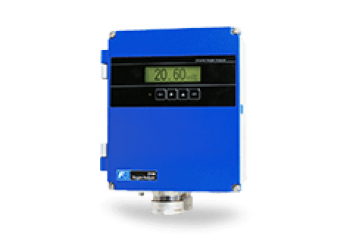
Zirconia oxygen converter - ZKM
ref : ZKMFrom
2922,00 € Request a quoteZirconia in-situ oxygen analysers are used to measure oxygen levels and combustion control in furnaces and boilers. The gas analysers are used to control the air-to-fuel ratio of burners in a controlled system to ensure an efficient process. This O2 gas analyser is perfect for controlling and optimizing excess air in a combustion. This measurement instrument provides significant fuel savings.
Ideal for combustion control of boilers, incinerators and furnaces, an oxygen analyser helps reduce CO₂, SOx and NOx emissions while saving your energy.
This gas analyser is specially designed for continuous measurement of oxygen concentration in flue gas and smoke from boilers in power plants, industrial furnaces (crematoria, glassworks, firing) and incinerators.
These zirconium oxide oxygen measurements are used to regulate the air-fuel ratio of burners in a controlled system to ensure optimum process efficiency in an industrial plant.
This instrument is ideally suited to control and optimize the excess air of a combustion. Therefore it allows an important saving on fuel consumption.
The operation of the in situ oxygen analyser is based on the property of zirconium oxide, also called zirconia, which conducts oxygen ions when heated.
This analyser obtains the O₂ concentration measurement by detecting the electromotive force generated by the difference in O₂ content between air and sample gas.
The ATEX type zirconia oxygen analyser is suitable for combustion monitoring in hazardous areas. These analysers comply with the most demanding international standards. They are CE, FM, ATEX and QAL1 certified.
The In-Situ O2 analyser with Zirconia probe offers an accurate measurement of ± 1% on the measured oxygen concentration. It is also very stable over time due to its zirconia probe technology. This system is suitable for processes with high temperatures up to 1500°C depending on the type chosen.
This probe is a very reliable and robust instrument, it can be used in the most difficult conditions (dust, smoke, etc.). Its construction with resistant materials such as 316L stainless steel guarantees an excellent resistance to humid and corrosive atmospheres.
The zirconium oxide analyser is equipped with a backlit LCD display for easy reading of results even in the darkest of places.
The transmitter is also equipped with an audible and visual alarm when preset limits are exceeded.
Service life
Easy to install
Wide temperature range
User-friendly operation
Operating principle and application
At the heart of this device is an in-situ zirconia sensor that guarantees fast, accurate oxygen measurement. Mainly dedicated to O2 measurement in non-combustible gas mixtures, this analyser is particularly suited to critical environments such as industrial heat production in refineries, petrochemical reactor furnaces, and other large combustion plants.
Exceptional Performance
The user-configurable measurement scale ranges from 0 to 2% up to 50% vol. oxygen. Exceptional repeatability of ≤ ± 0.5% PE and linearity of ≤ ± 2% PE ensure consistent, accurate performance under varied operating conditions.
Reactivity and Advanced Communication
With a fast response time of 4 to 7 seconds to reach 90% of response, theanalyser offers near-instantaneous measurement to adapt to rapidly changing conditions. Analog output of 4-20 mAdc or 0-1 Vdc offers flexibility in data collection. In addition, contact outputs include 6-point SPST-NO contacts for critical functions such as high/low limit alarm, maintenance in progress, purge in progress, calibration in progress, and the analyser faults.
Integrated Security and Advanced Options
Integrated safety functions, such as power cut-off in the event of thermocouple failure, add an extra layer of protection. The lockout function prevents potential operating errors. Advanced options include combustion efficiency display, cleaning, automatic calibration, selector valve and flowmeter, providing further customization to the specific needs of each application.
Installation and power supply
The analyser offers installation flexibility with panel- or pipe-mounting options. The cable length between controller and detector can be up to 100 meters, offering adaptability to a variety of factory configurations. Power can be supplied at 100-120 Vac or 200-240 Vac, at a frequency of 50/60 Hz, guaranteeing worldwide compatibility.
