Guide d’achat des capteurs de pression
Les capteurs de pression sont indispensables dans diverses applications industrielles et technologiques.
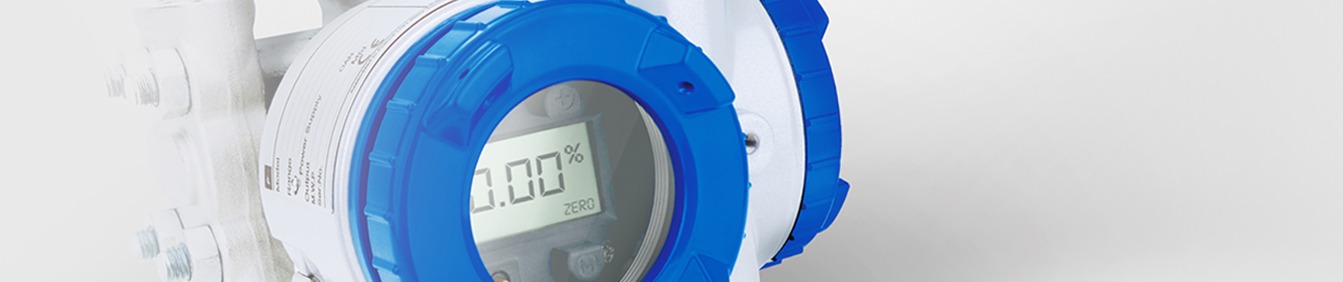
Depuis l’origine et l’unité de mesure de la pression jusqu’aux avantages et inconvénients des différents types de capteurs, vous découvrirez ce qu’est un capteur de pression, le principe de son fonctionnement, et comment un capteur de pression opère.
Nous détaillerons également la composition d’un capteur de pression, les types de signaux de sortie, et les critères essentiels pour choisir un capteur de pression industriel. En explorant les différentes catégories de capteurs de pression – capteur de pression différentielle, capteur de pression absolue ou capteur de pression relative – nous vous guiderons sur la manière de les étalonner, installer et tester efficacement.
Enfin, nous aborderons la configuration du transmetteur de pression et les applications pratiques de cet instrument de terrain essentiel, tout en pesant ces avantages et inconvénients.

- Unité de mesure de pression
- Qu’est-ce qu’un capteur de pression ?
- Quel est le principe d’un capteur de pression ?
- Comment fonctionne un transmetteur de pression ?
- Construction d’un capteur de pression ?
- Quel est le signal de sortie d’un capteur de pression ?
- Comment choisir un capteur de pression industriel ?
- Pression différentielle, absolue ou relative : les différents types de capteurs de pression ?
- Comment étalonner un capteur de pression ?
- Comment installer un capteur de pression industriel ?
- Comment tester un capteur de pression ?
- Comment configurer un capteur de pression ?
- Quelles sont les applications des capteurs de pression ?
- Quels sont les avantages et inconvénients des capteurs de pression ?
Origine de la mesure de pression
L’unité de mesure Pascal tire son origine du renommé philosophe, physicien et mathématicien français Blaise Pascal.
Né à Clermont-Ferrand où se situe le siège de l’unité de production de Fuji Electric France SAS, fabricant français de capteurs de pression industriels, Pascal réalisa une expérience fondamentale en transportant un baromètre au sommet du Puy de Dôme, afin de prouver que la pression atmosphérique diminuait avec l’altitude par rapport au niveau de la mer.
Cependant, le scientifique italien Evangelista Torricelli fut le pionnier dans la mise en évidence de la pression exercée par le poids du volume d’air sur la terre et conçut le premier baromètre à base de mercure.
Unité de mesure de pression
La pression p est exprimée en unités de force F par unités de surface A : p = F / A
Connaître les unités de pression et leur conversion est important pour faire les bons choix des échelles de votre capteur de pression industriel.
- Le Pascal (Pa) : c’est l’unité de base du Système international (SI) pour la pression. Un Pascal correspond à 1 Newton par mètre carré (1 Pa = 1 N/m²).
- Le Bar (Bar) : c’est une unité de pression couramment utilisée dans les applications industrielles. Un Bar correspond à une pression de 100 000 Pa.
- L’atmosphère standard (atm) : elle est utilisée pour exprimer la pression barométrique ou atmosphérique. Une atmosphère correspond à une pression de 101 325 Pa.
Qu’est-ce qu’un capteur de pression ?
Le capteur de pression est appelé aussi transmetteur de pression, sonde de pression, jauge de pression ou bien transducteur de pression. Il n’existe pas de différence notable entre ces différentes appellations. On distingue cependant les capteurs de pression analogique et les transmetteurs de process intelligent.
Si on se réfère à la définition d’un capteur de pression, c’est un appareil de détection de la pression dont le principe consiste à convertir la force appliquée par la pression d’un fluide sur une surface donnée (déformation) en un signal électrique.
