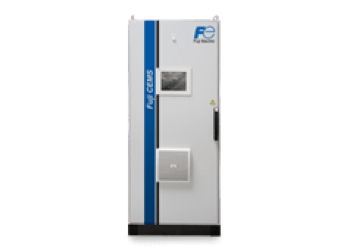
Gas instrumentation and analysis for industrial utilities includes technologies and methods for measuring and analyzing gas compositions in various industrial processes. These include gas detectors, on-line and portable analysers , aimed at optimizing performance, ensuring safety, and meeting environmental standards. These instruments measure the concentration of various gases, helping to control emissions, improve energy efficiency and guarantee air quality.
Fuji Electric provides integration instrumentation solutions for industrial utilities to:
Plant safety
Energy efficiency
Compliance with current standards
Monitoring and control of industrial utilities
Having a detailed map of energy consumption and highlighting the main areas where savings can be made helps to improve productivity, quality and competitiveness. Implementing state-of-the-art technologies and efficient operating practices is crucial to improving the energy efficiency of industrial utilities. Potential savings are often poorly exploited, whereas the gains to be made are both rapid and substantial.
Measuring instruments such as flow meters, level probes, energy meters and temperature probes enable you to monitor your processes precisely and continuously. pressure transmitterslevel probes, energy meters and temperature probes provide precise, continuous monitoring of your processes. These devices guarantee control of your energy consumption, with water metering, steam metering, thermal energy metering, condensate metering, electricity metering, compressed air metering or fuelmetering (gas, fuel oil and hydrogenmetering, etc.).
They help you detect possible drifts and malfunctions, prevent breakdowns, and optimize maintenance operations. Thanks to these field instruments, you can reduce industrial plant costs.
The analysers gas monitoring system enables you to monitor your atmospheric emissions andoptimize your industrial processes.
Industrial utilities are energy services essential to the smooth running of industrial production processes. They include electricity, water, steam, gas, compressed air and refrigeration. These utilities play a crucial role in industrial performance, helping to maintain product quality, reduce production costs and improve competitiveness.
Industrial utilities are energy services required to operate industrial production equipment and processes. They can be produced in-house or purchased from external suppliers. Industrial utilities are essential for maintaining product quality, reducing production costs and improving competitiveness.
Industrial utilities play an important role in the energy transition, as they can be used to reduce energy consumption and greenhouse gas emissions. Companies can adopt strategies to improve the energy efficiency of their industrial utilities, such as using renewable energy sources, implementing energy management systems and reducing energy losses.
The national low-carbon strategy is an action plan aimed at reducing greenhouse gas emissions in France and Europe. Decarbonizing industry is a key element of this strategy, as industry is one of the main sectors emitting greenhouse gases.
The aims of decarbonizing industry are to reduce greenhouse gas emissions and promote the use of renewable energy sources. The stakes involved in decarbonizing industry are high, as they can have a significant impact on business competitiveness and job creation. Companies need to adopt strategies to reduce their greenhouse gas emissions and improve their energy efficiency. Integrating renewable energies into the energy mix also helps to improve energy efficiency and reduce dependence on fossil fuels.
Our energy optimization solutions: Measure, visualize, monitor and optimize energy consumption
Steam | Fuel | Electricity | Cold | Air |
---|---|---|---|---|
Applications - Saturated steam - Superheated steam - Steam condensate - Flash steam | Applications - Natural gas - Domestic fuel oil - Heavy fuel oil | Applications Measuring active and reactive energy, active reactive and apparent power, power factor and current, voltage and frequency, etc. | Applications - Refrigerants - Heat transfer fluids | Applications Measuring the volume and mass of air flows |
Savings potential - Reduction of leaks - Improved purging - Isolation of out-of-service networks - Maintenance of purge system - Improved control and use - Reduced heat losses | Savings potential - Combustion optimisation - Efficiency calculation - Consumption monitoring | Savings potential - Improvement of network settings - Load distribution - Optimisation of sources of consumption - Modernisation of equipment, motors, inverters, etc. | Savings potential - Monitoring of thermal exchanges - Monitoring of clogging - Optimisation of maintenance operations - COP* monitoring *Coefficient of performance | Savings potential - Monitoring leaks - Optimisation of air network maintenance (monitoring filter clogging, etc.) - Keeping pressure levels as low as possible - Monitoring and optimizing energy consumption |
Measurement of steam parameters is essential to optimize processes using saturated and superheated fluids, such as those found in the chemical or petrochemical industries.
