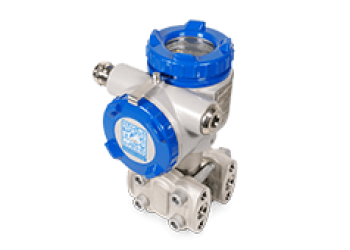
Sensor de presión diferencial - FKC
ref : FKCEn
1385,00 € Solicitar un presupuestoPara calcular la precisión de un transductor de presión, es necesario tener en cuenta tanto la precisión de referencia como el rendimiento in situ. El error total probable (TPE ) se obtiene sumando incertidumbres como la precisión del intervalo de medición calibrado, los efectos de la temperatura ambiente y los impactos de la presión estática.
En el vasto mundo de la ingeniería de procesos, la medición de la presión es la piedra angular de unas operaciones eficaces, seguras y fiables.
A medida que las tecnologías evolucionan y las industrias progresan, la necesidad de medir la presión con precisión es cada vez más importante.
Para los ingenieros de mantenimiento, instrumentación y control y los ingenieros de procesos, navegar por los entresijos de los sensores de presión puede ser a veces como buscar una aguja en un pajar.
Pero no tema. Para lograr un rendimiento óptimo, es esencial comprender los sutiles matices que influyen en la precisión de un sensor.
Este artículo aborda el tema de los transductores de presión, con el fin de ofrecer a los ingenieros de mantenimiento una visión del método para obtener mediciones precisas de la presión.
Empezaremos analizando la importancia de definir la precisión necesaria para aplicaciones de procesos específicos. A continuación, desentrañaremos la diferencia entre el rendimiento in situ y la precisión de referencia, destacando por qué esta distinción es crucial.
Más adelante, descifraremos la multitud de condiciones de funcionamiento que puede encontrar un transductor de presión: desde temperaturas ambiente fluctuantes hasta presiones estáticas variables, y sus respectivos efectos. También se tratarán el desplazamiento del cero, el desplazamiento del rango y sus ramificaciones acumulativas.
Por último, le proporcionaremos una metodología completa para calcular el error total probable de un sensor de presión.
Al final de este artículo, esperamos que haya adquirido los conocimientos necesarios no sólo para seleccionar el transductor de presión adecuado, sino también para garantizar su precisión durante toda su vida útil. Emprendamos juntos un viaje instructivo.
El primer paso consiste en definir el rendimiento exigido por la aplicación industrial para el punto de medición de la presión.
El rendimiento in situ de los transductores de presión debería situarse normalmente entre el 0,5% y el 2,0% del intervalo calibrado, dependiendo de la aplicación. Por término medio, se esperan los siguientes objetivos de rendimiento para todas las clasificaciones de servicio: seguridad y eficiencia de la planta al 0,5%, control medioambiental al 1,0%, sistema Scada y sistema de control distribuido al 1,5%, y sistema de monitorización de la planta y optimización del proceso al 2, 0%. Por supuesto, se trata sólo de promedios y algunos clientes tendrán expectativas mayores o menores en función de sus necesidades específicas. No obstante, estas cifras dan una idea general del nivel de rendimiento que buscan nuestros clientes.
El rendimiento in situ no debe confundirse con la precisión de referencia.
Hay dos conceptos distintos cuando se trata de sistemas de medición:
Es la precisión de un sensor de presión en condiciones específicas y controladas, normalmente en el laboratorio. Proporciona una norma o referencia con la que se puede comparar el rendimiento del sensor. La precisión de referencia incluye los efectos combinados de la no linealidad, la histéresis y la no repetibilidad en estas condiciones definidas.
Se refiere al rendimiento de un sensor o sistema de medición en condiciones reales o en el entorno al que está destinado.
Hay una serie de factores que pueden influir en el rendimiento in situ, como las variaciones de la temperatura ambiente, el efecto de la presión estática, la estabilidad a lo largo del tiempo, la influencia de la tensión de alimentación, la posición de montaje y otros factores ambientales.
El rendimiento in situ puede diferir de la precisión de referencia debido a estas influencias externas.
En la práctica, mientras que un sensor de presión puede tener una excelente precisión de referencia en condiciones controladas, su rendimiento in situ puede variar en función de las complejidades e imprevisibilidades del entorno real. Por tanto, es esencial tener en cuenta estos dos factores a la hora de evaluar o desplegar un sensor de presión para una aplicación específica.
El segundo paso consiste en definir las condiciones de funcionamiento a las que estará expuesto el dispositivo.
Dependiendo de la aplicación, los transmisores de presión pueden estar sujetos a variaciones significativas de la temperatura ambiente.
Por ejemplo, si un sensor de presión se utiliza al aire libre, la temperatura ambiente puede variar de -20°C a 60°C. Esto es muy diferente del uso en un laboratorio, donde la temperatura ambiente es estable y está climatizada.