Les entreprises industrielles utilisent un transmetteur de pression pour :
- Mesurer une pression avec un capteur de pression relatif ou absolue.
- Mesurer un débit avec un organe déprimogène et un capteur de pression différentielle
- Mesurer un niveau par capteur de pression hydrostatique
- Mesurer une densité avec un transmetteur de pression différentielle
Quel est le principe d’un capteur de pression ?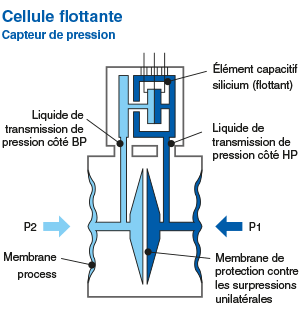
La pression du fluide mesuré est appliquée sur un composant de mesure interne à travers un raccord puis une interface mécanique – membrane de mesure en acier inoxydable, céramique ou un autre matériau noble.
L’élément de mesure électronique convertit la pression en un signal de sortie brut.
Comment fonctionne un transmetteur de pression ?
Il existe différentes technologies, méthodes, techniques et principes de mesure pour les modèles de capteurs de pression, chacun adapté à des applications spécifiques dans les domaines de l’automatisation des process et des installations industrielles.
Le capteur de pression piézorésistif mesure la force appliquée sur une membrane métallique. La contrainte exercée sur une fine pellicule provoque sa déformation, transmettant la variation de pression par l’intermédiaire d’un fluide incompressible (huile ou eau). Celui-ci vient déformer un élément silicium piézorésistif (circuit en pont de Wheatstone). Ce composant, utilisant des semi-conducteurs, est une résistance électrique variable qui convertit la déformation en valeur ohmique. Les MEMS (Micro-Electro-Mechanical Systems) sont également utilisés dans certains de ces capteurs, offrant une miniaturisation et une plus grande sensibilité.
- Le capteur de pression capacitif mesure la force appliquée sur une membrane métallique en acier inoxydable ou céramique. La pression exercée déforme la pellicule métallique qui transmet la variation de pression via un fluide incompressible intermédiaire (huile ou eau). Celui-ci vient déformer un élément silicium capacitif. Ce composant est un condensateur variable qui convertit la déformation en valeur capacitive.
- Le transmetteur à résonance de fréquence utilise des termes spécifiques tels que BFSL (Best Fit Straight Line) pour définir la linéarité de la mesure. Ce capteur de pression convertit la variation de pression en un changement de fréquence d’oscillation, offrant ainsi une haute résolution et une variété de solutions pour diverses applications.
- Le capteur de pression à jauges de contrainte ou jauges de tension fonctionne de manière similaire, où le signal de sortie du détecteur est ensuite filtré, amplifié, compensé en température puis formaté en un signal analogique. La sortie analogique est transmise via un connecteur électrique, réduisant ainsi les erreurs et améliorant la précision.
- Les manomètres, quant à eux, disposent d’un affichage locale de la mesure de pression. Les manomètres à tube en U, par exemple, sont souvent utilisés pour des mesures simples et directes.
Construction du capteur de pression
La construction d’un transmetteur de pression comprend plusieurs éléments essentiels :
- un raccord mécanique pour le montage,
- une membrane métallique ou céramique,
- un élément sensible capacitif ou détecteur piézorésistif,
- un fluide de remplissage, souvent de l’huile, intégré dans les cellules de mesure de pression pour transmettre les variations de pression,
- module électronique de conditionnement et d’amplification du signal du détecteur,
- un connecteur électrique, permettant une connexion facile à d’autres systèmes d’automatisation,
- un boîtier plastique ou métallique (aluminium, inox acier inoxydable),
- un indicateur digital (en option) pour un affichage des informations de pression en temps réel.

Quel est le signal de sortie d’un capteur de pression industriel ?
Le signal d’une sonde de pression peut être de type analogique ou numérique. Le signal analogique du capteur de pression est usuellement de type sortie courant 4-20mA, sortie tension 0-10V ou sortie tension 1-5V. Le signal de sortie est envoyé vers l’organe de commande afin d’agir sur l’organe de commande.
Le signal de sortie analogique 4-20mA est couramment utilisée par ces appareils en raison de plusieurs avantages qu’il présente.
Tout d’abord, le capteur de pression 4-20 mA est résistant à la perte de signal due à la ligne de transmission, ce qui garantit une mesure précise.
De plus, il permet d’étendre la distance entre le capteur de pression et le système concerné. En outre, l’absence de courant permet de détecter les défauts de ligne, ce qui facilite le dépannage. Le transmetteur de pression 4-20mA 2 fils ou 4 fils est également moins sensible aux perturbations électromagnétiques, ce qui garantit sa fiabilité.
Enfin, il peut être utilisé dans une boucle 4-20mA pour alimenter plusieurs équipements tels que l’afficheur, le régulateur et l’enregistreur.
