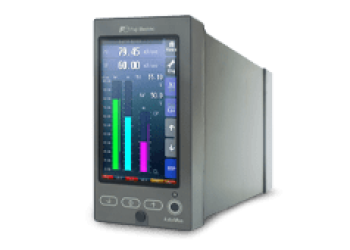
Controllore multifunzione - serie PSC100 - 2 loop
rif. : PSC100Da
2928,00 € Richiesta di preventivoLa questione delle prestazioni energetiche nelle industrie metallurgiche, siderurgiche e di fonderia è fondamentale per il successo della transizione energetica del settore. Una serie di strumenti di misura e analisi appropriati(analisi dei gas, misurazione della pressione, misurazione del flusso, misurazione della temperatura, misurazione del livello) può essere messa in atto per ottenere risparmi energetici e ridurre le bollette energetiche e l'impronta di carbonio. Risparmiare e ottimizzare il consumo energetico di ogni processo è alla portata di ogni produttore.
Gli strumenti di misura Fuji Electric supportano le aziende di lavorazione dei metalli in ogni fase del loro processo produttivo per :
Controllo qualità del metallo
Conformità agli standard attuali
Efficienza energetica
Sicurezza del personale e delle strutture
Nel forno di sinterizzazione, le polveri di materie prime (minerali, calcare e acqua) sono sottoposte al calore per produrre un pezzo compatto.
I pezzi passano attraverso il forno a diverse temperature, poi vengono raffreddati e infine calibrati per ottenere la forma desiderata.
In questo processo, è necessario controllare la temperatura all'interno del forno e controllare il rapporto aria-combustibile e le emissioni nocive.
La cokeria converte il carbone in coke mediante un processo di distillazione a secco.
Il coke è un combustibile ottenuto dalla pirolisi del carbon fossile (a 1100°C) in una cokeria, al riparo dall'aria, per diverse ore.
Per ottimizzare questo processo, il controllo della combustione e il monitoraggio dei gas di scarico sono essenziali.
La torre di raffreddamento, o sistema di raffreddamento del coke secco (CDQ), raffredda il coke incandescente a una temperatura adatta al trasporto. Si tratta di un sistema di recupero energetico. Durante il processo di aspersione dell'acqua, il calore emesso dal coke incandescente viene recuperato e utilizzato per produrre elettricità o vapore.
È necessario monitorare i gas, CO eH2, per evitare esplosioni durante il quenching.
L'altoforno trasforma il minerale di ferro agglomerato in ghisa liquida. Il minerale di ferro e il coke vengono caricati dall'alto. L'aria calda (1250°C), soffiata nella base dell'altoforno, reagisce con il coke e il carbone polverizzato per formare un gas riducente che assorbe l'ossigeno dal minerale di ferro. Allo stesso tempo, si crea il calore necessario per la fusione dei minerali ridotti. Durante questo processo si generano grandi quantità di gas (CO eCO2).
Per ottenere le migliori prestazioni dall'altoforno, è necessario controllare la qualità della ghisa, controllare la combustione del forno e monitorare le emissioni di gas.
La ghisa viene versata nel convertitore, che contiene rottami metallici. L'ossigeno puro viene soffiato sul bagno di metallo per bruciare il carbonio in eccesso e le impurità. Il risultato è un acciaio liquido noto come "acciaio selvaggio". Non è necessario generare calore aggiuntivo, poiché il calore generato durante l'ossidazione viene soffiato nel convertitore. I gas di combustione prodotti nel convertitore vengono riutilizzati per generare elettricità o per il riscaldamento nel processo di laminazione.
Per ottenere una trasformazione ottimale della ghisa in acciaio liquido, è necessario monitorare il processo di decarburazione e la quantità di ossigeno insufflata.
I degasatori sottovuoto sono installati in molti altiforni e acciaierie per migliorare la purezza dell'acciaio . Il degasaggio è un processo metallurgico che prevede l'aggiunta di una quantità di alluminio prima dell'acciaio, quindi l'iniezione di argon nell'acciaio fuso per ridurre il contenuto diH2,02 e N2 ed eliminare alcune inclusioni non metalliche.
L'acciaio fuso decarburatosi nel convertitore viene iniettato in una siviera e trasportato all'impianto di colata continua per la colata (bramme, billette o blumi).
Il gas argon viene versato nella siviera per prevenire l'ossidazione dell'acciaio fuso.
Il monitoraggio dell'ossigeno è necessario per garantire l'assenza di ossigeno all'interno della siviera.
Le bramme di acciaio vengono riscaldate nel forno di riscaldo (da 800°C a 1000°C) in modo da diventare sufficientemente morbide per la laminazione.
Il controllo della combustione è necessario per portare il metallo a una temperatura che consenta di trasformarlo in condizioni ottimali di qualità, produttività ed efficienza energetica, riducendo al contempo le emissioni inquinanti.
La lastra viene riscaldata in un forno a 1200°C per rendere il metallo più malleabile. Viene quindi assottigliata e allungata mediante schiacciamento progressivo tra i cilindri del laminatoio. Il nastro d'acciaio viene trasformato in rotoli o lamiere di spessore compreso tra 1,2 e 20 millimetri. I coils subiscono poi una seconda riduzione a freddo per ottenere un prodotto sottile come un foglio di carta (fino a 0,1 millimetri di spessore).
Durante questi processi, i componenti gassosi legati al potenziale di carbonio(CO2, CO, CH4, NH3,H2 o O2) devono essere monitorati e controllati.
Scoprite come gli analizzatori di gas contribuiscono a ridurre gli inquinanti e a promuovere lo sviluppo di energia pulita per un ambiente sostenibile.
09 giugno 2024