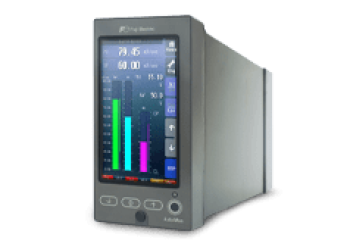
Controlador multifunções - série PSC100 - 2 circuitos
ref : PSC100De
2928,00 € Pedir um orçamentoA questão do desempenho energético nas indústrias metalúrgica, siderúrgica e de fundição é crucial para que o sector possa ter êxito na sua transição energética. É possível utilizar uma série de instrumentos de medição e de análise adequados(análise de gases, medição da pressão, medição do caudal, medição da temperatura, medição do nível) para realizar economias de energia e reduzir a fatura energética e a pegada de carbono. Poupar e otimizar o consumo de energia de cada processo está ao alcance de qualquer fabricante.
Os instrumentos de medição da Fuji Electric apoiam as empresas metalúrgicas em todas as fases do seu processo de fabrico, de modo a :
Controlo de qualidade dos metais
Conformidade com as normas actuais
Eficiência energética
Segurança do pessoal e das instalações
No forno de sinterização, os pós das matérias-primas (minérios, calcário e água) são submetidos ao calor para produzir uma peça compacta.
As peças passam pelo forno a diferentes temperaturas, depois são arrefecidas e finalmente calibradas para obter a forma desejada.
Neste processo, é necessário controlar a temperatura no interior do forno e controlar a relação ar-combustível e as emissões nocivas.
O forno de coque converte o carvão em coque através de um processo de destilação seca.
O coque é um combustível obtido através da pirólise de hulha (a 1100°C) num forno de coque, ao abrigo do ar, durante várias horas.
Para otimizar este processo, o controlo da combustão e a monitorização dos gases de escape são essenciais.
A torre de arrefecimento, ou sistema de arrefecimento de coque seco (CDQ), arrefece o coque incandescente até uma temperatura adequada para o transporte. Trata-se de um sistema de recuperação de energia. Durante o processo de aspersão de água, o calor emitido pelo coque incandescente é recuperado e utilizado para produzir eletricidade ou vapor.
É necessário controlar os gases, CO eH2, para evitar explosões durante o arrefecimento.
O alto-forno transforma o minério de ferro aglomerado em ferro fundido líquido. O minério de ferro e o coque são carregados por cima. O ar quente (1250°C), soprado para a base do alto-forno, reage com o coque e o carvão pulverizado para formar um gás redutor que absorve o oxigénio do minério de ferro. Simultaneamente, é criado o calor necessário para a fusão dos minérios reduzidos. Durante este processo, são geradas grandes quantidades de gases (CO eCO2).
Para obter o melhor desempenho do alto-forno, é necessário controlar a qualidade do ferro fundido, controlar a combustão do forno e monitorizar as emissões de gases.
O ferro fundido é vertido no conversor, que contém sucata metálica. O oxigénio puro é soprado sobre o banho de metal para queimar o excesso de carbono e as impurezas. O resultado é o aço líquido, conhecido como "aço selvagem". Não há necessidade de gerar calor adicional, uma vez que o calor gerado durante a oxidação é soprado para o conversor. Os gases de combustão produzidos no conversor são reutilizados para gerar eletricidade ou para aquecimento no processo de laminagem.
Para conseguir uma transformação óptima do ferro fundido em aço líquido, é necessário monitorizar o processo de descarbonetação e a quantidade de oxigénio insuflado.
Os desgaseificadores a vácuo são instalados em muitos altos-fornos e siderurgias para melhorar a pureza do aço . A desgaseificação é um processo metalúrgico que envolve a adição de uma quantidade de alumínio antes do aço e, em seguida, a injeção de árgon no aço fundido para reduzir o teor deH2,02 e N2 e eliminar determinadas inclusões não metálicas.
O aço fundido descarbonetado no conversor é injetado numa panela e transportado para o equipamento de vazamento contínuo para ser fundido (placa, bilete ou bloco).
O gás árgon é vertido na panela para evitar a oxidação do aço fundido.
É necessário monitorizar o oxigénio para garantir que não existe oxigénio no interior da panela.
As placas de aço são aquecidas no forno de reaquecimento (800°C a 1000°C), de modo a ficarem suficientemente moles para serem laminadas.
O controlo da combustão é necessário para levar o metal a uma temperatura que permita a sua transformação em condições óptimas de qualidade, produtividade e eficiência energética, reduzindo simultaneamente as emissões poluentes.
A placa é aquecida num forno a 1200°C para tornar o metal mais maleável. De seguida, é desbastada e esticada por esmagamento progressivo entre os cilindros do laminador. A tira de aço é transformada em bobinas ou chapas de 1,2 a 20 milímetros de espessura. As bobinas são depois objeto de uma segunda redução a frio para obter um produto tão fino como uma folha de papel (até 0,1 milímetros de espessura).
Durante estes processos, os componentes gasosos ligados ao potencial de carbono(CO2, CO, CH4, NH3,H2 ou O2) devem ser monitorizados e controlados.
Descubra como os analisadores de gás ajudam a reduzir os poluentes e a promover o desenvolvimento de energia limpa para um ambiente sustentável.
09 de junho de 2024