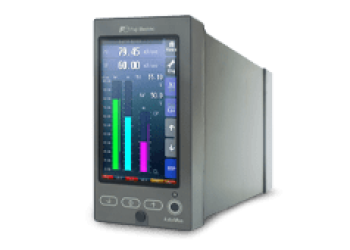
Controlador multifunción - Serie PSC100 - 2 bucles
ref : PSC100En
2928,00 € Solicitar un presupuestoLa cuestión del rendimiento energético en las industrias metalúrgica, siderúrgica y de fundición es crucial para que el sector logre con éxito su transición energética. Para ahorrar energía y reducir la factura energética y la huella de carbono, se puede recurrir a una serie de instrumentos de medición y análisis adecuados(análisis de gases, medición de la presión, medición del caudal, medición de la temperatura, medición del nivel). Ahorrar y optimizar el consumo energético de cada proceso está al alcance de todos los fabricantes.
Los instrumentos de medición de Fuji Electric ayudan a las empresas metalúrgicas en todas las fases de su proceso de fabricación para :
Control de calidad del metal
Cumplimiento de las normas vigentes
Eficiencia energética
Seguridad del personal y de las instalaciones
En el horno de sinterización, los polvos de las materias primas (minerales, piedra caliza y agua) se someten a calor para producir una pieza compacta.
Las piezas pasan por el horno a diferentes temperaturas, luego se enfrían y finalmente se calibran para obtener la forma deseada.
En este proceso, es necesario controlar la temperatura en el interior del horno, así como la relación aire-combustible y las emisiones nocivas.
La coquería transforma el carbón en coque mediante un proceso de destilación seca.
El coque es un combustible que se obtiene por pirólisis de la hulla (a 1100°C) en una coquería, al abrigo del aire, durante varias horas.
Para optimizar este proceso, son esenciales el control de la combustión y la vigilancia de los gases de escape.
La torre de enfriamiento, o sistema de enfriamiento de coque seco (CDQ), enfría el coque incandescente hasta una temperatura adecuada para su transporte. Se trata de un sistema de recuperación de energía. Durante el proceso de rociado con agua, el calor emitido por el coque incandescente se recupera y se utiliza para producir electricidad o vapor.
Es necesario controlar los gases, CO yH2, para evitar explosiones durante el temple.
El alto horno transforma el mineral de hierro aglomerado en fundición líquida. El mineral de hierro y el coque se cargan desde arriba. El aire caliente (1250°C), soplado en la base del alto horno, reacciona con el coque y el carbón pulverizado para formar un gas reductor que absorbe el oxígeno del mineral de hierro. Al mismo tiempo, se crea el calor necesario para la fundición de los minerales reducidos. Durante este proceso se generan grandes cantidades de gases (CO yCO2).
Para obtener el mejor rendimiento del alto horno, es necesario controlar la calidad del hierro fundido, controlar la combustión del horno y vigilar las emisiones de gases.
El hierro fundido se vierte en el convertidor, que contiene chatarra. Se insufla oxígeno puro en el baño de metal para quemar el exceso de carbono y las impurezas. El resultado es un acero líquido conocido como "acero salvaje". No es necesario generar calor adicional, ya que el calor generado durante la oxidación se sopla en el convertidor. Los gases de combustión producidos en el convertidor se reutilizan para generar electricidad o para calentar el proceso de laminación.
Para lograr una transformación óptima del hierro fundido en acero líquido, es necesario controlar el proceso de descarburación y la cantidad de oxígeno insuflado.
Los desgasificadores al vacío se instalan en muchos altos hornos y acerías para mejorar la pureza del acero . La desgasificación es un proceso metalúrgico que consiste en añadir una cantidad de aluminio antes del acero y, a continuación, inyectar argón en el acero fundido para reducir el contenido deH2,02 y N2 y eliminar determinadas inclusiones no metálicas.
El acero fundido descarburado en el convertidor se inyecta en una cuchara y se transporta a un equipo de colada continua para su colada (planchón, palanquilla o bloom).
Se vierte gas argón en la cuchara para evitar la oxidación del acero fundido.
Es necesario controlar el oxígeno para garantizar que no haya oxígeno en el interior de la cuchara.
Los desbastes de acero se calientan en el horno de recalentamiento (de 800°C a 1000°C) para que se ablanden lo suficiente para ser laminados.
El control de la combustión es necesario para llevar el metal a una temperatura que permita transformarlo en condiciones óptimas de calidad, productividad y eficiencia energética, reduciendo al mismo tiempo las emisiones contaminantes.
El planchón se calienta en un horno a 1.200 °C para que el metal sea más maleable. A continuación se adelgaza y se estira mediante aplastamiento progresivo entre los cilindros del tren de laminación. La banda de acero se transforma en bobinas o chapas de 1,2 a 20 milímetros de espesor. A continuación, las bobinas se someten a una segunda reducción en frío para obtener un producto tan fino como una hoja de papel (hasta 0,1 milímetros de grosor).
Durante estos procesos, deben vigilarse y controlarse los componentes gaseosos ligados al potencial de carbono(CO2, CO, CH4, NH3,H2 u O2).
Descubra cómo los analizadores de gases ayudan a reducir los contaminantes y fomentan el desarrollo de energías limpias para un medio ambiente sostenible.
09 de junio de 2024