is state-of-the-art technology, harnessing electrical energy to separate water into hydrogen and oxygen. Hydrogen electrolyzer manufacturers offer a range of different technologies: alkaline water electrolysis (AWE), proton exchange membrane electrolysis (PEM), solid oxide electrolysis (SOEC), anion exchange membrane hydrogen electrolyzer (AEM).
Ensuring maximum efficiency and safety of this green hydrogen production process by water electrolysis relies heavily on precision measuring instruments and control systems.
The pressure transmitters are essential for keeping the internal pressure of the hydrogen electrolyzer within safe operational limits, thus preventing any dangerous overpressure scenario. Equally essential is the role of temperature measurement technology, which provides real-time data to monitor the thermal state of the hydrogen electrolyzer, a variable that significantly influences the efficiency and longevity of the process.
Hydrogen flowmeters provide accurate quantification of hydrogen electrolyzer performance, enabling operators to monitor production rates and make adjustments to optimize performance.
Finally,hydrogen composition analysis plays an essential role in guaranteeing the purity of the hydrogen produced. This analytical process ensures that the hydrogen produced meets the high quality standards required for various applications, while identifying any undesirable impurities or by-products that may emerge during electrolysis.
Specifications :
The production of hydrogen as a by-product in various industrial sectors, such as steel and caustic soda manufacturing, presents unique challenges in the capture, purification and efficient use of this valuable gas. Here's how the precision of measuring instruments helps to control and optimize these processes.
In metallurgy, particularly in steel production, hydrogen is often released during the reduction of iron oxides using alternative reducing methods. The pressure transmitter hydrogen sensor in this context helps to monitor and control the reaction environments where hydrogen is generated, ensuring safe and optimal working conditions for metal reduction. Temperature measurement is also critical, ensuring that furnaces and other equipment reach and maintain the temperatures required for efficient metal reduction while managing hydrogen production.
In the caustic soda industry, hydrogen is produced as a by-product of brine electrolysis in the chloralkali process. The pressure measurement is essential for controlling electrolytic cells, where pressure variations can influence electrolysis efficiency and process safety. The temperature probes are used to regulate cell temperatures, optimizing electrolytic reactions and the amount of hydrogen generated. The flow measurement controls the flow of brine and chemical solutions, ensuring a stable supply and continuous production.
In both cases, the analysers of gas are essential to determine the purity of the recovered hydrogen. This step is crucial in deciding whether the hydrogen can be used directly in other industrial processes, or whether it requires further purification. For example, the presence of impurities such as carbon monoxide may require the use of purification technologies such as pressure swing adsorption (PSA) before the hydrogen can be used safely.
Finally, the level measurement in hydrogen storage tanks helps to manage available stocks and plan the production or sale of surplus hydrogen. This not only enables efficient resource management, but also the strategic integration of hydrogen into the company's overall industrial activities.
Thus, integrating these measures into industrial processes is not just a matter of regulatory compliance, but an essential element in increasing efficiency, maximizing the yield of the hydrogen produced, and reinforcing the sustainable development commitments of the industries involved.
Specifications :
Coal gasification is a sophisticated method of hydrogen production that transforms coal into a hydrogen-rich gas mixture known as syngas.
Carbon injected into a furnace reacts with O2 in the air to form CO2 and/or CO, or reacts with water vapor to form CO and H2.
The resulting CO reacts with steam, dissolving into CO and H2. CO + H2O CO2 + H2. This process, which takes place in a high-temperature, pressurized environment, requires the use of advanced measurement technologies to guarantee the efficiency and safety of operations.
pressure transmitters are essential for precise control of operating conditions in the gasifier, where stable pressure is fundamental to the chemical reaction.
Temperature measurement plays a critical role in monitoring and controlling the high temperatures required for the gasification reaction.
The flowmeter ensures rigorous control of the quantities of oxygen and steam injected, key elements for optimum syngas production.
In addition, gas analysis is used to examine syngas composition and adjust process parameters in real time, ensuring maximum hydrogen production while minimizing impurities. Finally, level measurement helps to manage the storage tanks for inputs and finished products, ensuring continuous and efficient system supply.