El otro parámetro a tener en cuenta es la presión estática en el proceso.
En el caso de la medición de la presión diferencial, cuanto mayor sea la presión estática, menor será la precisión. En el caso de los sensores de presión absoluta y relativa, el efecto de la presión estática es nulo.
Conocer estos factores que pueden influir en la precisión permite calcular el Error Total Probable (TEP), que define la precisión del transductor de presión en las condiciones de instalación de la aplicación cuando se combinan todas las fuentes individuales de error. Este error total de funcionamiento es la diferencia entre la desviación de medición más positiva y la más negativa con respecto a la presión real. Se calcula combinando todos los errores posibles en las condiciones de funcionamiento de la aplicación.
El valor del error total probable se utiliza para definir el peor rendimiento del transmisor de presión instalado in situ.
Factores como la temperatura ambiente y la presión estática tienen cierta influencia en la precisión y el rendimiento del sensor de presión. Afectan tanto al punto cero como al rango de medición establecido de los transmisores de presión, lo que provoca desviaciones o imprecisiones en la medición.
En primer lugar, hemos determinado la precisión necesaria in situ para la aplicación, hemos determinado los parámetros de instalación que influyen en la precisión de nuestra medición y su influencia en el desplazamiento del cero y el desplazamiento de la escala.
El siguiente paso consiste en calcular el error total probable utilizando las especificaciones disponibles en el sitio web del fabricante del transductor de presión (especificaciones técnicas). Este cálculo es la suma de las raíces cuadradas de las incertidumbres asociadas a la precisión de referencia y a factores de instalación como la temperatura ambiente y el efecto de la presión estática.
El error total probable del dispositivo incluye la precisión de referencia, el efecto de la temperatura ambiente, el efecto de la presión estática y se calcula mediante la siguiente fórmula TPE:
Error total probable = ± √ ((E1)²+(E2)²+(E3)²)
E1 = Precisión nominal de la escala calibrada o precisión de referencia
E2 = Efecto de la temperatura ambiente
E3 = Efecto de la presión estática
E1. Precisión nominal o de referencia
La precisión nominal debe calcularse sobre la escala calibrada o ajustada. La precisión de referencia incluye los errores de incertidumbre máximos por histéresis, no linealidad y no repetibilidad.
E2. Efecto de la temperatura ambiente
Los sensores de presión se calibran en el laboratorio a una temperatura ambiente estable. La temperatura ambiente en el lugar de aplicación puede ser diferente. Esta temperatura influye en los componentes electrónicos del instrumento de medición y puede dar lugar a una medición inexacta. Los fabricantes de sensores de presión, como Fuji Electric, suelen expresar este efecto en incrementos de 28 °C.
E3. Efecto de la presión estática
Los errores de presión estática pueden deberse a varios fenómenos en el interior del sensor de presión. Entre ellos, la deformación de las membranas metálicas bajo la presión de la línea y el equilibrio de los volúmenes de aceite de llenado. Los proveedores suelen definir la influencia de la presión estática cada 10 MPa de variación de presión. Los efectos de la presión estática en un transductor de presión diferencial pueden manifestarse en desplazamientos del cero y del span. A veces se denomina "efecto de presión estática" o "efecto de presión de línea".
Efecto sobre cero :
Es la desviación de la señal de salida del sensor cuando no hay presión diferencial en el transmisor, pero sí presión estática o presión en la línea.
Consejo: El efecto sobre el cero puede eliminarse "poniendo a cero" el transmisor en condiciones de presión estática, lo que significa que el transmisor puede recalibrarse o ajustarse bajo presión estática para devolver su punto cero al nivel de referencia correcto. Esto compensa eficazmente los efectos de la presión estática en la lectura cero.
Efecto sobre la escala :
Es el cambio en el rango de salida del transmisor debido a la presión estática o a la presión de la línea.
Para nuestro ejemplo, consideraremos las siguientes condiciones de servicio para nuestra aplicación.
Utilizamos las siguientes especificaciones para el sensor de presión diferencial Fuji Electric FKC para calcular el rendimiento general.
Descargue la especificación para descubrir las características técnicas del sensor de presión eléctrico Fuji.
Así que, en primer lugar, consideremos el modelo adecuado para el rango de medición de presión requerido y para las condiciones de funcionamiento de la aplicación siguiendo esta guía de selección de transductores de presión.
El ajuste de la escala debe establecerse lo más cerca posible del límite superior del rango de la célula del sensor para obtener la mejor precisión.
Para una medición de presión de 0-100 mbar, elegimos el modelo FKC..33 que ofrece el rango más cercano de 0/320 mbar.