Our measurements instruments allow you measure energy flow rates; pressure levels which can be used for compensation purposes if needed along with temperature readings too! This allows companies create smart data that will help them establish relevant performance indicators while monitoring equipment's effectiveness from day-to-day.
Count energy with standardized measurements, develop relevant performance indicators and monitor the performance of industrial boiler plants
Fuel is a vital resource for the manufacturing industry, providing heat energy required for many key processes.
The industrial sector accounts for 20% of French energy consumption (36% gas and 40% electricity).
Gas and fuel oil are mainly used to produce heat for processes. Recovering the by-products and waste generated by industrial processes makes it possible to integrate these elements into a sustainable energy model, reducing dependence on fossil fuels and greenhouse gas emissions.
Hydrocarbons are used as raw materials in the chemical industry.
Through instrumentation, businesses can measure fuel consumption. Any kind of measurement can be done: from fuel oil and hydrocarbon flow rate to gas flow rate, pressure, temperature or combustion regulation analysis. The data gathered through instrumentation allows companies to make informed decisions about their process operations in order to make energy savings and to remain competitive.
Measuring fuel consumption, monitoring waste compliance and combustion efficiency in industrial heating systems
With the entry of competition into the electricity market, industries are finding it increasingly difficult to accurately determine their energy needs so that they can negotiate with power suppliers for optimised rates. Fuji Electric instrumentation is here to bridge that gap and ensure that utilities consume the right amount of energy. The instrumentation makes use of smart data for analysis and distribution of consumed electricity to calculate relevant performance indicators. This instrumentation also includes essential measurements such as power energy counter which allows businesses to remain competitive in a market where prices are constantly fluctuating.
Measure electrical consumption, analyze and distribute consumption and monitor energy performance indicators
Industrial air conditions, and refrigerant systems are used in a wide range of industries (pharmaceutical, chemical, etc), including heating and ventilating.
The food industry is the main user of refrigeration, accounting for up to 57% of the sector's electricity consumption, followed by cold production systems (process cooling circuits, data centers, public buildings, etc.).
Measure power consumption, monitor COP (coefficient of performance) and optimize refrigeration cycle performance
Compressed air is an extremely expensive process with a conversion rate that's less than 10%.
Savings of 15%-30% can be achieved by managing networks more accurately, choosing performance indicators wisely and exploiting data appropriately. These savings are available to many industries including glassworks, mechanical, automotive, plastic, smelting plant and engineering industries—or any other plant where accurate flow, pressure, temperature or power consumption information are necessary for effective operations.
Measure standard flow rates and power consumption, monitor air compressor pressure and efficiency
Energy performance indicators give you the ability to monitor your consumption accurately and continuously, detect possible drifts in machinery operation or malfunctions of equipment. They also help optimize maintenance operations for increased efficiency which ultimately frees up financial capacity that can be allocated towards developing our core business while ensuring high energy quality standards continue without interruption.
Engaging in an energy optimization process means:
Whatever your industrial sector(oil & gas, renewable energy, thermal energy or nuclear industry, chemical industry, paper industry, food & beverage, water & environment, pharmaceuticals, glassmaking, mechanics, metallurgy, steelmaking, etc.), our teams are there for you every step of the way.
We provide diagnostics, energy audits, consultancy, solutions, commissioning, operating assistance, calibration services, maintenance contracts and instrument training, so as to offer you the most appropriate response to your needs.
We can help you manage and make the most of your energy measures.
Control your energy costs with Fuji Electric France: measurement, control and regulation solutions to improve your competitiveness and accurate billing.
October 26, 2022
Audit, measure and analyze utility consumption to optimize costs quickly and efficiently, while boosting your competitiveness.
September 16, 2024
Boost your energy savings with Energy Savings Certificates (CEE)! Find out how to reduce your costs while supporting the energy transition.
June 16, 2024
Optimize the energy efficiency of your buildings by identifying the key levers. Discover how ultrasonic flowmeters play a crucial role in this optimization.
February 24, 2023