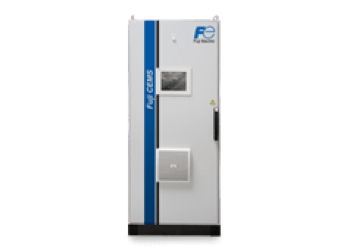
Avete deciso di acquistare o sviluppare un sistema dianalisi dei gas per il vostro processo industriale. Si tratta di una decisione molto importante che avrà un impatto sull'efficienza e sulle prestazioni dell'impianto.
Quando si progetta un sistema di analisi dei gas per un ambiente industriale, ci sono 6 punti chiave da considerare.
In questo blog post li analizzeremo in dettaglio e spiegheremo come possono influire sul successo complessivo delle vostre soluzioni di analisi dei gas.
Quando si integra un analizzatore di gas in un processo industriale, la scelta della tecnologia o delle tecnologie di rilevamento da utilizzare è fondamentale. Esiste un'ampia gamma di tecnologie, come l'infrarosso (IR), la conducibilità termica (TCD ), l'ossido di zirconio (zirconia ) o il rilevamento paramagnetico per la misurazione dell'ossigeno. Ogni tecnologia ha i suoi vantaggi e svantaggi, quindi è importante scegliere quella più adatta alla propria applicazione specifica.
Durante questa fase iniziale di selezione, i principali fattori da prendere in considerazione saranno :
COMPONENTI DA MISURARE
SCALE DI MISURA
COMPONENTI INTERFERENTI
Quest'ultimo fattore è importante quanto gli altri, poiché l'impatto delle interferenze incrociate può disturbare e degradare la misurazione.
Il secondo punto chiave da considerare è la scelta tra soluzioni di analisi dei gas in situ o estrattive.
Gli analizzatori di gas in situ sono installati direttamente nel flusso di processo e misurano la concentrazione dei gas, dove si trovano, al momento t, senza spostarli o denaturarli. Di conseguenza, offrono tempi di risposta migliori. Il più delle volte sono più compatti e consumano meno energia, non richiedono la preparazione del gas prima dell'analisi.
Gli analizzatori di gas estrattivi prelevano un campione del gas di processo e lo analizzano al di fuori del processo, a distanze variabili. I tempi di risposta sono più lunghi ed è necessario un sistema per prelevare ed elaborare il campione. Come si può notare, entrambi i metodi presentano vantaggi e svantaggi e la scelta migliore dipende in larga misura dall'applicazione.
Il terzo punto chiave da tenere in considerazione quando si progettano soluzioni per l'analisi dei gas è la progettazione dei sistemi di campionamento, noti anche come sistemi di campionamento o di trattamento o condizionamento dei campioni.
Il gas campione deve essere rappresentativo del gas di processo e non deve contenere contaminanti solidi, liquidi o gassosi che possano danneggiare il sensore. Il gas campione deve inoltre essere fornito al sensore a una portata e a una pressione definite e costanti. A seconda dell'applicazione e della tecnologia di rilevamento, possono essere necessari diversi tipi di sistemi di campionamento.
La maggior parte degli analizzatori IR, ad esempio, funziona a temperatura ambiente. Infatti, i gas devono essere prima essiccati in modo da non condensare nella cella dell'analizzatore. Al contrario, un analizzatore dotato di una cella riscaldata e che misura i composti solubili, accoglierà gas mantenuti caldi, ma preventivamente filtrati.
L'analizzatore industriale deve essere progettato per funzionare e resistere alle sollecitazioni delle condizioni ambientali, comprese le alte temperature, le pressioni e le vibrazioni.
Ecco le principali domande da porre in questa fase:
ALL'INTERNO O AL COPERTO
SCATOLA O CABINA
IP E/O ATEX
UTENZE DISPONIBILI
La funzione di un analizzatore industriale è quella di determinare la concentrazione di gas dei composti in un processo industriale. Ma lo scopo delle soluzioni di analisi dei gas è quello di informare l'utente, o addirittura di consentire la regolazione del processo.
Nel caso di un sistema di misurazione continua delle emissioni (CEMS), il sistema di analisi sarà dotato di automazione industriale e di un sistema di acquisizione ed elaborazione dati (DAHS). Si tratta di un'interfaccia specifica e complessa, conforme a norme come la EN14181 per i CEMS e la EN17255 per i DAHS.
Nel caso dei sistemi di analisi utilizzati per controllare i processi industriali, come il controllo della combustione o un forno per il trattamento termico, i dati di misura e alcune informazioni di stato (scale, allarmi, ecc.) vengono trasmessi al sistema di controllo tramite segnali analogici (4-20mA, contatti a relè, ecc.) o trasmissione digitale(Modbus, Profibus, ecc.).
A seconda delle esigenze dell'utente, è possibile utilizzare come interfaccia diversi dispositivi come un PC, un touch screen HMI industriale, uno smartphone o un tablet.
Il sesto e ultimo punto chiave da considerare è la garanzia della durata e delle prestazioni delle soluzioni di analisi dei gas. Il sistema di analisi dei gas deve essere in grado di resistere ai rigori dell'uso industriale e mantenere la sua precisione nel tempo.
Per mantenere un analizzatore di gas accurato nel tempo, ci sono tre elementi fondamentali da considerare in fase di progettazione:
È necessario integrare un dispositivo di calibrazione nel sistema di campionamento. Che il sistema di analisi dei gas sia dotato di un dispositivo dicalibrazione manuale o di un sistema di calibrazione automatica, è indispensabile che quest'ultimo sia facile da usare. Inoltre, deve essere adattato alle frequenze di calibrazione richieste sia dalla tecnologia di rilevamento sia dalle esigenze dell'operatore per garantire l'accuratezza delle misure dell'analizzatore di gas.
I materiali di consumo, come guarnizioni, filtri e valvole della pompa, devono essere accessibili per facilitare e incoraggiare la manutenzione regolare. Gli operatori possono essere addestrati a queste operazioni di manutenzione, oppure la manutenzione può essere esternalizzata.
I materiali utilizzati per tutti i sistemi di analisi dei gas, sia all'interno degli analizzatori stessi che nei sistemi di campionamento, devono essere adatti alle condizioni del gas campione. Devono essere robusti e inerti, in modo da resistere soprattutto all'umidità e alla corrosione. In questo modo non solo si evitano danni all'apparecchiatura analitica, ma si denaturano anche i gas da analizzare prima ancora che vengano analizzati.
Quando si progettano soluzioni di analisi dei gas per un ambiente industriale, questi sono sei punti chiave da considerare. Prendendo in considerazione tutti questi fattori, è possibile scegliere o sviluppare un sistema di analisi industriale che soddisfi le esigenze della vostra applicazione e fornisca anni di servizio affidabile.
L'80% dei problemi riscontrati nell'utilizzo degli analizzatori di gas non sono dovuti all'analizzatore stesso, ma al sistema in cui è integrato. Fuji Electric produce analizzatori dal... 1954 (!), oltre a progettare, integrare e produrre il sistema di analisi completo adattato al processo industriale dell'utente. Grazie a questa duplice competenza, le soluzioni Fuji Electric per l'analisi dei gas sono note in tutto il mondo per essere tra le più affidabili ed efficienti del mercato.