Une communication numérique peut être disponible avec différents protocoles de communication – HART – Fieldbus – Profibus – Modbus. Ces protocoles de communication transmettent la valeur de mesure et permettent aussi de configurer les appareils de mesure de la pression. On parle de transmetteur électronique intelligent ou SMART. Certains capteurs de pression électroniques offrent également des interfaces IO Link, une gamme de précisions et d’étendues de mesure spécifiques, ainsi que des homologations internationales.
Comment choisir un capteur de pression industriel ?
Le transmetteur de pression industriel doit être choisi en fonction du fluide à mesurer, de la plage de pression et des conditions de service de l’application et du process.
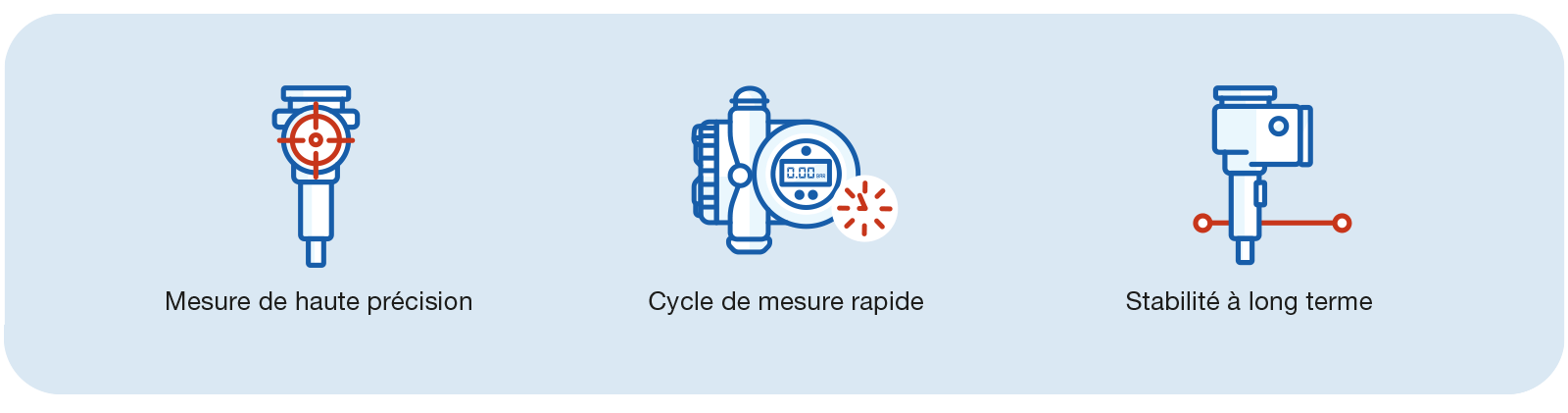
Les propriétés du fluide à mesurer tel que : capteur de pression air, capteur de pression gaz, capteur de pression hydrogène, capteur de pression vapeur, capteur de pression eau ou un autre liquide ainsi que ses caractéristiques (densité, viscosité, corrosivité…)
- Les conditions de service du processus : la pression à mesurer, la pression statique, la température du process, le risque de corrosion
- Le type de mesure : mesure de pression, mesure de débit par organe déprimogène et pression différentielle delta-p, mesure de niveau par pression hydrostatique, mesure de densité
- Le type de pression à mesurer :
- Pression relative
- Pression atmosphérique
- Pression absolue
- Pression différentielle
- Pression barométrique
- La plage de pression ou étendue de mesure
- La dynamique ou rangeabilité
- La précision de la mesure de pression
- Le temps de réponse
- L’interface mécanique de montage ou raccord de connexion process : raccordement vissé, raccordement à brides
- Le signal de sortie analogique et/ou communication numérique avec ou sans fil
- L’environnement climatique et les contraintes associées :
- L’environnement industriel, les contraintes associées, la réglementation en vigueur :
La sécurité fonctionnelle et le niveau d’intégrité de sécurité (SIL) ; norme CEI 61508 et norme CEI 61511 qui nécessitent des transmetteurs de pression avec fonctions de sécurité avancées SIL2/SIL3.
Le choix d’une sonde de pression avec le bon niveau de sécurité et le choix du capteur le plus sûr en zone explosive sont essentiels pour la sécurité et la longévité de votre process.
- La pression d’éclatement doit être prise en compte lors du dimensionnement des capteurs de pression. La pression d’éclatement correspond à la limite de sollicitation mécanique du boîtier, et lorsque celle-ci dépasse ce seuil, le boîtier est détruit, ce qui peut causer une fuite de fluide. Maintenir la pression dans la plage spécifiée garantit des mesures fiables conformes aux indications de la fiche technique.
- Les accessoires pour capteur de pression associés tels qu’un manifold ou un presse-étoupe.
