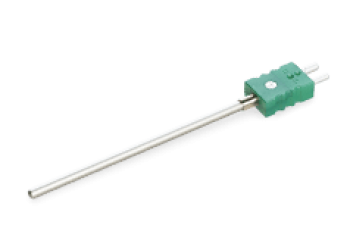
A thermocouple probe is a sensor for measuring temperature. Thermocouples are versatile temperature sensors and are commonly used for a wide range of applications: from industrial thermocouples to standard thermocouples for domestic appliances and equipment.
The thermocouple probe is an indispensable temperature measurement instrument in many industrial and scientific applications. Thanks to its robustness, accuracy and wide measuring range, it is widely used in fields as varied as metallurgy, power generation, the chemical industry and scientific research.
The device works on the principle of the Thomas Johann Seebeck effect, named after the physicist of the same name, where a voltage is generated between two dissimilar metals when they are exposed to a temperature difference. This voltage is then converted into a temperature measurement.
Despite their apparent simplicity, thermocouples require a thorough understanding of their operation, the types available, as well as mounting and wiring techniques to ensure reliable and accurate measurements.
Let's explore in detail the different types of thermocouples, the principle of operation, installation and wiring methods, and best practices for optimizing their use in various applications.
The thermocouple probe works by combining two dissimilar metals, connected at an end called the "hot junction". When a temperature difference occurs at this junction, an electric current is created in the circuit, generating an electromotive force (EMF). The value of this EMF depends on the properties of the metals used and the temperature difference between the hot junction and a reference junction, often referred to as the "cold junction".
The metals used in thermocouples are of homogeneous quality, enabling the device to withstand different temperature gradients along its entire length without altering the FEM. This means that the thermocouple can measure temperatures accurately, even under variable conditions.
Measuring devices such as digital displays, PLCs and temperature controllers are designed to accept thermocouples directly. They automatically manage cold junction compensation, essential for accurate readings.
The alloys used to manufacture thermocouples are generally available in wire form, making them easy to manufacture and handle.
To choose the most suitable thermocouple for your application, it is essential to :
Knowledge of materials
Know how it works
Controlling temperature ranges
Knowing the different types of probe
Understanding assembly and wiring
Take insulation resistance into account
Each type of thermocouple probe has specific output (voltage) characteristics, and requires appropriate calibration and measuring equipment to ensure accurate and reliable readings.
Thermocouples offer a number of advantages that make them indispensable in many industrial and scientific applications.
Reduced cost
High-temperature resistance and stability
Small dimensions and a wide range of diameters
Positioning the hot spot
Short response times
Good vibration resistance
By weighing up these advantages and disadvantages, it is possible to determine whether thermocouples are suitable for a specific application. For environments requiring fast, reliable temperature measurement at low cost, thermocouples are often the ideal solution.
Mounting and wiring a thermocouple probe are crucial steps in ensuring accurate and reliable temperature measurements. Here are the key steps and considerations:
By following these recommendations, thermocouple probe mounting and wiring can be carried out efficiently, guaranteeing optimum instrumentation performance.
Thermocouples are often exposed to harsh environments, subject to electrical, electromagnetic and other types of interference. To compensate for temperature measurement disturbances caused by such interference, metal-sheathed thermocouples are fitted with an insulation resistor between the wires and the protector.
This insulation resistance, rigorously tested at the factory, ranges from 1000 to 5000 MW minimum at 100 to 500 Vdc, depending on thermocouple diameter and at ambient temperature. These datasheet values are valid for thermocouple lengths of less than 1 meter, in accordance with current standards.
It is important to note that these resistance values decrease when the thermocouple is subjected to high temperatures, until they become almost zero at very high temperatures. Effective insulation of thermocouples is therefore crucial to ensure accurate and reliable measurements, particularly in extreme temperature conditions and disturbed environments.
This is why it is always preferable to use measuring instruments with galvanic isolation input / output or input / output / power supply.
A thermocouple is a temperature sensor consisting of two wires of different metals welded together at one end, called the hot junction. When this junction is exposed to a temperature, it generates an electrical voltage proportional to that temperature, due to the Seebeck effect.
The main types of thermocouples are :
A thermocouple works by measuring the electrical potential difference between the hot junction and a reference junction, often maintained at a known temperature. The voltage produced is converted into a temperature measurement using calibration tables.
Cold junction refers to the reference junction of a thermocouple, where the wires are soldered to metal terminals. Cold junction compensation is a technique used to compensate for temperature variations at this junction to ensure accurate measurements.
The choice of a thermocouple depends on several factors:
Thermocouples are manufactured from various combinations of metals and alloys, such as :
The Seebeck effect is the phenomenon whereby a temperature difference between two different materials generates an electrical voltage. This effect is the basis of thermocouples.
Calibrating a thermocouple involves comparing its measurements with those of a known standard at different temperatures, and adjusting the readings accordingly to guarantee accuracy.
Thermocouples are used in many sectors and applications, including :