Together, these measuring instruments enable precise and efficient management of coal gasification, making this process a vital component of the modern hydrogen industry.
Specifications :
Hydrogen production by thermochemical conversion, biomass thermolysis and photolysis represent innovative methods that exploit various energy sources to break down water molecules or other organic compounds into hydrogen. Each of these techniques requires specialized measuring instruments to optimize yields and ensure process safety.
For thermochemical conversion and thermolysis of biomass, where high temperatures are used to break down biomass into hydrogen and other gases, temperature measurement is crucial. It enables precise monitoring of reaction conditions, essential for achieving maximum efficiency.
Pressure regulation is also important to maintain a controlled environment, optimizing reaction and safety.
The analysers gas analyzers play a vital role in characterizing the gases produced and adjusting the reaction parameters accordingly, thus ensuring the purity of the hydrogen produced and the reduction of undesirable by-products.
In the case of photolysis, which uses sunlight to split water into hydrogen and oxygen, flow measurement is used to control water supply and gas release, ensuring continuous, efficient system operation.
Packaging and trucking are crucial to ensuring a smooth and secure hydrogen supply chain.
Pressure gauges play a vital role in monitoring the pressure at which hydrogen is compressed and maintained in storage tanks or cylinders during transportation. This avoids the risks associated with pressure increases that could compromise container integrity.
Temperature monitoring is essential to ensure that hydrogen does not undergo thermal variations that could cause dangerous pressure rises during storage and transport.
Flowmetering is essential for accurately quantifying the rate at which hydrogen is charged or discharged from storage facilities, enabling optimized management and accurate invoicing.
Gas analysis is also crucial: it ensures that the hydrogen remains free of contamination throughout its transit, preserving its purity for end uses.
Finally, level measurement is used to accurately determine the volume of hydrogen present in storage tanks during transport, ensuring clear knowledge of the quantities in circulation and helping to prevent overloads or product shortages.
Hydrogen dispensing stations act as nerve centers, linking hydrogen producers and end-users. Precision and safety at these stations are guaranteed by the specialized measuring instruments that orchestrate distribution.
Pressure control is fundamental to the safe distribution of hydrogen to vehicles or containers, ensuring that pressure during refuelling remains within safe parameters.
Temperature measurement is essential to control the temperature of the hydrogen and the station environment, two factors which influence the safety and efficiency of dispensing. Careful monitoring helps avoid pressure variations due to temperature changes.
As for flow meters, they ensure precise measurement of the quantity of hydrogen dispensed, essential for both inventory management and accurate billing to consumers.
Gas composition analysis is used to confirm hydrogen purity at the point of sale, a quality criterion that can determine the energy efficiency of hydrogen-powered vehicles.
Finally, level probes are essential for monitoring the quantity of hydrogen available for distribution, enabling efficient management of station reserves to meet demand on an ongoing basis. Together, these measures form the technological foundation for the safe, reliable operation of hydrogen filling stations, key elements of tomorrow's energy infrastructure.
Stationary fuel cells for power generation (Stationary PAC) use hydrogen to generate electricity cleanly and efficiently, and are equipped with a range of essential measuring instruments to optimize their operation and guarantee their safety.
Pressure gauges monitor the pressure of the hydrogen fed to the cells, ensuring that the gas is delivered at optimum levels for the electrochemical reaction. Temperature sensors are also essential, as they control the temperature within the fuel cells, preventing overheating which could damage components and reduce system efficiency.
Flow sensors ensure precise control of the flow of hydrogen and oxygen into the cells, which is vital for maintaining the right balance between reactants and maximizing energy production.
analysers gas sensors are used to monitor hydrogen quality and detect any contaminants that could affect cell performance or life. Finally, level probes are often integrated to monitor stored hydrogen levels, ensuring continuous supply without service interruption.
These measuring instruments are therefore essential for the safe and efficient operation of Stationary PACs, enabling real-time monitoring and rapid response to changes in operating conditions. Their use ensures that these systems can provide a reliable and sustainable source of energy, while supporting environmental objectives to reduce emissions and promote renewable energies.
Discover how Fuji Electric is transforming the future of energy with its hydrogen-measuring innovations unveiled at Hyvolution 2025.
June 09, 2024