Pression différentielle, absolue ou relative : les différents types de capteurs de pression ?
Le transmetteur de pression relative permet la mesure de pression relative du processus par rapport à la pression atmosphérique. La pression atmosphérique est mesurée en utilisant une cavité de référence à l’intérieur du transmetteur. Cette pression diminue au fur et à mesure que l’on s’élève en altitude.
Le capteur de pression différentielle utilise deux chambres séparées reliées par une membrane souple. La pression est mesurée de chaque côté de la membrane. La pression différentielle (dp) est la différence de pression entre ces deux pressions : une pression de référence coté basse pression (BP ou LP) et une pression coté haute pression (HP). Cet appareil de mesure de pression différentielle est utilisé pour la mesure de débit des fluides dans les tuyauteries, la surveillance des encrassements des filtres ou le calcul des pertes de charge.
Le capteur de pression absolue compare la pression relative par rapport au vide absolue. La pression absolue est toujours positive. Le fonctionnement de cet appareil a pour avantage de s’affranchir des variations de la pression atmosphérique grâce à une chambre de référence au vide et d’obtenir ainsi une meilleure exactitude.
On exprime la pression absolue à partir de la pression relative en ajoutant 1,013 bar soit p. absolue (bar abs.) = p. relative (bar) + 1,013.
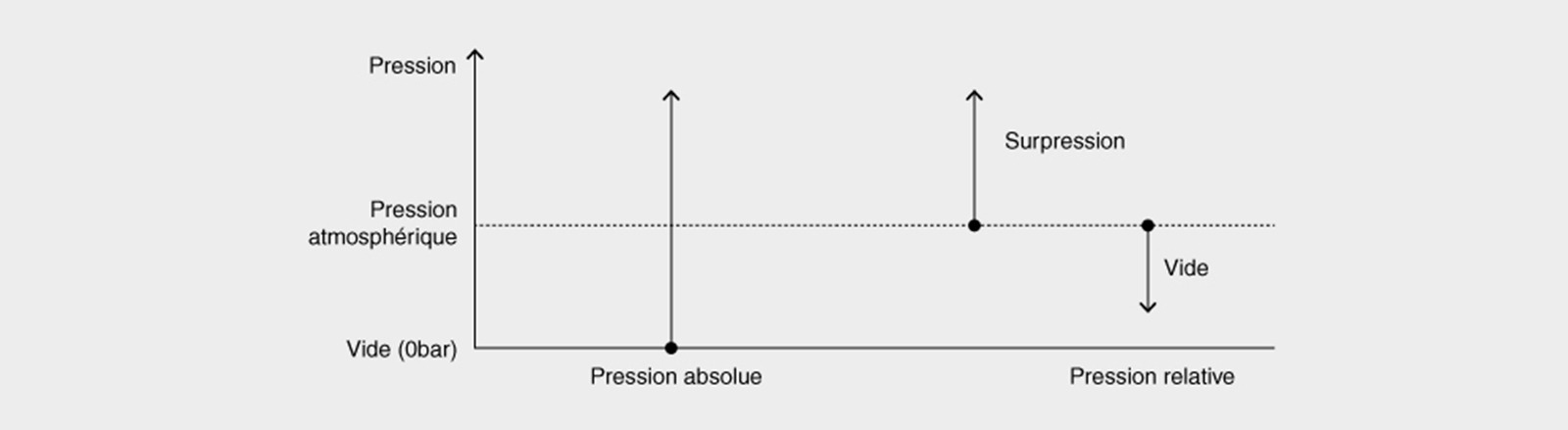
Un transmetteur de pression à séparateur à membrane sépare le fluide du procédé mesuré de la cellule de pression. La membrane et les pièces de contact sont faites d’un matériau résistant au fluide mesuré et sont soudées à la base de la cellule de mesure de la pression.
Un tube capillaire ou un manchon de raccordement assure la liaison entre la membrane séparatrice et la cellule de pression. Cet espace doit être dégazé sous vide, puis rempli d’une huile de remplissage et scellé. La pression mesurée exerce une force sur la surface extérieure de la membrane. Lorsque la membrane fléchit vers l’intérieur, elle tente de comprimer le fluide de remplissage à l’intérieur de l’instrument.
Ce liquide de remplissage est conçu pour résister à la compression, de sorte que la force est canalisée directement vers la cellule de mesure de la pression. L’ensemble du fonctionnement d’un capteur de pression à membrane est basé sur le principe de Blaise Pascal.
Le capteur de pression à diaphragme est fabriqué à partir de différents matériaux tels que l’acier inoxydable, le titane, l’Inconel, le Hastelloy, le Monel, le Tantale, la céramique et le Nickel. Les matériaux utilisés dépendent du type d’application et de la température pour lequel le capteur de pression industriel est conçu.
Le capteur de pression avec séparateurs est utilisé pour mesurer les pressions des fluides dans une gamme de haute température.
