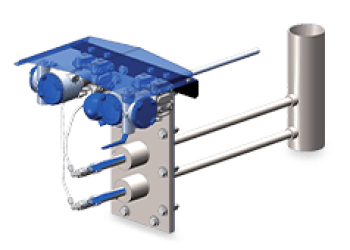
La produzione di cemento è un processo complesso, che richiede rigore e precisione per ottenere prodotti di qualità eccellente e conformi agli standard ambientali. Il controllo del processo della cementeria con strumenti affidabili per la misurazione della pressione, della portata e della temperatura contribuisce ad aumentare la produzione e a prolungare la durata degli impianti. Anche gli analizzatori di gas consentono un migliore controllo del processo, monitorando le emissioni atmosferiche.
Gli strumenti di misura Fuji Electric supportano i produttori di cemento in ogni fase del processo produttivo, al fine di :
Controllo qualità del cemento
Produzione rispettosa dell'ambiente
Gestione delle emissioni di CO2
Efficienza energetica
Il cemento è un legante idraulico essenziale utilizzato nelle costruzioni, ottenuto da clinker macinato. Il clinker si ottiene dalla cottura di una miscela di calcare e argilla a temperature molto elevate. La fabbricazione del cemento è un processo complesso che inizia con la macinazione delle materie prime, seguita dalla loro cottura in un forno rotante a temperature che possono raggiungere i 1.450 °C. Questo processo chimico trasforma la miscela in clinker, che viene poi macinato finemente per produrre il cemento. Utilizzato per legare tra loro le particelle di cemento e malta, il cemento è indispensabile per la costruzione di edifici, ponti, strade e altre infrastrutture.
Il mulino a farina cruda viene utilizzato per macinare le materie prime del cemento: calcare, argilla, pietra silicea, ossido di ferro, gesso e sabbia. Questi materiali vengono pre-misurati e poi mescolati nel mulino. La fase di macinazione è anche l'occasione per aggiungere scorie di altoforno provenienti da acciaierie. Anche le ceneri degli impianti di incenerimento dei rifiuti vengono utilizzate come materiale alternativo al cemento. Le materie prime vengono poi essiccate con gas caldi. Solo i materiali sufficientemente fini possono passare attraverso il separatore e passare al processo successivo. La polvere fine ottenuta è nota come farina grezza.
Il filtro elettrostatico viene utilizzato per rimuovere le particelle nocive dal gas. Rimuove le particelle fini, come polvere e fumo, dal gas che scorre, utilizzando la forza di una carica elettrostatica indotta, senza impedire il flusso di gas attraverso l'unità. Poiché i filtri elettrostatici creano poche perdite di carico e sono espandibili, sono ampiamente utilizzati nelle grandi caldaie e nei cementifici. Possono trattare gas superiori a 350°C e gas molto umidi. Agisce come filtro finale, rimuovendo particelle di dimensioni fino a 0,05 µm.
L'altezza e le dimensioni del camino industriale dipendono dalle sostanze emesse, dalle condizioni meteorologiche e geografiche locali e dagli edifici vicini. Soffiate da un ventilatore e poi rilasciate nell'atmosfera attraverso un camino, le emissioni di gas di combustione e degli inquinanti associati devono essere monitorate e misurate in conformità alle normative vigenti.
La farina deve essere preriscaldata prima di essere introdotta nel forno rotativo. Viene introdotta negli scambiatori di calore allineati verticalmente del preriscaldatore. La farina grezza scende lungo i cicloni in controcorrente rispetto ai gas caldi. Quando la miscela grezza scende nelle vasche del preriscaldatore, viene riscaldata a una temperatura compresa tra 800°C e 900°C utilizzando il calore estratto dal forno rotativo. In questo processo, si verifica una reazione chimica nella farina grezza, migliorando l'efficienza del processo di calcinazione. Questo preriscaldamento è necessario per ottenere le prestazioni principali del cemento.
Il calore emesso dal preriscaldatore viene reindirizzato alla caldaia, che fornisce energia al resto degli impianti. Caldaia a tubi d'acqua: due fusti sono disposti in alto e in basso, collegati tra loro da una serie di tubi d'acqua, attraverso i quali circola l'acqua. I tubi sono riscaldati dai gas di combustione per generare vapore.
Il forno rotativo è un tubo rivestito di mattoni refrattari (largo 3-5 metri e lungo 30-60 metri) che ruota circa 3-5 volte al minuto e la materia prima passa attraverso zone progressivamente più calde del forno verso la fiamma. La farina grezza viene riscaldata a 1450°C in rotazione. Viene poi raffreddata con aria fredda per formare il clinker di cemento. L'aria calda del raffreddatore viene restituita al preriscaldatore per risparmiare combustibile ed energia. Il cemento o la calce dipendono dal processo di produzione e dalle temperature coinvolte.
Il clinker viene poi macinato molto finemente in un mulino a sfere con altri additivi (ceneri da centrali termiche, scorie d'altoforno o gesso) per ottenere diversi gradi di cemento. Il cemento viene poi stoccato prima della consegna.
L'analisi dei gas garantisce la qualità dell'aria nei cementifici. Le centrali termiche e i forni rotativi utilizzati nella produzione del cemento emettono gas a effetto serra, in particolare CO2, che contribuiscono al cambiamento climatico. L'analisi dei gas consente di misurare queste emissioni e di attuare strategie per ridurle. Ad esempio, i cementi a basso contenuto di carbonio vengono prodotti utilizzando materiali alternativi e processi produttivi più efficienti, riducendo così le emissioni di CO2. Questo approccio è essenziale per soddisfare gli standard ambientali e promuovere una produzione di cemento più sostenibile.
Scoprite come gli analizzatori di gas contribuiscono a ridurre gli inquinanti e a promuovere lo sviluppo di energia pulita per un ambiente sostenibile.
09 giugno 2024