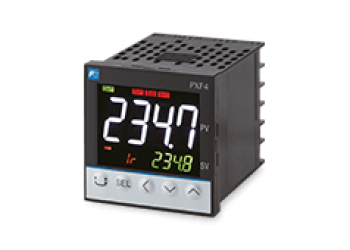
A temperature controller Pid is a temperature control instrument. The Pid function enables the controller to switch the heating element on or off up to the process setpoint.
Temperature is one of the basic factors in the success or failure of a finished product, so it's essential to take it into account in order to manage it as effectively as possible.
Temperature management can be controlled simply and automatically, thanks to temperature controllers featuring Pid technology. There are many ways of controlling temperature to optimize and automate the response of industrial processes.
On/Off control is the simplest and most widely used control system in industry.
When the measured value (PV) falls below the desired setpoint (SV), the output is triggered, activating the heating element. As soon as PV rises above the SV value, this output is deactivated, switching off your heating element. To maintain a stable range, this continuous cycle of on/off action occurs according to the setpoint you select.
This type of control is quite energy-intensive, requiring frequent on/off cycles of the heating element. In addition, this approach leads to fluctuations that can affect the production process and alter product quality.
Pid controllers are much more advanced than these all-or-nothing controllers, because they automatically adjust heating or cooling according to the temperature measurement. They keep the setpoint constant, counteracting temperature variations and their impact on the industrial process.
Pid is the abbreviation of the three actions Proportional, Integral and Derivative.
The operating principle of PID controllers is based on these three mathematical functions, invented by mathematician Nicolas Minorsky, who was seeking to automate the piloting of U.S. Navy ships.
Proportional Action (P) : The proportional variable P is used to measure the instantaneous error, act on it and generate a corrective action. The gain, which can be adjusted according to the system's needs, determines the speed and strength of the system's response. Each PID component then acts to balance the overall system behavior.
Integral action (I) : The integral variable is an important component that enables the system to adjust for errors accumulated in the past, and to correct small errors that a single proportional variable cannot correct.
Derivative Action (D): The derived variable is used to predict future error in order to minimize oscillations and attenuate response to change. The gain associated with this component must be properly defined in order to improve the speed and response time required by the system to achieve its overall objectives.
With these functions, the controller measures the process temperature and compares it with the setpoint. If it encounters a difference between these two values, also known as the "proportional band", the controller responds by adjusting the output to match the given setpoint. Thanks to the feedback principle, this corrective action prevents any disturbances that may occur.
In other words, Pid control with auto-tuning considerably improves the efficiency and stability of an industrial process control loop by automating temperature management with precision and reliability.
Fuji Electric offers other, more advanced and high-performance control modes. They provide optimal measurement and control for a wide range of industrial applications.
To fine-tune the controller's response to external changes, fuzzy logic control is used to suppress overshoot.
By inspecting the measured value, the fuzzy controller is able to avoid overshoot without affecting the start-up and temperature rise speed of the equipment.
In addition, reactions to disturbances are handled quickly and efficiently.
Thanks to thePID parameter auto-tuning function, you don't need to know everything about PID control to configure the settings.
Thanks to this 2-degree-of-freedom PID function with auto-tuning :
This PID2 control method for open-loop systems eliminates overshoot, regardless of how often the process is started and stopped. This control mode is ideal for processes requiring frequent stops during control phases.
At start-up, and whenever the setpoint changes or is disturbed by external factors, Pid parameters automatically adjust in response to temperature setpoint changes. Self-adaptive control ensures efficient process control whatever the setpoint selected.
Pid (Proportional, Integral, Derivative) control automates the management of an industrial process, for a variety of industrial applications.
Installing a PID controller allows you to control and regulate your process conditions, ensuring that temperatures remain within the desired setpoint.
For example, in the pharmaceutical industry, it's crucial to maintain stable measurements with precise temperature control in test laboratories to avoid errors and guarantee the accuracy of research and experimental results. If temperatures deviate from the ideal range, this can lead to unpredictable reactions and invalidate any experiments carried out. PID controllers provide an optimum solution to prevent these effects.
The pharmaceutical PID controller will send a control signal to automatically switch on the heating element and generate heat until the setpoint is reached. Heating is automatically adjusted according to the setpoint. This means your laboratory ovens, furnaces and incubators run optimally and safely.
Fuji Electric's range of Pid PXF series temperature controllers fully automate the temperature control and regulation of your industrial process.
This automation enables you to save money by avoiding temperature oscillations and variations that cause industrial rejects and excessive energy consumption.
For industries such as chemicals, thermal power or industrial utilities, precise temperature control is essential.
Installing a Pid controller will enable you to quickly and accurately correct any variations in the control loop.
This process control system is particularly effective for industrial boilers, where it ensures safe, efficient operation without exceeding the setpoint.
Its fast response time enables rapid adaptation to any situation. It corrects any deviations caused by process disturbances with speed and precision.
The PSC series process controller with color display provides essential functions to correctly regulate the temperature of the pressurized water contained in your industrial boiler.
This ensures maximum efficiency and safety for your industrial equipment.
Pid temperature controllers are the ideal devices for controlling pre-set temperatures in manufacturing operations.
By using temperature control with pid, you can set specific temperatures and times, allowing you to efficiently manage the different stages of the manufacturing process.
PXH multifunction controllers and PXF series PID controllers let you define up to 64 steps (ramps and stages) with different temperatures and durations. In other words, you'll be able to manage your manufacturing process with the utmost precision and over a wide range of production stages, using a single instrument.
The controllers feature a configuration menu directly accessible from the front panel, enabling you to configure them to suit your needs simply and precisely.
You can set a password to prevent any modification of the setpoint or PID parameters. This function ensures that the defined setting cannot be inadvertently altered.
You can also :
For more user-friendly, dynamic parameterization and operation, you can also connect your modular PID controllers to an industrial touchscreen HMI - Human Machine Interface - via modbus communication.
You don't have to configure your Pid controllers from the front panel.
You can also set them up from your workstation, directly on your computer using dedicated control software.
Installing this software will enable you to modify the values entered as often as necessary, for each controller.
This feature is very practical and useful for frequent temperature changes.
In addition, the software is easy to use and user-friendly, which is a real time-saver for manufacturers.
Thanks to the recording and supervision software installed on your computer and connected to your temperature controllers, you can monitor your process in real time .
Temperature traceability is mandatory in many industries, such as the food and pharmaceutical industries, but also in the aeronautics and automotive sectors, and in heat treatment control.
To guarantee the quality of finished products, it is important to be able to monitor the different temperatures to which they have been exposed during the industrial manufacturing process.
This is where the software's archiving function comes in, enabling you to provide a detailed report and analysis of control loop parameters.
Of all the control methods available, Pid control is the most reliable and precise.
Used to control temperature, flow rate, pressure, speed or level, Pid control allows you to automate and considerably improve the performance of the various stages of an industrial process.
Pid temperature controllers are therefore indispensable instruments for all industrial applications that need to pay particular attention to temperature control and regulation.