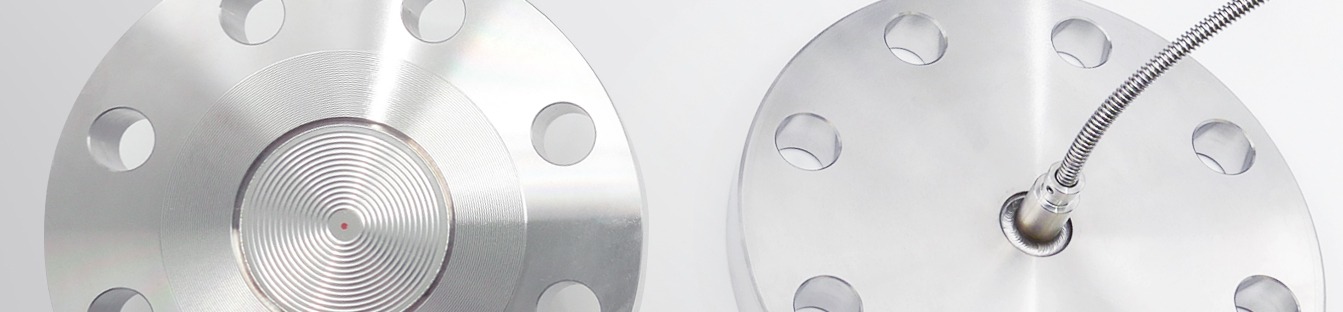
- Le capteur de pression multivariable
Le transmetteur de pression multivariable combine dans le même capteur une mesure de pression différentielle, une mesure de pression absolue et une mesure de température. Ces produits sont utilisés notamment pour la mesure de débit massique.
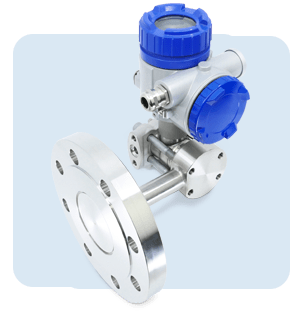
Le capteur de niveau hydrostatique est un dispositif de mesure qui permet de déterminer le niveau de remplissage d’un liquide dans des réservoirs ou des cuves. Le principe de mesure est basé sur la pression hydrostatique, qui est le poids exercé par un liquide en fonction de la hauteur de la colonne de remplissage.
- Le capteur de pression immergé
Cette sonde de pression submersible ou hydrostatique peut être immergée dans un liquide et permet de mesurer le niveau d’une cuve ou d’un réservoir. Le capteur de pression immergé est généralement pourvue d’une membrane en acier inoxydable.
Comment étalonner un capteur de pression ?
Les transmetteurs de pression industriels nécessitent un étalonnage périodique pour assurer une métrologie industrielle précise au long de leur cycle de vie et éviter les facteurs qui influencent la précision de vos capteurs.
La période de calibration est définie par les fabricants de capteurs de pression. Il convient d’étalonner le zéro (Zéro) et la pleine échelle (Span).
En usine, afin de vérifier la linéarité du signal de sortie, on vérifie la précision sur plusieurs points de la plage de pression.
La calibration consiste à appliquer une pression de référence définie sur l’interface mécanique du capteur, de vérifier le signal de sortie 4-20 mA puis d’appliquer une compensation. Le capteur peut être calibré à l’aide d’une vis de réglage externe ou d’une interface de programmation ou d’un logiciel de programmation. Pour les modèles de capteur de pression avec afficheur et boutons poussoirs, il est possible de les étalonner localement.
Afin de procéder aux différentes manipulations, il peut être nécessaire de disposer de robinet d’isolement ou de manifold monté sur le transmetteur de pression afin d’isoler celui-ci du process.
Pour vos calibrations annuelles, vous pouvez faire appel à une entreprise spécialisée dans l’étalonnage des capteurs de pression.
L’étalonnage du capteur de pression régulier vous permet de garantir la précision de la mesure de pression pour garantir des résultats constants.
Comment installer une mesure de pression ?
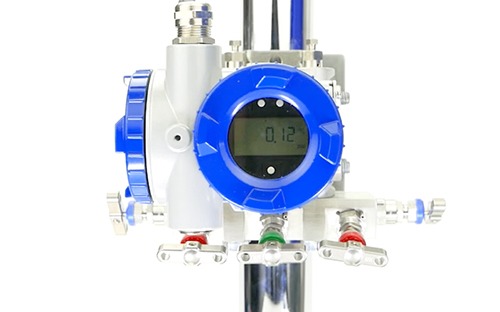
Les capteurs de pression peuvent être fixés grâce à un raccord mécanique sur l’organe de mesure ou sur la tuyauterie où la pression est à mesurer.
Des précautions de montage particulières doivent être prises en fonction des conditions de pression et de température du process.