Modelos | Límite de presión estática MPa {bar} | Rangos de medida kPa {mbar} MIN | Rangos de medición kPa {mbar} MAX | Posibles ajustes kPa {m bar} |
---|---|---|---|---|
FKC 11 | -0,1 a + 3,2 {-1 a + 32} | 0,1 {1} | 1 {10} | ±1 {±10} |
FKC 22 | -0,1 a + 10 {-1 a + 100} | 0,1 {1} | 6 {60} | ±6 {±60} |
FKC 33 | -0,1 a + 16 {-1 a + 160} | 0,32 {3,2} | 32 {320} | ±32 {±320} |
FKC 35 | -0,1 a + 16 {-1 a + 160} | 1.3 {13} | 130 {1300} | ±130 {±1300} |
FKC 36 | -0,1 a + 16 {-1 a + 160} | 5 {50} | 500 {5000} | ±500 {±5000} |
FKC 38 | -0,1 a + 16 {-1 a + 160} | 30 {300} | 3000 {30000} | ±3000 {±30000} |
FKC 43 | -0,1 a + 42 {-1 a + 420} | 0,32 {3,2} | 32 {320} | ±32 {±320} |
FKC 45 | -0,1 a + 42 {-1 a + 420} | 1.3 {13} | 130 {1300} | ±130 {±1300} |
FKC 46 | -0,1 a + 42 {-1 a + 420} | 5 {50} | 500 {5000} | ±500 {±5000} |
FKC 48 | -0,1 a + 30 {-1 a + 300} | 30 {300} | 3000 {30000} | ±3000 {±30000} |
FKC 49 | -0,1 a + 30 {-1 a + 300} | 500 {5000} | 20000 {200000} | {+20000,-10000} {+200000,-100000} |
Precisión del campo de medida calibrado o precisión de referencia
Precisión: (incluyendo linealidad, histéresis y repetibilidad) |
Para modelos de 32 kPa a 3000 kPa |
MPE > 1/10 de la escala máxima: ±0,065% de MPE o ±0,04% de MPE como opción |
EMR < à 1/10 de l’échelle maximale : ± (0.015 + 0.005 × Ech.max/EMR ) % de l’EMR |
La mejor precisión de referencia, incluidos los errores máximos de incertidumbre por histéresis, no linealidad y no repetibilidad, es de ± 0,04% de la escala para el transmisor de presión FKC de Fuji Electric.
E1 = 0,04 % *100
E1= 0,04 mbar
Efecto de la temperatura ambiente
Influencia de la temperatura |
---|
Los valores que se indican a continuación corresponden a variaciones de temperatura de 28°C entre -40°C y +85°C. |
Rango de medición máx. | Efecto sobre cero (% de TRA) | Efecto total (% de TRA) |
---|---|---|
"1"/100 mmCE {10 mbar} "2"/600 mmCE {60 mbar} | ± (0,125+0,1 Ec.máx/EMR)% (0,125+0,1 Ec.máx/EMR) | ± (0,15+0,1 Ech.max/EMR)% (0,15+0,1 Ech.max/EMR) |
"3"/32kPa {320mbar} "5"/130kPa {1300mbar} "6"/500kPa {5000mbar} "8"/3000 kPa {30000mbar} "9"/20000 kPa {200000mbar} | ±(0,075+0,0125 Ec.máx/EMR)% (0,075+0,0125 Ec.máx/EMR) | ±(0,095+0,0125 Ec.máx/EMR)% (0,095+0,0125 Ec.máx/EMR) |
En nuestro ejemplo, la diferencia de temperatura ambiente es de 28°C.
Aquí consideramos el efecto total del efecto de la temperatura.
E2 = ± (0,095 + 0,0125*320)%
E2= ± 0,135 mbar
Influencia de la presión estática
Presión estática | Efecto sobre el cero (% de la escala máxima) |
---|---|
"1" / 100 mmCE {10 mbar} "2" / 600 mmCE {60 mbar} | ± 0,1% / 0,1 MPa {1 bar} ± 0,063% / 1 MPa {10 bar} |
"3" "4" | ±0,035% / 6,9 MPa {69bar} ±0,035% / 6,9 MPa {69bar} |
Aquí estamos considerando el desplazamiento del cero del efecto de la presión estática.
E3 = ± 0,035*320%
E3 = ± 0,112 mbar
Ahora podemos calcular el error total probable.
Error total probable (ETC)
Error total probable = ± √ ((E1)²+ (E2)²+ (E3)²)
E1= Precisión nominal de la escala calibrada
E2= Efecto de la temperatura ambiente a 28°C
E3 = Efecto de la presión estática a 6,9 MPa
TPE = SQRT ((0.04)^2+(0.135)^2+(0.112)^2)
TPE= 0.179 mbar
TPE= 0.179 % de span
La aplicación del proceso requería una precisión de ± 0,2% del intervalo. El sensor medirá una presión diferencial de 100 mbar en condiciones normales de funcionamiento. El rendimiento requerido del sensor in situ será de ±0,5 mbar. Podemos concluir que el sensor de presión diferencial FKC de Fuji Electric es adecuado para esta aplicación. Para completar nuestro análisis del rendimiento de la presión, podemos añadir un factor adicional que influye en la precisión de la presión in situ.