Select the required modules combination according to the process conditions using below table.
Process conditions | Module selection | |||||||||||||||||||||||||||||||||||||||||||||||||||||||||||||||||||||
Application example | Temperature | Dust | Tube material | Back purge | Tube type | Tube code (*) | Detector type | |||||||||||||||||||||||||||||||||||||||||||||||||||||||||||||||
Gas boiler | ≤ 600 °C | ≤ 0.1 g/Nm³ | SS316 | No | Standard guide tube | 631B562-0# | ZFK8 | |||||||||||||||||||||||||||||||||||||||||||||||||||||||||||||||
Biomass, oil, coal boiler/ Incinerator | ≤ 600 °C | ≤ 5 g/Nm³ | Yes | Guide tube with backpurge | 631B563-0# | |||||||||||||||||||||||||||||||||||||||||||||||||||||||||||||||||
≤ 25 g/Nm³ | Yes | Direct tube for high particulate | 631B673-0# | |||||||||||||||||||||||||||||||||||||||||||||||||||||||||||||||||||
Yes | Direct tube for HP with deflector | 631B677-0# | ||||||||||||||||||||||||||||||||||||||||||||||||||||||||||||||||||||
≤ 1000 °C | ≤ 0.2 g/Nm³ | SS310 | No | Dual Flange (DF) Guide tube for high temperature (HT) | 631B685-0# | ZFKH | ||||||||||||||||||||||||||||||||||||||||||||||||||||||||||||||||
≤ 5 g/Nm³ | Yes | DF Guide tube for HT with backpurge | 631B684-0# | |||||||||||||||||||||||||||||||||||||||||||||||||||||||||||||||||||
≤ 25 g/Nm³ | Yes | Direct tube for HT and HP | 631B675-0# | |||||||||||||||||||||||||||||||||||||||||||||||||||||||||||||||||||
Yes | Direct tubefor HT and HP with deflector | 631B678-0# | ||||||||||||||||||||||||||||||||||||||||||||||||||||||||||||||||||||
Incinerator / Furnace / Glass / Metal industry | ≤ 1300 °C | ≤ 0.2 g/Nm³ | Kanthal | No | Guide tube for very high temperature | 631B682-0# | ||||||||||||||||||||||||||||||||||||||||||||||||||||||||||||||||
≤ 5 g/Nm³ | Yes | Guide tube for very high temperature with backpurge | 631B683-0# | |||||||||||||||||||||||||||||||||||||||||||||||||||||||||||||||||||
≤ 800 °C | ≤ 0.5 g/Nm³ | SS310 | Yes | ZTA ejector module | ZTA2 | ZFK8 | ||||||||||||||||||||||||||||||||||||||||||||||||||||||||||||||||
≤ 1500 °C | SiC | Yes | ZTA ejector module | ZTA1 | ||||||||||||||||||||||||||||||||||||||||||||||||||||||||||||||||||
Remarks | (*) The last digit of the tube code is dedicated to the tube insertion length as per below list: | |||||||||||||||||||||||||||||||||||||||||||||||||||||||||||||||||||||
"1" = 300 mm | "2" = 500 mm | "3" = 750 mm | "4" = 1000 mm | "Z" = specific length -> consult Fuji |
- In case of very humid gas, keep the flange hot enough to prevent condensation
- In case of highly corrosive gas, please consult Fuji for special materials
- If the gas flow is lower than 5 m/s, use ejector module instead of flow tube
We help you configure your oxygen measurement platform for :
With the data from this questionnaire, our engineers will select the best combination for reliable and accurate oxygen analysis. Do not hesitate to send us, in writing or in the form of a diagram, on the last page of this questionnaire or as an attachment, any additional information that would allow us to understand the specifics of your process, and thus adapt the configuration of your O2 analysis solution.
Download the questionnaire so that we can suggest the best solution for your application!