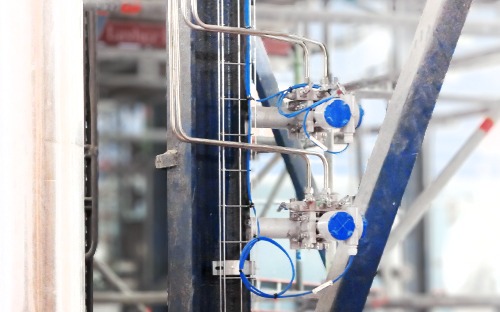
Le signal de sortie 4-20 mA de cet appareil peut être raccordé à un système d’affichage (un afficheur numérique industriel, un enregistreur, un régulateur, ou une supervision) ou à un automate (système d’automatisation pour mesure de la pression) afin de contrôler un organe de contrôle et réguler la pression d’un process.
Vérifier le schéma éléctrique du capteur de pression avant le cablâge de l’instrument de terrain pour votre sécurité.
Si vous avez besoin d’aide, il est recommandé de faire appel à une entreprise professionnelle pour l’installation et la mise en service de votre instrument de mesure.
Comment tester un capteur de pression ?
Un capteur de pression 4-20 mA peut être testé en appliquant une pression connue définie sur l’interface mécanique de la sonde de pression et en vérifiant le signal de la sortie analogique mesuré. Si vous disposez d’un capteur de pression avec affichage, vérifiez la valeur affichée sur l’indicateur.
Si votre instrument est défectueux vous pouvez demander la réparation de votre instrument à un spécialiste ou un des fabricants de capteurs industriels.
Si la réparation n’est pas possible, vous pouvez remplacer votre ancienne référence de capteur de pression par un nouveau modèle plus moderne.
Comment configurer un capteur de pression ?
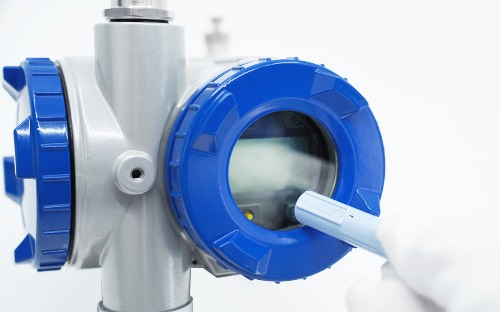
La configuration des transmetteurs numériques intelligents avec protocole HART peut être opérée :
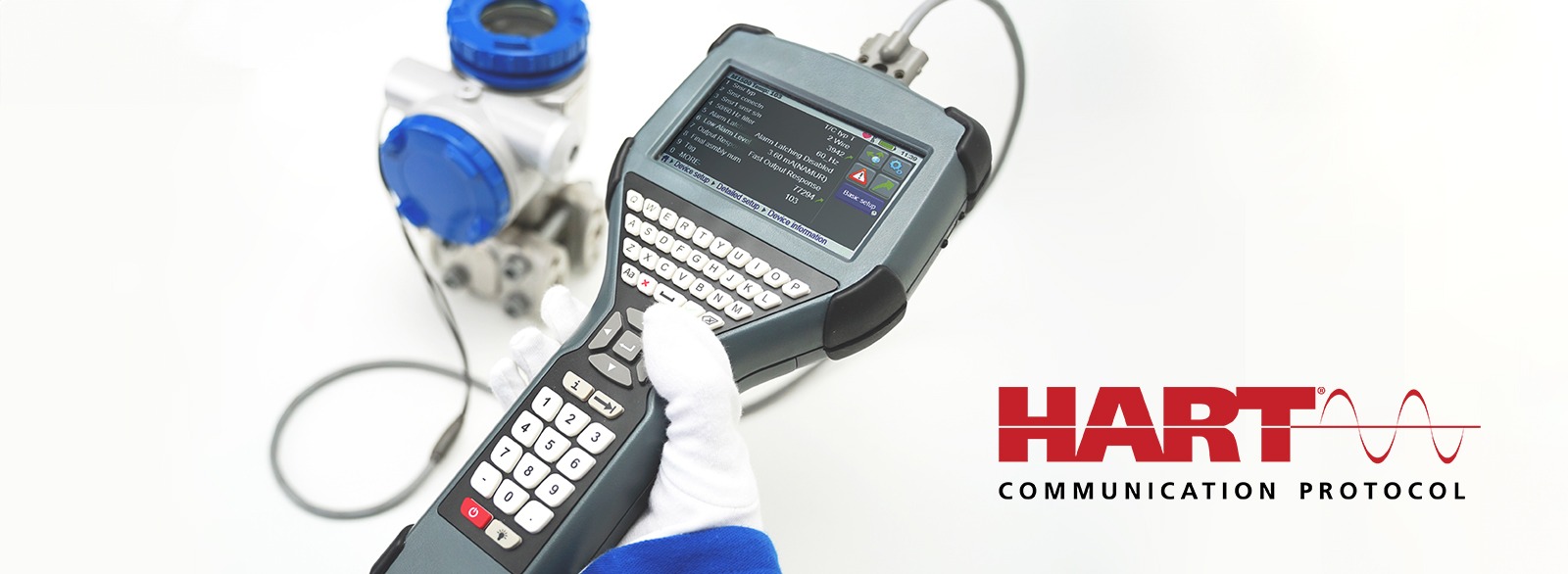
Quelles sont les applications des capteurs de pression ?