Efecto de sobrepresión
La sobrepresión se refiere a una situación en la que la presión supera el rango máximo calibrado del dispositivo de medición. Estas condiciones pueden darse en caso de accidente o situación anormal. La precisión de los sensores de presión también se ve afectada por la sobrepresión. Los fabricantes de sensores de presión, como Fuji Electric, suelen expresar este efecto en términos de presión máxima de trabajo.
Presión estática | Efecto sobre el cero (% de la escala máxima) |
---|---|
"1" / 100 mmCE {10 mbar} "2" / 600 mmCE {60 mbar} | ± 0,96 % / 3,2 MPa {32 bar} ± 0,31 % / 10 MPa {100 bar} |
"3" "3" "4" "4" | ± 0,10 % / 16 MPa {160 bar} FKC 35, 36, 38 ± 0,15 % / 16 MPa {160 bar} FKC 33 ± 0,26 % / 42 MPa {420 bar} FKC 43, 45, 46 ± 0,06 % / 10 MPa {100 bar} FKC 48, 49 |
E4 = ± 0,15*320%
E4= ± 0,6 mbar
Ahora podemos calcular la precisión total, incluido el efecto de sobrepresión de la gama.
Precisión total = ± √ ((E1)²+(E2)²+(E3)²+(E4)2)
TA = SQRT ((0.04)^2+(0.135)^2+(0.112)^2+(0.6)^2)
TA = 0.62639 mbar
TA = 0.62639 % de span
La medición de la presión sigue siendo un aspecto fundamental para garantizar la eficacia y la seguridad de las operaciones en el ámbito de la ingeniería de procesos. Su precisión es primordial, dada la diversidad y complejidad de las aplicaciones en distintos sectores.
La exploración exhaustiva de los transductores de presión en este artículo ha puesto de relieve la importancia de comprender tanto la precisión de referencia como el rendimiento in situ, así como los factores que influyen en estos parámetros, incluidos los efectos de la temperatura ambiente, los impactos de la presión estática, los desplazamientos del cero y los desplazamientos del span.
Mediante una explicación sistemática, hemos desvelado cómo calcular el Error Total Probable (TPE), teniendo en cuenta diversas incertidumbres como la precisión del span calibrado, las influencias de la temperatura ambiente y los efectos de la presión estática. El ejemplo presentado, que utiliza las especificaciones del sensor de presión diferencial FKC de Fuji Electric, simplifica aún más la aplicación práctica de estos conocimientos.
En esencia, a la hora de seleccionar un transductor de presión, es imprescindible asegurarse de que no sólo cumple los parámetros de rendimiento exigidos, sino que también resiste las condiciones variables del emplazamiento, garantizando su precisión durante toda su vida operativa. Mediante la integración de la información proporcionada, los ingenieros de mantenimiento y procesos pueden sin duda tomar decisiones más informadas, mejorando la fiabilidad y eficiencia de sus sistemas.
A la hora de elegir un sensor de presión, es importante optar por un dispositivo que tenga un impacto mínimo en el medio ambiente.
La avanzada tecnología de célula flotante de los transductores de presión de Fuji Electric ofrece una alta inmunidad a las variaciones de temperatura, la presión estática y la sobrepresión habituales en la industria de procesos, y reduce significativamente el error de medición global.
Los transductores de presión de clase de alto rendimiento de Fuji Electric están diseñados para revolucionar la medición de la presión. Se caracterizan térmicamente durante el proceso de fabricación para mejorar la precisión de referencia y minimizar la influencia de la temperatura ambiente y la presión estática.
Este proceso único de caracterización térmica, conocido como giro 4D, permitió caracterizar la célula del transmisor de presión en un rango de temperaturas de -40 a +85 °C.
Los datos se recogen durante el proceso de fabricación registrando el desplazamiento del cero y el intervalo a diferentes temperaturas mediante un proceso de fabricación automatizado. Se realiza un algoritmo de ajuste de curvas no lineales para caracterizar el comportamiento único del sensor de presión.
Los datos de compensación se cargan continuamente en cada célula del transmisor de presión durante este proceso para compensar activamente los efectos del entorno térmico. El resultado es una precisión de referencia (incluyendo histéresis, no linealidad y no repetibilidad) de menos del +0,04% del fondo de escala en este amplio rango de temperatura compensada.
Elimine posibles errores al medir la presión diferencial: ahorre tiempo y energía confiando en un único instrumento diseñado específicamente para mediciones precisas de presión diferencial.