Comprendre pourquoi mesurer la pression dans les industries de process est important pour garantir la sécurité, optimiser le contrôle des processus, améliorer l’efficacité énergétique et maintenir la qualité des produits finis.
Le transmetteur de pression est utilisé dans de nombreuses applications du secteur industriel.
Ce capteur de pression digital peut détecter des pressions allant de quelques millibars à plusieurs centaines de bars. Il est donc essentiel dans un large spectre d’industries pour l’automatisation des lignes de production et des machines.
Les pressions relatives ou absolues d’air comprimé, les pressions d’eau, les pressions de vapeur, les pressions de gaz peuvent ainsi être mesurées.
Par exemple, les applications comprennent la mesure par pression différentielle de débit des liquides, de débit de gaz ou du débit de vapeur dans une conduite, la surveillance des filtres, la mesure du niveau d’un liquide dans un réservoir avec un capteur de pression à membrane affleurante , la mesure de la densité d’un fluide.
Suivant votre industrie, il convient de choisir un instrument de mesure adapté en fonction de l’application et des contraintes du milieu industriel.
Quels sont les avantages et inconvénients
d’un capteur de pression ?
Avantages des capteurs de pression
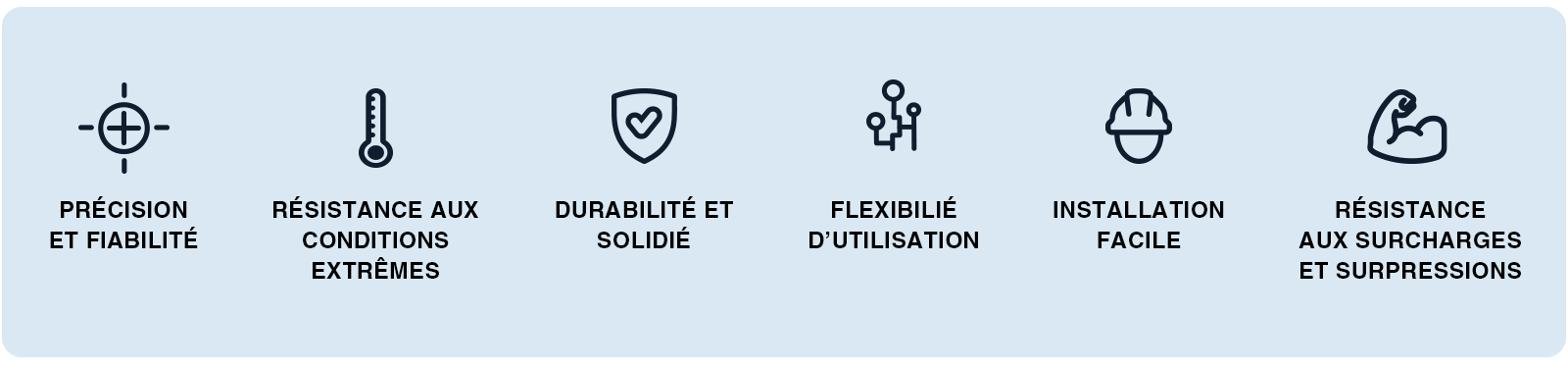
- Précision et fiabilité : Les capteurs de pression offrent des mesures extrêmement précises, essentielles pour des applications industrielles. Ils augmentent la productivité et réduisent les coûts en fournissant des informations précises sur la pression de gaz, de vapeur ou de liquides.
- Résistance aux conditions extrêmes : Même dans des conditions de hautes températures ou des environnements corrosifs, comme ceux rencontrés dans l’industrie chimique ou du pétrole et du gaz, leur fonctionnement est garanti avec une fiabilité et une précision exceptionnelles.
- Durabilité et solidité : Logés dans des boîtiers en acier inoxydable ou en aluminium, les capteurs de pression résistent aux chocs, aux vibrations, et aux environnements hostiles. Ils sont conçus pour durer.
- Flexibilité d’utilisation : Disponibles dans une variété de designs et de technologies, ces capteurs couvrent un large éventail de plages de mesure de pression pour tous les fluides, incluant les applications en vide et dépression. Leur flexibilité les rend adaptés à de nombreuses industries.
- Installation facile : Avec une grande variété de raccords et de connecteurs disponibles, les capteurs de pression peuvent être intégrés rapidement et facilement dans les systèmes d’automatisation, minimisant les erreurs d’installation.
- Résistance aux surcharges et surpressions : Grâce à leur haute résistance à la surcharge, les capteurs de pression peuvent supporter des pics de pression extrêmes, tels que ceux produits par des soupapes se fermant rapidement ou les coups de béliers de l’air comprimé.
Inconvénients des capteurs de pression
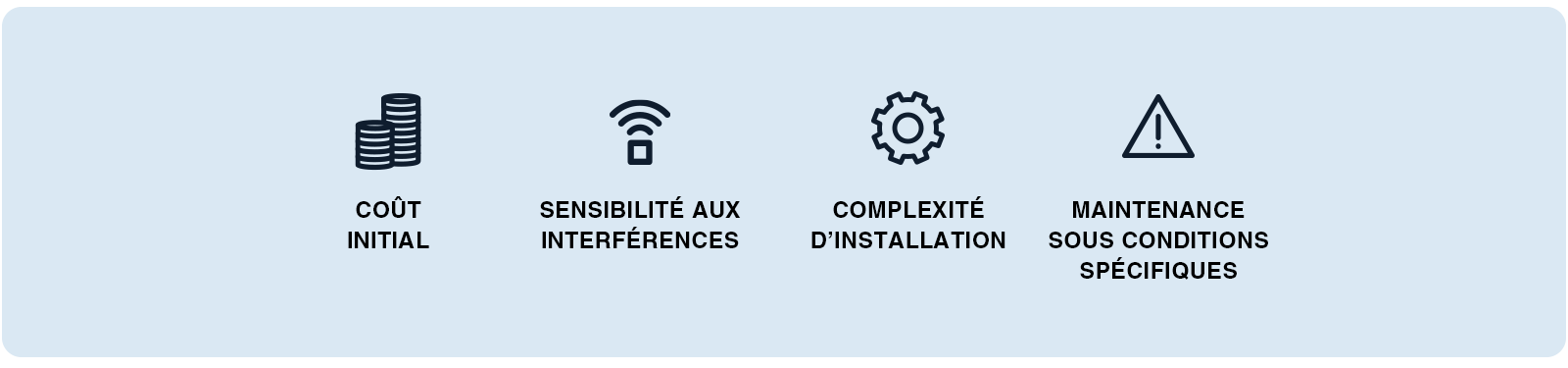
- Coût initial : Le coût d’acquisition de capteurs de pression de haute précision peut être élevé, ce qui peut représenter un investissement important pour certaines entreprises industrielles. Le prix d’un capteur de pression reflête souvent sa qualité et sa durabilité. Evitez les marques de capteurs de pression exotiques et orientez-vous vers un fabricant de capteur de pression français.
- Sensibilité aux interférences : Les capteurs utilisant des semi-conducteurs peuvent être sensibles aux interférences électromagnétiques, ce qui peut affecter leur précision. Optez pour un fabricant proposant des capteur de pression conformes aux normes CEM.
- Complexité d’installation : Bien que de nombreux capteurs soient conçus pour une installation facile, certaines applications complexes peuvent nécessiter des compétences techniques spécifiques pour garantir un fonctionnement optimal. Appuyez-vous sur un fabricant de capteur de pression de confiance.
- Maintenance sous conditions spécifiques : Dans certaines installations, particulièrement où les conditions environnementales sont extrêmes, une maintenance régulière de votre capteur de pression peut être nécessaire pour garantir la performance. Choississez un fabricant de capteur de pression avec un service de maintenance de proximité.
Mesurer la pression ne s’improvise pas !
La mesure de pression nécessite de faire appel à des professionnels du domaine du secteur de l’instrumentation.
Pour garantir le fonctionnement et les résultats attendus et éviter les erreurs dans la mesure de pression sur vos process, les experts de Fuji Electric, fabricant français de capteurs de pression industriels, vous guident et vous proposent des capteurs de pression conçus pour votre application la plus exigeante. Vous profiterez ainsi des avantages du capteur de pression sans en subir les inconvénients.
Les capteurs de pression Fuji Electric sont reconnus pour leur haute technologie, leur précision de mesure de pression, leur large plage de mesure, leur stabilité à long terme, leur qualité de fabrication, leur fiabilité, leur résistance, leur support technique, leur politique de retour facile et leur service de livraison rapide pour les clients.
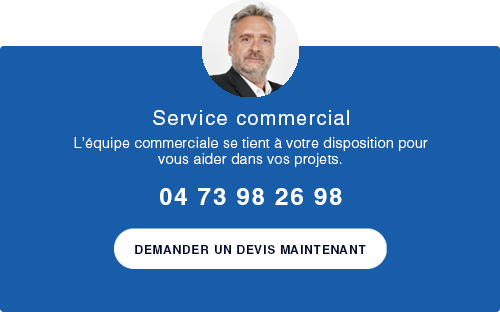